Cavitation
A series of phenomena in a flowing liquid including the formation of vapor bubbles due to decreased pressure, the implosion of those bubbles when pressure rises, and the return of the bubbles to liquid.
- Shock waves and microjets gener ated by flowing liquid can cause the destruction of pipes and valves.
- Methods for preventing cavitation damage and technologies for detecting signs of cavitation
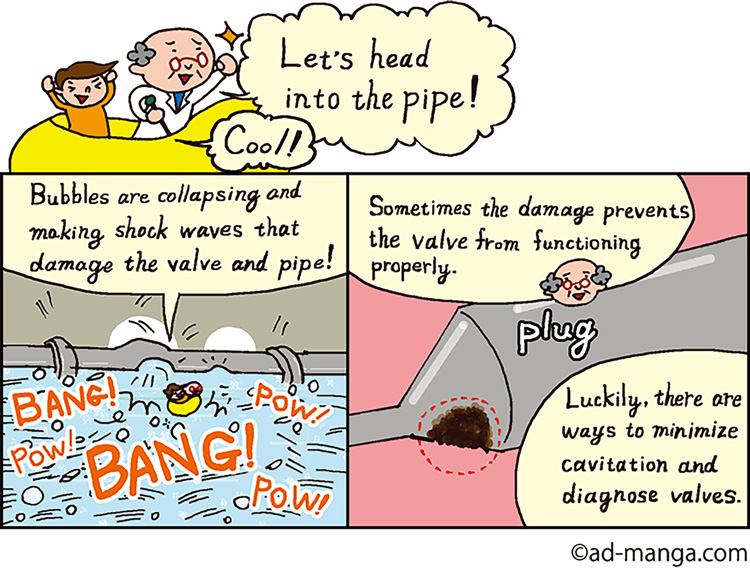
Shock waves and microjets gener ated by flowing liquid can cause the destruction of pipes and valves.
Cavitation refers to a series of phenomena in a flowing liquid, such as water or petroleum, including the formation of small bubbles (vapor bubbles), the implosion of those bubbles, and their return to liquid. When cavitation occurs, there is a shock wave or strong local jet of liquid that gen erates vibration and noise in the pipes or connecting valves. This gradually causes fatigue fracture (cavitation damage) of the liquid-contacting surfaces, which eventually becomes a serious problem.
Cavitation is triggered by the pressure changes in the flowing liquid, which occur at various places inside the pipe. A change in pressure causes the formation of vapor bubbles because it reduces the boiling point of the liquid. Under normal atmospheric pressure, water boils at 100 ℃ and produces vigorous bubbles. The boiling temperature of water is the boundary temperature at which liquid water changes rapidly to vapor, forming vapor bubbles.
In the case of factories and power generating plants, liquids in pipes are under pressures of several tens to several hun dreds of atmospheres in order to efficiently transport the liquids and to drive turbines at high speeds using high differential pressures. Consequently, liquids in the pipes of factories and power generating plants tend to experience sudden changes in pressure.
In particular, valves that are used to adjust the pressure or flow rate of liquids in pipes constrict the area through which the liquid passes. This increases the flow speed of the liquid in the pipe and creates conditions prone to cavitation. According to the energy law governing liquids, an increase in flow velocity decreases the pressure, and therefore the boiling point is lowered, causing vaporization of the liquid and the formation of vapor bubbles. Bubbles formed by cavitation can sometimes have high energy※ in spite of their small size, and can completely destroy even the hard stainless steel plug in a valve in about 10 hours in some cases.
Methods for preventing cavitation damage and technologies for detecting signs of cavitation
If many vapor bubbles are formed continuously in a liquid for an extended period of time, cavitation damage can progress in the valve, eventually preventing accurate regulation of the liquid pressure or flow rate. In the case of a manufacturing factory, this results in quality problems in the product. Before long, the valve becomes unable to close properly to stop the flo of the liquid, or the pipe ruptures when it is no longer able to withstand the pressure.
There are countermeasures to the problems caused by cavitation. Cavitation damage can be prevented by using a plug made of a material that is hard to break, or by using valves that incorporate a specially designed internal structure to minimize internal pressure changes.
In order to detect cavitation damage occurring inside of valves and pipes, in stallation of a maintenance support system enables maintenance engineers not only to monitor the condition of the valve but also to determine the appropriate replacement period for the valve by means of a valve positioner equipped with diagnostic functions.
※Theoretical calculations show that a bubble of 1 μ(1 micrometer = 0.001 mm) in size can generate a local pressure of 90 atmospheres and a high temperature of about 570 ℃ when it collapses.