Meeting the Needs of the Times with Groundbreaking New Products
Taking on challenges in the areas of performance, safety, environment, and design to create new dual valves with high value to customers
Since its founding as a manufacturer specializing in pneumatic equipment, Azbil TA has supported industry in Japan and overseas for many years with its unique aircontrolling technology. The company recently put a new dual valve on the market that provides new value for customers and meets current needs for performance, safety, environment, and design.
- An overwhelming market share for dual valves, the “heart” of mechanical presses
- Shooting for No. 1 worldwide in performance, and meeting a variety of needs in a new era
- Sophisticated design to communicate high product value
An overwhelming market share for dual valves, the “heart” of mechanical presses
Azbil TA Co., Ltd., was founded in 1955 as a manufacturer specializing in pneumatic equipment. The company, which joined the azbil Group in November 2012, has supported industry in Japan and overseas for many years with its unique air-controlling technology. One of the pillars of the company’s business is direction control valves, including dual valves.
Presses are used to process a wide variety of parts, from automobile bodies to parts for personal computers, smartphones, and even coins. Presses can be categorized as mechanical or hydraulic, according to the power source for pressurization, and dual valves are used for mechanical presses. A mechanical press transfers the rotational force of a flywheel driven by a motor to a crankshaft via a clutch, converting it into linear motion to move a metal mold up and down, sandwiching a metal plate for processing. In this process, the dual valve controls the timing at which the metal mold is moved up and down, and it can be said to be the heart of the mechanical press.
Azbil TA put its first dual valve on the market in 1979. From the outset,the company had a strong desire to expand into overseas markets, and actively promoted the supply of its products to press manufacturers in Taiwan, where the press industry was just beginning. Afterward, the production of presses moved to China, where industrialization was progressing rapidly, and Azbil TA’s dual valves, which had become the standard in Taiwan, began to be incorporated into presses made in China.
Today, they are used by major manufacturers in China, the center of press production, and are supplied worldwide with more than half of the world’s newly produced mechanical presses.
Shooting for No. 1 worldwide in performance, and meeting a variety of needs in a new era
In recent years, the requirements for dual valves in mechanical presses have been changing. In addition to requests for improvements in basic functions to protect the safety of workers, such as a faster time for reliably stopping the press and reduction of residual pressure in the case of a failure, there is a rapidly increasing demand for environmentally friendly design, an unavoidable theme in modern industry.
In response, Azbil TA decided to dramatically revise the products it had been providing for about 40 years, since their introduction in 1979, in order to provide even safer and more environmentally friendly products. The company embarked on the development of new products with the goal of being No. 1 in performance worldwide, and began supplying the upgraded dual valve model TX-A, (hereafter “the TX-A”), in May of 2020.
In planning and development, the company focused on three major points. The first was to achieve faster and safer operation, aiming for the highest performance among dual valves of the same size and price. A mechanical press works by using air pressure to manipulate the transmission of power from the clutch. In an emergency, it is necessary to quickly release this air pressure, cut power transmission from the clutch, and quickly stop the machine. For the TX-A, a unique L-shaped cross-flow channel for the compressed air was developed, which was an improvement over the previous cross-flow channel. The new channel design made it possible to stop the mechanical press more quickly in an emergency like a single-sided valve failure, greatly enhancing the safety of the operator.
The second point for development was environmentally friendly design. For the TX-A, efforts were made to use molded plastic parts and aluminum die-cast parts, and to consolidate functions to reduce the number of parts. The result was an approximately 22% reduction in weight and approximately 41.4% reduction in resource use. Furthermore, by more optimal design of the coil, pilot valve, and main valve, which are the main mechanical elements of the dual valve, the company has reduced power consumption by approximately 50%, contributing to energy conservation at the end user’s manufacturing site. In addition, due to this design, the TX-A has achieved a LC-CO2*1 reduction of approximately 51.7% compared to conventional products.
