with azbil
azbil MIND
Creating new value through the renewal of production bases
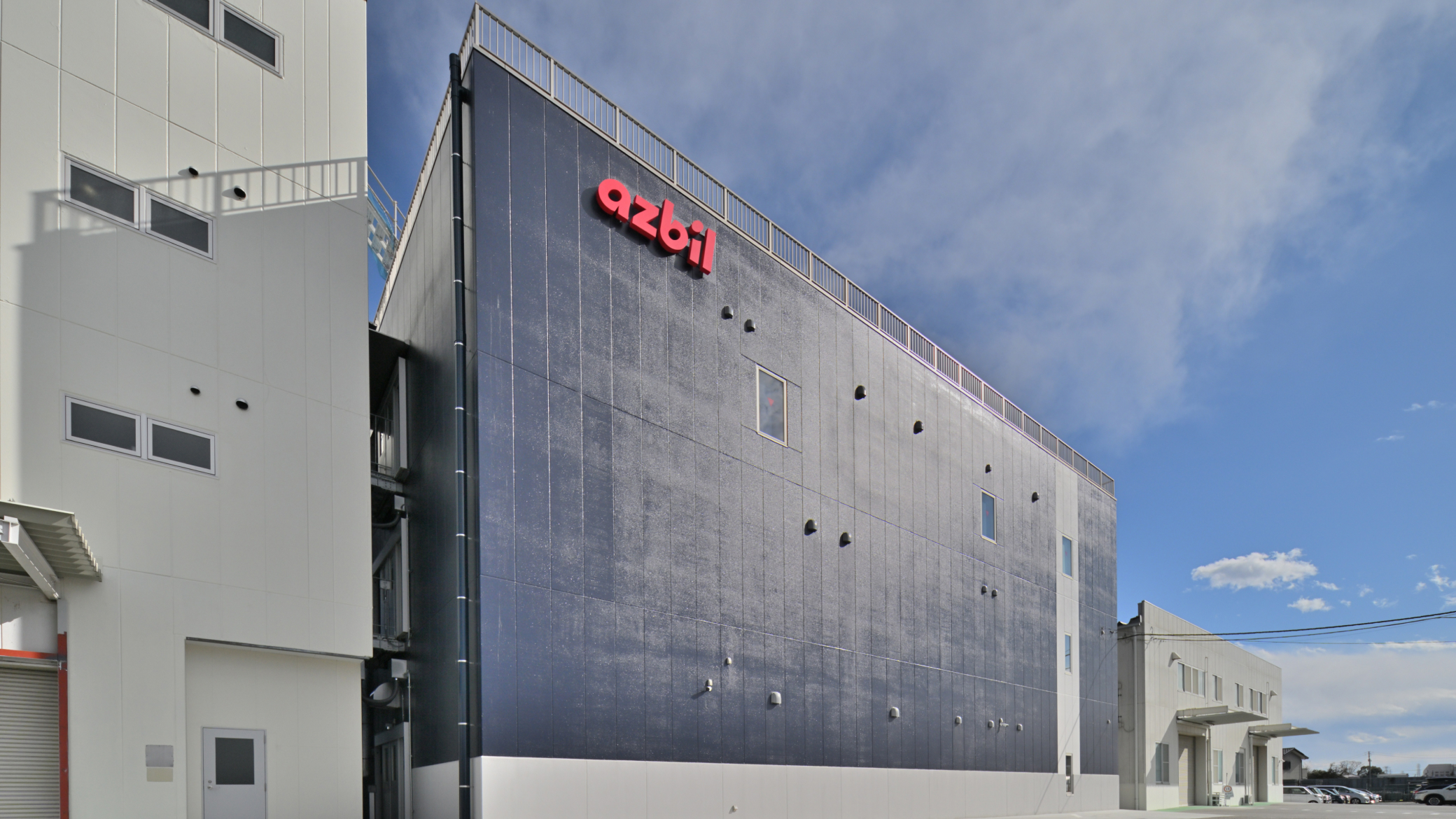
Pursuing the ideal factory that supports production innovation through
four tasks aligned with the construction of a new building
Azbil TA supports the production activities of industrial customers by providing products such as fog-type lubricators, dual valves, and pneumatic equipment. The company carried out a renovation of its long-standing main production base at the Saitama factory, centered around the construction of a new building. Through the initiation of four tasks during the renewal, Azbil TA is realizing new value creation by improving the efficiency of production and development, ensuring safety and security for employees, being environmentally conscious, and improving employee satisfaction.
