PID Control
This type of feedback control operates on the basis of sensor measurements in order to keep the temperature, pressure, and other variables inside of manufacturing or processing equipment at the desired levels. PID refers to proportional, integral, and derivative action.
- To maintain product quality, manufacturing processes require strict temperature control.
- A widely applied fundamental method of automatically controlling temperature, flow, pressure, etc.
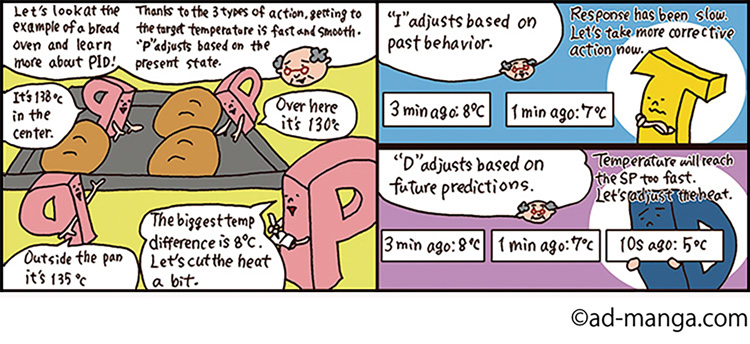
To maintain product quality, manufacturing processes require strict temperature control.
In factories and plants, very precise temperature control is often needed to manufacture products such as semiconductors. If a heater is simply turned on and off (ON-OFF control), the temperature fluctuates significantly, overshooting the setpoint or causing other problems. Reliable control is difficult to achieve. To solve this problem, PID control, which is a kind of feedback control, is used.
A widely applied fundamental method of automatically controlling temperature, flow, pressure, etc.
PID control consists of the three components of proportional, integral, and derivative action.
First, proportional action, which is basic feedback control, changes the output (called the manipulated variable or MV) of a heater, etc., in proportion to the amount of deviation from the setpoint or SP (deviation = SP . PV [the process variable, for example the current process temperature]). This is done within a preset “proportional band” (the range of allowed temperature or pressure change). Depending on the amount of deviation between the preset temperature and the current temperature in the proportional band, the output is increased or decreased so that the temperature reaches the target. If a wide proportional band is set, control operation is relatively slow. Reaching the target temperature takes more time, but overshoot of the target and temperature fluctuation can be prevented.
Next, in contrast to proportional action, which operates based on a preset proportional band, integral action adjusts the control input according to the surrounding environment. For example, in the case of a heating furnace, once the furnace has heated up, 100% output of the heater may not be necessary. In this case, integral action decreases the output.
Finally, derivative action changes the amount of control output (MV) by adjusting the proportional band, depending on the latest change in temperature. For example, when the temperature is falling, rapid heating is necessary. On the other hand, when the temperature is rising, derivative action can reduce the risk of overshooting the temperature target by suppressing the MV.
These three actions together can maintain reliable control, preventing significant temperature overshoot and undershoot and repeated ON-OFF action. As a result, the optimal temperature can be reached rapidly.
PID control is widely applied not only for temperature, but also for flow rate and pressure, etc. It is an indispensable technology for all kinds of automatic control.