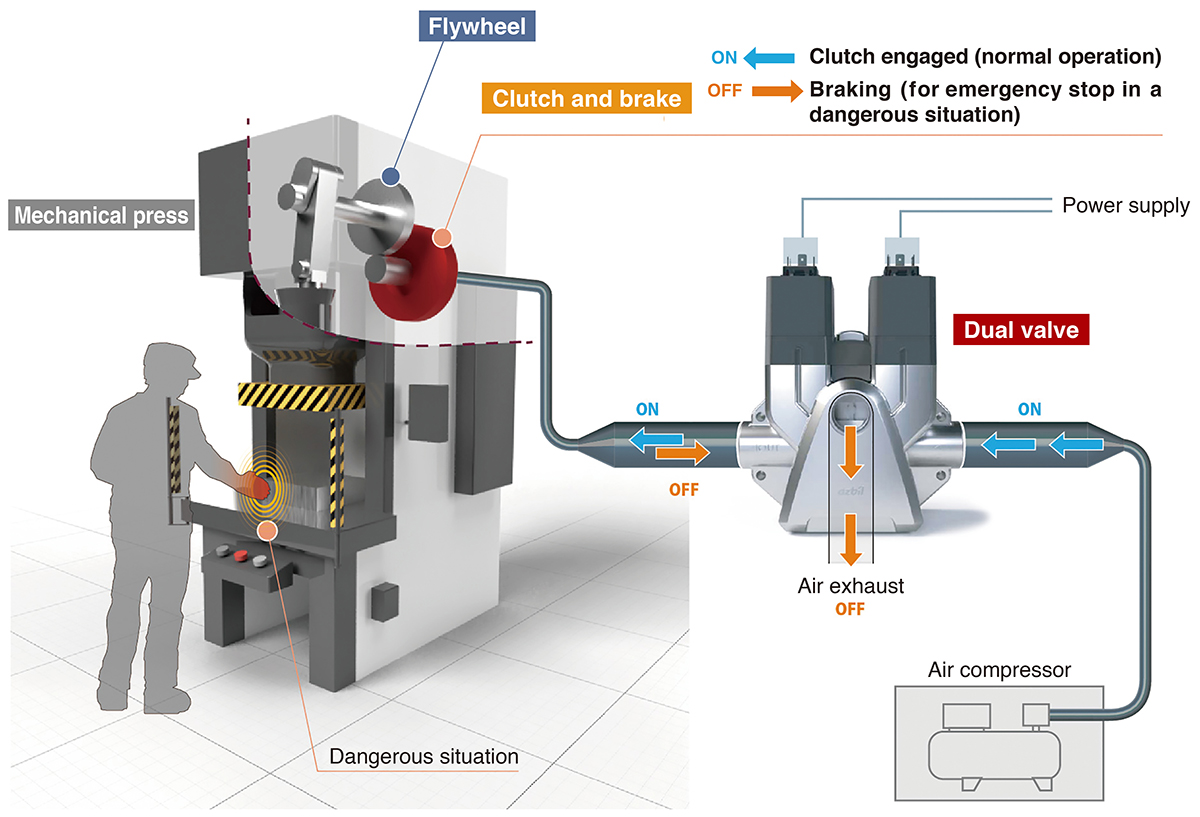
Dual valve operation
Sophisticated design to communicate high product value
The third point for development was the synergy of best function, best performance, and best design. Conventional dual valves prioritize function and performance over design, but with the TX-A there was focus not only on function, but also on a new and more sophisticated design. For example, the green-gold color of Azbil TA products was widely recognized by overseas press manufacturers and end users as a symbol of safety and high quality. But with the TX-A, considering the environmental impact of painting, the design along with the product color was revised. With the cooperation of designers with a wealth of experience in the field of industrial products and Azbil’s design management department, the company sought a product design that more effectively communicated the value of Azbil TA’s dual valves. The current design expresses novelty, precision, and robustness. In addition, with the new product design, the redundant dual-valve configuration and cross-flow structure can be understood from the exterior, embodying the idea that form follows function. The TX-A has been rated highly by customers and others, and won a Good Design Award*2 in 2021.
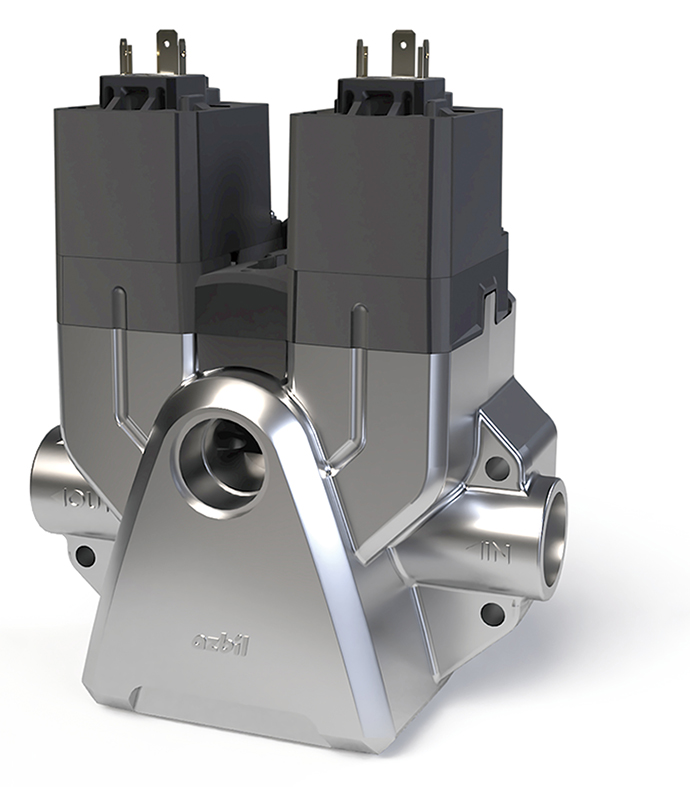
Model TX-A Dual Valve
Conventional dual valves made by Azbil TA and installed in presses are now being steadily replaced with the TX-A, some 30% in 2022 and an estimated 60% in 2023.
Azbil TA plans to expand sales channels and strengthen its service system in line with the expansion of the Chinese market and the expansion of production in emerging countries. In addition, the company would like to apply the knowledge and experience gained from upgrading the dual valve to other product groups, including fog-type lubricators, in order to provide further value to customers.
*1 LC-CO2 (life cycle CO2)
The total amount of CO2 emitted over the life cycle of a product, from planning, production, and operation to dismantling.
*2 Good Design Award
The only system in Japan that comprehensively evaluates and honors design. The aim is not competition on beauty, but acknowledgment of leadership in the development of industry and in the improvement of the quality of life.
This article was published on June 30, 2023.