Ensuring Safe and Consistent Operations of Plants and Factories Across Japan By Reinforcing Valve Maintenance Systems and Providing IoT-Based Services
With the aim of helping plants and factories to reinforce their valve maintenance systems, Azbil Corporation has installed five valve maintenance centers in Japan and established a system that enables the centers to help each other by dispatching maintenance staff and sending equipment. Thanks to this system, the centers can provide cross-regional valve maintenance services, and by also providing IoT-based valve diagnosis services, they help to ensure the safe and consistent operation of customers’ plants and factories.
- Providing high-quality maintenance services, backed by a history of achievement in valve manufacture and maintenance
- With five maintenance centers, a flexible system covers all of Japan
- Valve diagnosis services provided by fusing maintenance and IoT technologies
Providing high-quality maintenance services, backed by a history of achievement in valve manufacture and maintenance
Guided by its corporate philosophy of “human-centered automation,” the azbil Group develops products and services using its control and measurement technologies. One of its core areas of business is advanced automation, which ensures the safe and consistent operation of customers’ plants and factories and plays a role in improving the quality of customers’ products and the efficiency of manufacturing. Azbil equipment is used in various facilities for the production of oil, industrial chemicals, etc. Included in this equipment are valves. Since they control the flow rate and pressure of liquids and gases that are important for manufacturing, valves are essential devices for maintaining the quality of products and for consistent production.
Generally, industrial plants regularly halt all production lines every two or four years in order to maintain equipment functions and ensure consistent operation. During this periodic shutdown maintenance, large facilities and equipment are repaired and maintained. At this time, valves also undergo overhaul inspection. They are removed, disassembled, and cleaned. If necessary, old parts are replaced. With its expertise and specialized technology cultivated over many years of valve manufacture and maintenance services, Azbil can provide high-quality maintenance services not only for its own products, but also for valves made by other companies. This results in increased convenience for customers, as it eliminates the complication of requesting inspections from multiple manufacturers.
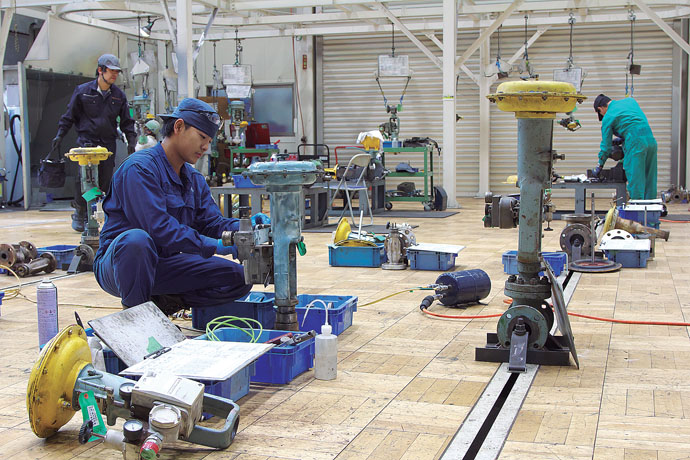
Valves are put on rails while being inspected, repaired, and maintained, in order to keep them upright. The new maintenance facility has added two more rail tracks, doubling the previous amount, and has improved its workflow to make overall maintenance performance highly efficient.
With five maintenance centers, a flexible system covers all of Japan
Azbil has bases in each region where many industrial complexes are located, so it can provide services to nearby customer sites by maintaining Azbil valves and other devices that are used. Since customers often wish to have their facilities undergo maintenance at the same time as the nearby ethylene plant, or they wish to shorten the maintenance period, valve inspection and maintenance orders tend to be concentrated in the same periods of time. To address these busy periods, Azbil established a valve maintenance center in each of its locations in the five relatively large industrial zones of Kashima, Chiba, Yokkaichi, Mizushima, and Kawara, and constructed a system for sharing staff, work space, and equipment in cases where one of the regions becomes busy with maintenance work, so any engineer can help with technical support to that region. Each center has an operational director who provides technical guidance and adjusts the workload among the centers when some are busy with maintenance work. In this way, by providing cross-regional solution-based services, the centers provide reliable maintenance across Japan.
The maintenance center at the Mizushima office in the city of Kurashiki (Okayama Prefecture) is the largest of the five and serves as the hub for the others. Receiving orders from the surrounding large industrial complexes, the center services a great variety of valves and has accumulated a corresponding amount of know-how.
When it relocated in February 2014, the Mizushima office expanded the size of its maintenance center, revised its workflow, and made its procedures more efficient. As a result, the office has successfully shortened the time necessary for maintenance and improved maintenance quality.
