Calibration
In the area of measuring instruments, calibration maintains an instrument’s accuracy by comparing it with a more reliable standard instrument and clarifying the differences between the two.
- Calibration of Measuring Instruments Affects Product Quality
- Accuracy of Calibration Improves as Standards Become More Highly Accurate
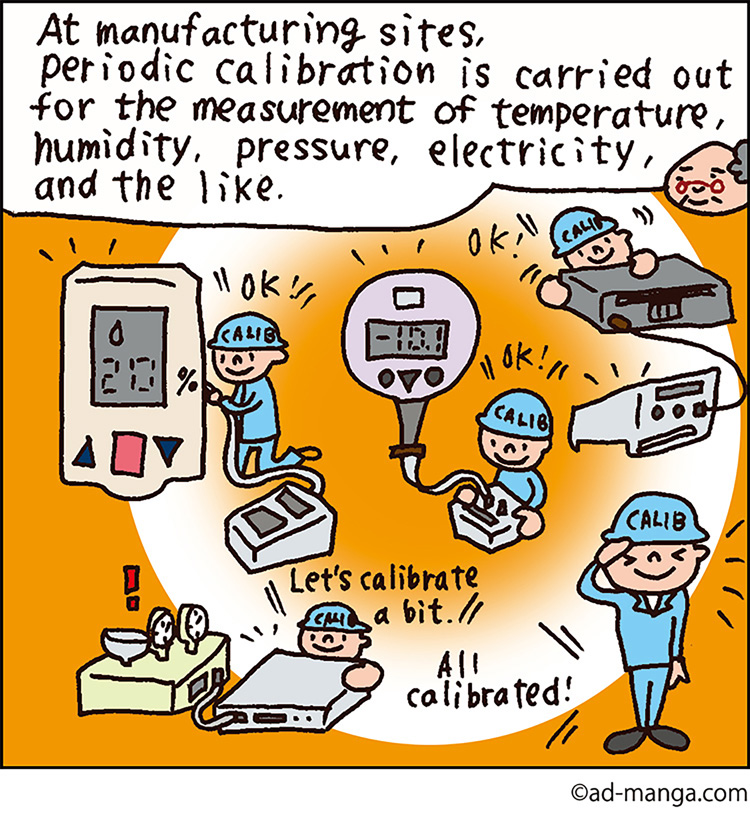
Calibration of Measuring Instruments Affects Product Quality
When you weigh a thing, if the instrument says “100g,” you will probably accept that it weighs 100 grams. But what if the instrument is not displaying an accurate number? Here is a familiar example. If your bathroom scale does not show the proper weight when you are working hard on a diet, you cannot see the effects of the diet.
So, the accuracy of measuring instruments is important, and particularly so in the field of manufacturing. Measurement is carried out in various contexts at production sites, including manufacturing, processing, maintenance, and pre-shipment inspection. If measuring instruments are not accurate, product quality and safety cannot be ensured.
Calibration is done to check that measured values are accurate. (The term calibration, however, is used differently in other industries, such as IT or finance.
To check that measuring instruments are accurate, comparison is made with a standard instrument of higher accuracy. Of course, the standard instrument used for calibration must itself be reliable and highly accurate. It is calibrated with an even more accurate, higher level standard instrument. In this way, a chain of comparisons eventually reaches a national or international measurement standard. This is called “measurement traceability.” This kind of chain of calibration proves that the tested measuring instrument is accurate.
In Japan, there is a measurement traceability system called “the Japan Calibration Service System (JCSS).” JCSS is the system that accredits calibration laboratories. The system was introduced by the Measurement Law to improve quality control, etc., by ensuring the reliability of measurements. Also, if a calibration laboratory is accredited by an international Mutual Recognition Arrangement (MRA), calibration results measured by the laboratory in Japan are accepted in MRA member countries in Europe, America, and Asia.
Accuracy of Calibration Improves as Standards Become More Highly Accurate
If measuring instruments were always accurate, calibration would not be necessary. However, parts deteriorate and wear out over time, which makes it difficult to maintain accurate measurement. Moreover, even though measuring instruments are maintained and managed properly, if they are used incorrectly, they will be unable to measure accurately.
That is why periodic calibration is essential. A calibration cycle should be determined for each measuring instrument in order to check that it is measuring accurately.
As the capabilities of industry improve, measuring instruments can measure more accurately. Take a look at rulers, which are measuring tools, as an example. Some rulers can now measure down to the micron level. They are made from materials that are almost unaffected by the environment and are etched with fine graduations or are digitized.
Even increased precision and management of measuring instruments does not always ensure accurate measurement, so an engineer with expert measurement knowledge is indispensable for calibration.
For example, a measurement (numerical value) may vary according to the environment or measurement method. If the same person is weighed in Japan and in Africa, the weight (the measured value) will not be the same, because the gravitational acceleration differs depending on the place on the Earth.
So, unless the person who is calibrating has a deep knowledge of measurement principles and takes into account environmental changes and other factors, accurate calibration cannot be carried out.
The accuracy of measuring instruments can be maintained because technicians possess a knowledge of physics, mathematics, and statistics that enables them to continue to calibrate accurately and honestly.