Validation
When validation is used in connection with the manufacture of pharmaceuticals as a technical term, it refers to the process of establishing scientific evidence demonstrating that the manufacturing system, including processes and equipment, can consistently deliver the expected product quality.
- Scientific examination to confirm the soundness of procedures and rules for drug manufacture and quality management
- Documentation is also essential to make evidence accessible to others
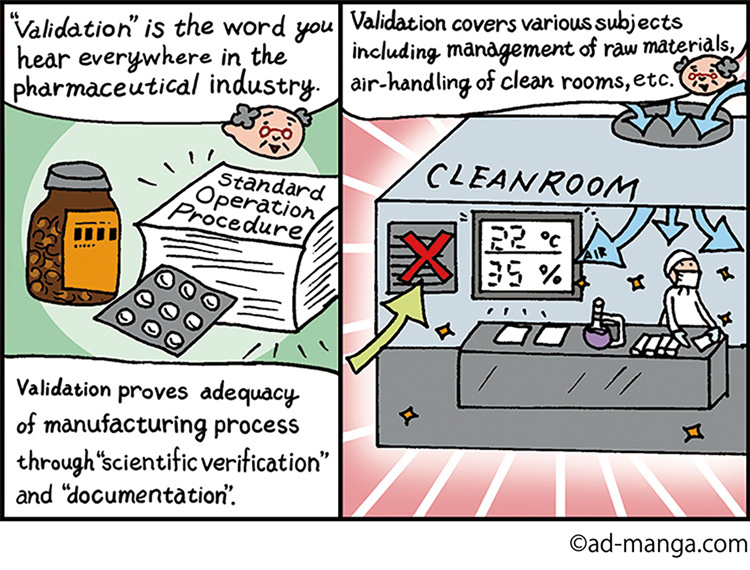
Scientific examination to confirm the soundness of procedures and rules for drug manufacture and quality management
Drugs for sickness and injuries can roughly be categorized into two kinds: over-the-counter drugs sold in pharmacies, and prescription drugs. Both kinds must be manufactured so as to always have quality as intended. What if each tablet contained inconsistent active ingredients (the chemical substances that cause the medicine’s effects)? Patients would not feel that the medicine was safe to take.
For that reason, many countries in the world establish GMP※ guideline defining the requirements that drug manufacturers must meet in managing manufacturing process and product quality. Such guideline requires the manufacturer to document the manufacturing procedures and to follow them for the purpose of 1) minimizing human error, 2) preventing contamination and degradation of quality, and 3) establishing a system for assuring high quality.
The GMP guideline prescribes an activity called “validation” for assuring drug product safety. Validation in this context means examining each stage of the process, from receiving raw materials to shipping the finished products, in order to verify that all stages of the manufacturing process meet the predefined specifications. Without collecting objective evidence that warrants that safety of the finished products is assured, manufacturers cannot demonstrate that their drugs were properly made by proper process.
Validation consists of two major activities. The first is to verify “through scientific approaches” that procedures and the equipment used are fit for manufacturing drugs.
Drug manufacturers need to identify all the risks with the procedures, facility, and equipment (potential variables) and eliminate them to achieve consistency.
For example, for the process step to mix multiple ingredients, an ingredient may be weighed wrongly, mixing time may be too short, or the mixer may be contaminated and impurities may make their way into the product. To minimize such risks, the measurement procedures, mixing specifications (including time), and equipment cleaning procedures are tested to verify their appropriateness.
Temperature and humidity control is also essential because many pharmaceutical in gredients are powders that are sensitive to temperature and humidity changes. To prevent the risk from increasing, the control of the air-handling equipment must be verified. The control records are used as part of the evidence to demonstrate the equipment is fit for the drug manufacturing.
Documentation is also essential to make evidence accessible to others
The other major validation activity is documentation. It is an activity to record the data and to ensure it is accessible to others.
When drugs are manufactured, ingredients, apparatus, equipment, operators, operations, and plant environment (temperature, humidity, etc.) must all be recorded so that the adequacy of the entire manufacturing system can be ensured and, when a problem occurs, the cause can be tracked.
Today, pharmaceutical manufacturing plants are increasingly adopting computers for control of the manufacturing process, product quality, manufacturing equipment, and analysis. Such computers must be validated, and that practice is called “computerized system validation” (CSV). Patients can take medicine with no fear when these good practices are performed by drug manufacturers. Validation activities, through tireless efforts by the manufacturers, are like an invisible warranty card that comes with a pharmaceutical product.
※ Acronym for good manufacturing practices. The Food and Drug Administration (FDA) of the US government was the first to define GMP regulations. Later the World Health Organization (WHO) developed their GMP, and many different countries started to adopt them.