Striving for Higher Product Value Through Improved Design Quality
Using a knowledge database to bridge our development departments and share the information needed to prevent defective products
As part of its efforts to improve product quality, Azbil has created a knowledge database about defects and their causal mechanisms, based on the Stress-Strength Model (SSM)*1 proposed by the Institute of Structured Knowledge Yielding Co., Ltd. The various product development departments use this knowledge so that products and production processes can be designed from a broader perspective to avoid nonconformities and similar problems. We are working to further enhance our systems and further improve the value of our products for our customers.
- Using SSM to transform data about nonconformities into knowledge that is useful in the design process
- Useful also for design review, nonconformity response, and technology transfer
- Sharing design knowledge across the company gives designers new insights
Using SSM to transform data about nonconformities into knowledge that is useful in the design process
The azbil Group’s philosophy is to bring about safety, comfort and fulfillment in people’s lives through “human-centered automation.” We strive to provide value through products and solutions based on advanced measurement and control technology in the Group’s business segments of Building Automation (BA), Advanced Automation (AA) and Life Automation (LA), with the goal of solving the ever-changing problems of our customers and society.
One of our main missions is to maintain and improve quality in order to meet the expectations and needs of our customers. To achieve this, for many years we have taken company-wide measures to make everyone fully aware of the need to improve the quality of the products provided by each business unit and the quality of our engineering, maintenance support, and other services, as part of our corporate culture.
In recent years we have placed particular emphasis on an initiative to ensure quality craftsmanship in product design and in the design phase of production processes. Until now, information about defects found at customers’ sites and during the production and development process was scattered among the product development and production engineering departments of individual business segments. This information is now unified, structured (generalized) and modeled (converted into knowledge) so that it can be reused in an organized form. Now, before starting a design, all development departments can access knowledge about nonconformities and the like that occurred in the past, and can create a framework for producing an efficient and high-quality design.
For the methodology of structuring this knowledge, Azbil has adopted the SSM approach proposed by the Institute of Structured Knowledge Yielding. Based on this model, knowledge about possible defects and nonconformities in products and processes is put into a database using SSM™ Master, which is nonconformity prevention software. The idea is to aid the design of products and production processes.
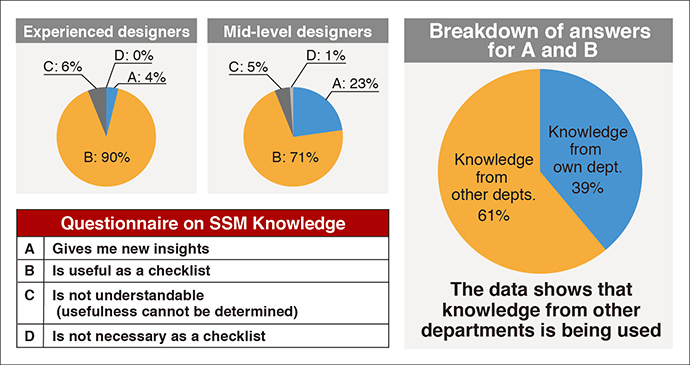
Evaluating the usefulness of knowledge classifications
Useful also for design review, nonconformity response, and technology transfer
Azbil first tested this approach in its control valve development department. Starting around 2010, Azbil began capturing data with SSM Master with the help of the Institute of Structured Knowledge Yielding, and in spring 2012, the department began using the system. After receiving a positive impression of the system, the next step was to consider inputting the knowledge accumulated since 2012 by the company’s key development departments into a database across the company. In spring 2015, the database created by SSM Master was renamed “Azbil Design Knowledge Database” and was put into operation throughout the company.
At the same time, the Design Knowledge Database Operation Subcommittee was set up consisting of approximately ten members appointed by the development department of each business unit to promote the use of the Design Knowledge Database in internal development work
With the introduction of the Design Knowledge Database, design engineers can learn about past problems, their mechanisms, and design considerations for the product currently being designed and its components before beginning product development. The database can be used to improve design quality and prevent problems by providing a multi-perspective view of the product being designed.
In addition, Azbil uses the database not only for design work, but also as a source of reference information if required by reviewers when conducting design reviews and for troubleshooting if a product nonconformity is found in the field or in the production process. There are also plans to actively use the database to pass on skills to younger designers.
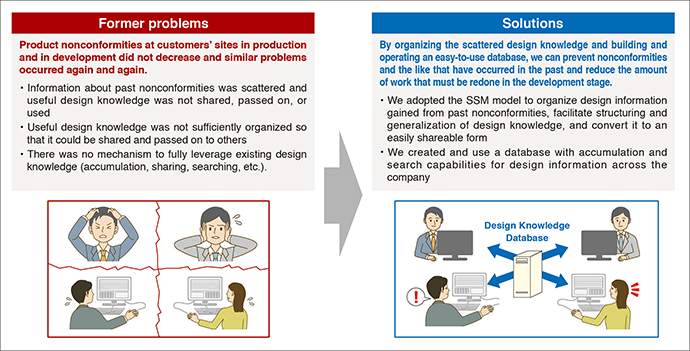
Background and purpose of the Azbil Design Knowledge Database
Sharing design knowledge across the company gives designers new insights
A key feature of Azbil’s Design Knowledge Database is that design knowledge related to products within the company is consolidated into a single common database for all business units and departments. As design engineers are exposed to knowledge from other departments, they can gain insights into ways to improve design quality that go beyond the information they have accumulated in their own department.
In order to share this design knowledge across the company, the Design Knowledge Database Operation Subcommittee works to standardize the definition attributes selected when searching the database and to consolidate variations so that designers can find the knowledge they need without having to enter the precise terms used previously. Also, to improve the accuracy of the input information, a system was created that checks the knowledge contributed by each business unit’s development department when it is entered into the database, so that only information whose usefulness has been carefully checked is input.
When users were surveyed about the usefulness of the company-wide Design Knowledge Database, in one development department over 95% of designers with more than 15 years of experience and middle-level designers with about 10 years of experience responded that they gained new knowledge and that they found the database useful as a checklist.
When asked whether the knowledge they gained or found useful came from their department or other departments, 39% said it was their department’s knowledge, while 61% said it was other departments’ knowledge. This shows that designers see great benefits in sharing knowledge within the company.
Going forward, Azbil will continue to expand and improve the Design Knowledge Database while encouraging the development of personnel skilled in SSM knowledge structuring in each development department to make even better use of the database. At the same time, there is a desire to showcase examples of departments that are using knowledge more effectively in their day-to-day work across the company, and to compile these examples as company best practices. Through these activities, it will be possible to continually improve the quality of Azbil’s products and to further increase their value to customers.
*1 Stress-Strength Model (SSM)
The SSM is a model for organizing and expressing knowledge about the mechanisms that lead to potential problems in products and processes. The model is intended for use in future design and planning.
SSM is a trademark of Institute of Structured Knowledge Yielding Co., Ltd.
This article was published on October 1, 2021.