Furthermore, the location serves as a training site for engineers who are involved in valve maintenance work across the azbil Group. Many engineers visit from around the world and around Japan in order to learn management methods for finishing a large number of valves in a short time, or for hands-on practice of parts replacement skills that are difficult to learn from manuals. On top of that, the center has created a system for evaluating and visualizing engineers’ maintenance techniques to help them improve their skills. Azbil plans to establish an internal qualification system to recognize valve engineers who have reached a certain level as “highly skilled engineers.”
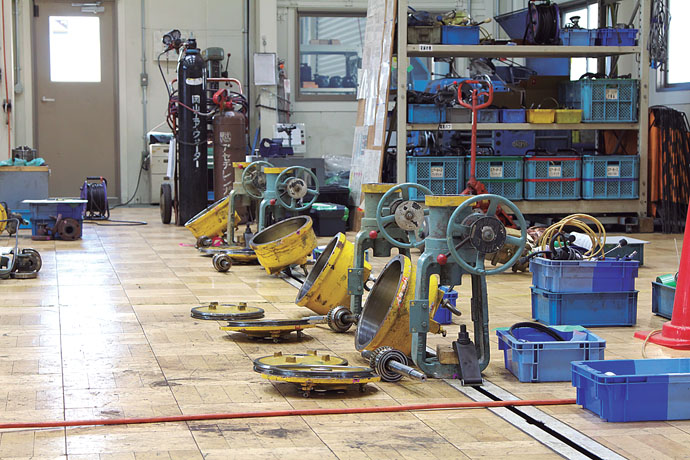
Disassembled valves from customers’ plants. The inside is cleaned and, depending on the amount of wear and deterioration, valves are repaired, parts are replaced, and coating is applied. Valves are restored to like-new condition and returned to customers.
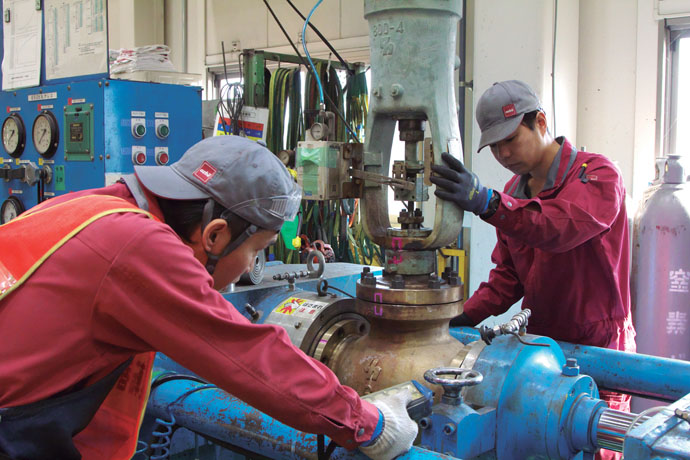
To ensure quality, engineers use specialized test equipment to check a variety of characteristics of repaired valves, including tests of pressure, airtightness, leakage, and operation.
Valve diagnosis services provided by fusing maintenance and IoT technologies
It is impossible to tell if a valve is worn out or degraded inside only by checking its appearance. Therefore, time-based maintenance (TBM), meaning that valves are inspected on a regular basis after a certain interval, is usually used. However, in recent years, a more efficient method called condition-based maintenance (CBM) has been attracting attention. In CBM, the condition of valves is checked without disassembling them, and maintenance is provided only to those valves that need it.
CBM is made possible by Azbil’s smart valve positioners, which not only control the opening and closing of valves but also measure their condition as they operate, and by a control valve maintenance support system called PLUG-IN Valstaff™, which can analyze data from the positioner and provide diagnosis. This IoT-based system can grasp the condition of every valve in real time and identify valves whose movement is abnormal.
Recently, many industrial plants face the problem of aging facilities and fewer experienced maintenance personnel, so it is important for them to find a way to take over or supplement veterans’ technical skills in order to ensure safe and consistent operations while improving productivity. From that standpoint also, Azbil’s smart valve positioners and Valstaff are useful, since they can supplement veterans’ techniques and reduce the workload of maintenance staff. From now on, Azbil will provide valve diagnosis services that make use of these smart valve positioners at overseas valve maintenance centers also.
Azbil Corporation intends to continue to provide speedy and high-quality maintenance services and high-value added valve diagnosis services using advanced technology in order to help its customers to operate their plants smoothly.
*1 Ethylene plant
A facility that generates ethylene, which is a raw material for
petrochemical products, and provides it to petrochemical
plants. Companies increasingly opt for joint operation by integrating
their facilities.
* Valstaff is a trademark of Azbil Corporation.
This article was published on July 1, 2017.