Pursuing added value by implementing four tasks triggered by aging factory countermeasures
Azbil TA Co., Ltd. leverages its unique air-controlling technology to manufacture and sell equipment that supports the production activities of industrial customers in the fields of lubrication equipment, directional control valves, and pneumatic equipment. The company was founded in 1955 as Tokyo Automatic Control Co., Ltd., and in 1961 it set up its Saitama factory in Gyoda, Saitama Prefecture. In 1989, the company changed its name to TACO Co., Ltd. It joined the azbil Group in 2012, and in 2013, changed its name to Azbil TA to mark a new beginning.
The company’s main products include fog-type lubricators, which spray lubricant onto the rotating shafts of cutting tools to reduce frictional heat and wear. They also produce directional control valves that are installed in power presses to manage the discharge of compressed air for clutches and brakes. Additionally, the company offers customized pneumatic equipment used in semiconductor manufacturing, which requires a clean vacuum. Production is carried out at two bases: the Saitama factory and the subsidiary, Taco Seiki Co., Ltd. (Soma, Fukushima Prefecture).
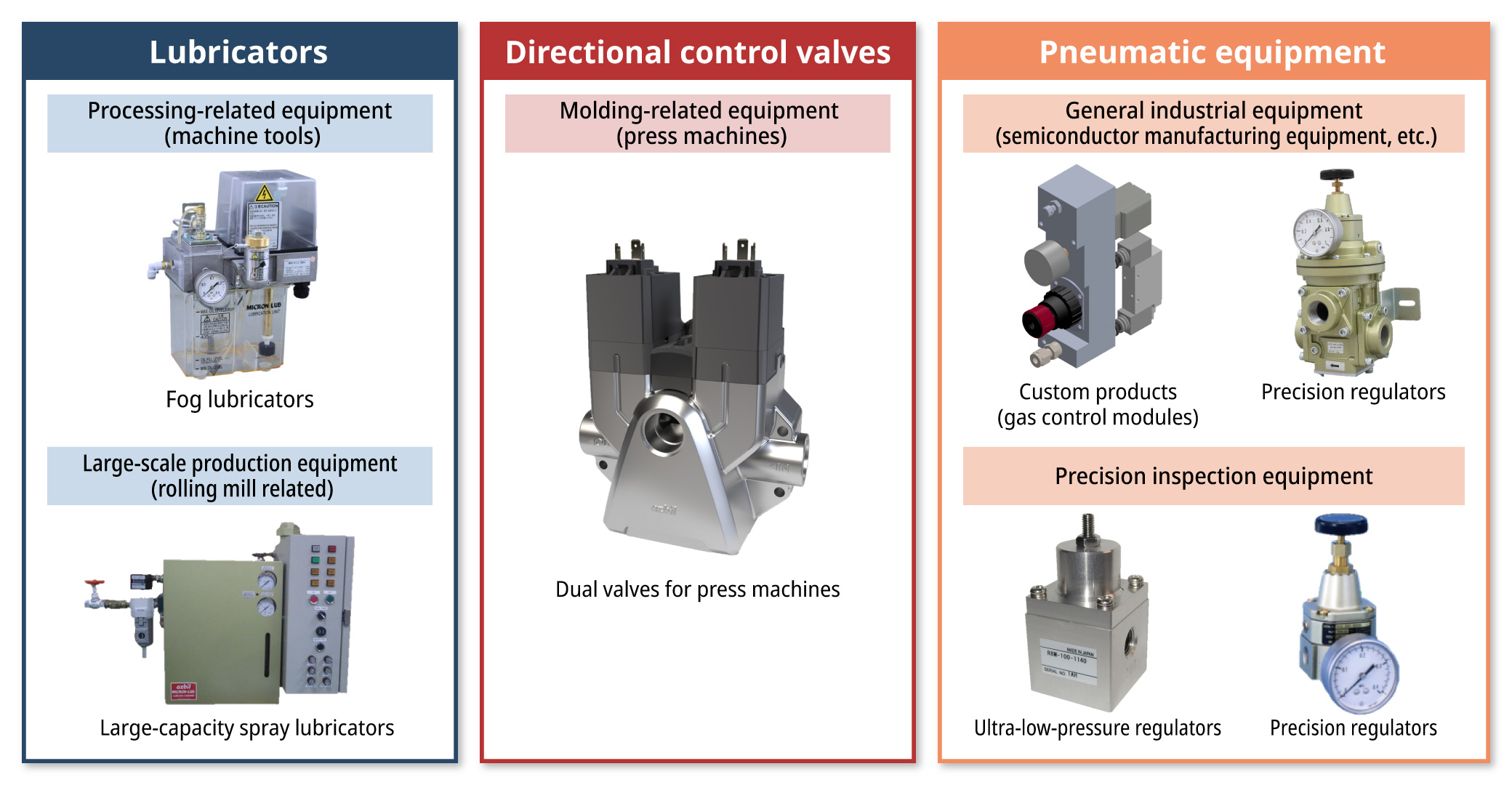
Since its inception, the Saitama factory, with a history of over 60 years as a main facility, had experienced noticeable aging in its buildings and auxiliary facilities. Ensuring seismic resistance in some buildings had also become a challenge. As part of our business continuity plan (BCP), the azbil Group is encouraging all business locations to relocate to buildings that meet new earthquake resistance standards or meet the reinforcement requirements. In response, Azbil TA decided in March 2020 to demolish the aging Building 2 and construct a new building, Building 10, on the same site, which complies with the new seismic standards.
In undertaking the renewal, they aimed to further enhance productivity through the construction of a new building, while also pursuing the realization of health and well-being management*1 and well-being, which are initiatives of the azbil Group. To achieve these goals, the project was organized around four tasks. Until now, due to building constraints, it was challenging to undertake various improvement measures related to production innovation. However, efforts are now being made to create an environment in which employees can work safely, securely, and comfortably. The new building, Building 10, was completed at the end of July 2024, and the Saitama factory has begun operations as a production base that supports the provision of new added value brought about by these tasks.
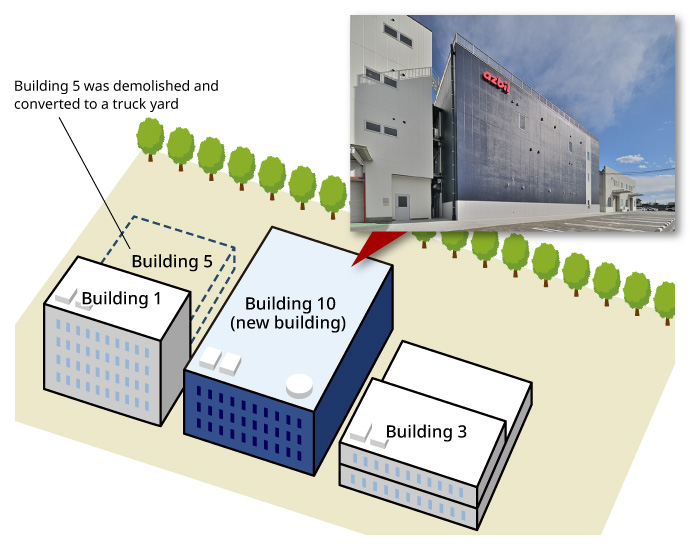
Rethinking outdated production methods and striving to realize an ideal model
The first of the four tasks in the Saitama factory renewal project was the “production system establishment task.” Given that the Saitama factory serves as the central production base for Azbil TA, the goal was to establish a new production system with an eye on the future. By completely restructuring the outdated production line and shortening the movement of goods within the factory by 50% compared to the previous system, the lead time from product order to shipment was effectively shortened.
The company has also identified the need to gradually narrow down its product lineup, which currently consists of an enormous number of items, to an optimal number. By reviewing the product lineup, it becomes possible to utilize the space required for production and inventory more efficiently, as well as optimize the operations and skills associated with product management.
The second task was the “factory construction task.” This measure aimed at creating a production base that is safe, secure, comfortable, and easy to work in, and that also contributes to the local community. It also involved consideration of the local environment and neighboring residents, including reducing CO2 emissions and preventing noise pollution. Initiatives included transitioning to LED lighting for energy savings and improving insulation by reducing the number of windows. Additionally, out of consideration for neighboring residents, the company is replacing compressors, which are frequently used in production to generate compressed air, with energy-efficient and low-noise models to prevent noise pollution. Furthermore, a system has been established to utilize the heat emitted by compressors by recirculating it within the factory for heating purposes. The company has also installed a system to monitor electricity usage by installing power meters for each line within the factory, creating an environment that further accelerates energy-saving efforts.
As a result of these measures, the Saitama factory achieved a reduction in CO2 emissions by 31% and a unit-based reduction of 33%, on average, from August to October 2024, compared to the fiscal 2019. Further reductions are achieved in winter when waste heat can be reused.
The third task was the “technical center construction task.” This involved completely renovating the development department’s laboratory, which was located in Building 3, and transforming it into a brighter, more comfortable working environment. The renovated development and testing environment has been named the Saitama Technical Center and is being equipped as the development base for all the products manufactured by Azbil TA.
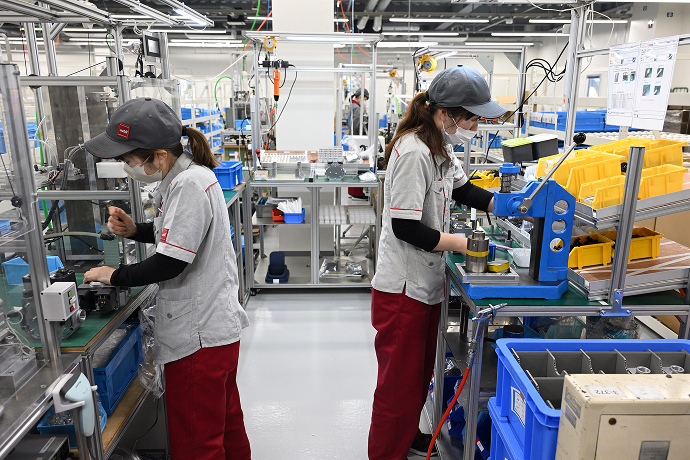
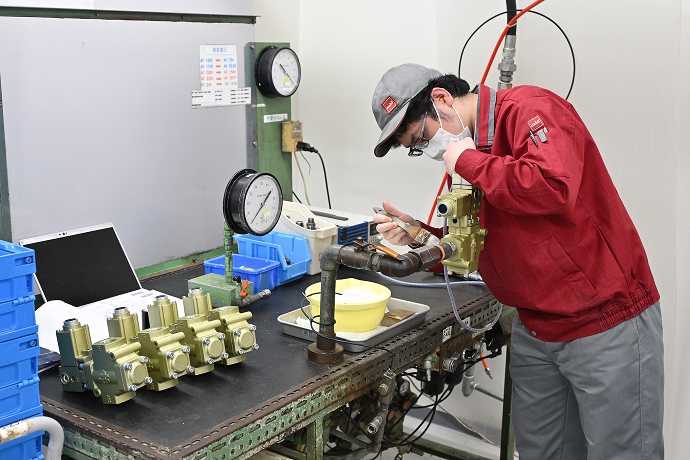
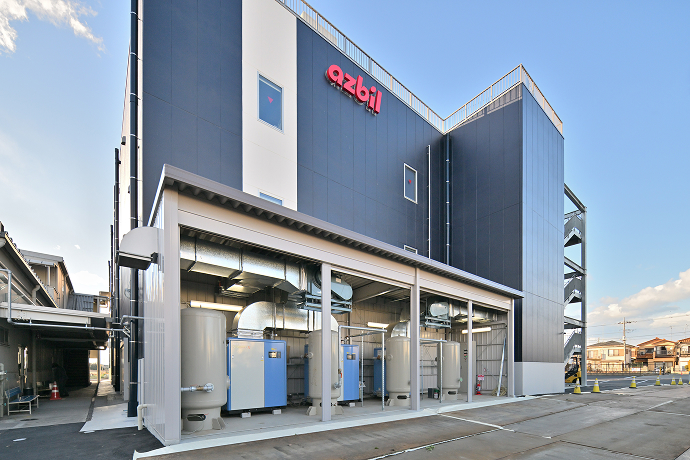
*The shutters are usually closed for noise reduction purposes
Creating a pleasant work environment by collecting feedback from the workplace
The fourth task, the “employee satisfaction improvement task,” was a major initiative aimed at enhancing added value in this factory renewal. In contrast to the three tasks introduced so far, which focus on tangible improvements like building a production system and creating an environment that ensures safety, security, and comfort, this initiative emphasized the intangible aspect of enhancing employee satisfaction.
Specifically, task members from each department within the factory conducted surveys and other activities at their respective sites to identify the issues employees were dissatisfied with. They gathered opinions on how to enable employees to work more comfortably and proceeded with efforts to create a more pleasant working environment.
A symbolic achievement of these efforts was the creation of a space called the Green Lounge on the third floor of Building 1. The Green Lounge primarily takes on the traditional role of a dining hall, but it is adorned with many potted plants, creating a comfortable environment where employees can relax. Employees use it not only for meals but also for breaks, meetings, occasionally for desk work when they need a change of scenery, and meetings with clients. It serves as a venue for communication among employees and greatly contributes to fostering new ideas and creativity.
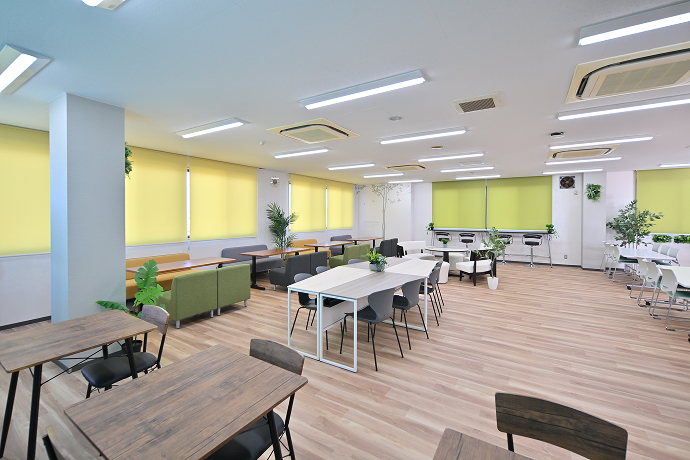
The cafeteria in Building 1 has been transformed into the Green Lounge,
serving as a place for employee communication
The renewal project for the Saitama factory was completed in December 2024, allowing Azbil TA to establish an environment to implement production innovations for the future. We have high expectations that the improved work environment will contribute to the well-being of employees and lead directly to providing higher value to our customers’ production activities.
- *1: Health and well-being management
In July 2019, the azbil Group defined its comprehensive initiatives for work style reform, diversity promotion, and enabling employees to work healthily and energetically as “Health and Well-being Management” and announced the “azbil Group Health and Well-Being Declaration.” - *This article was translated from the Japanese version of the article published on March 28, 2025.