Loader-unloader uses a non-contact drive mechanism to eliminate problems associated with loading and unloading
Loader-unloader for freeze dryers
In some cases, antibiotics, antibody drugs, and other pharmaceutical products are freeze-dried as part of their manufacturing process. Azbil and Azbil Telstar, an azbil Group company based in Spain that makes manufacturing equipment for pharmaceutical factories, have together developed a new technology for systems designed to load and unload vials for the freeze-drying process. Because there is a risk that workers might inhale chemicals, or that dust or bacteria from workers might contaminate products, there is a rapidly increasing need to automate freeze dryer loading and unloading. Not only does the newly developed technology meet this need, but it also has a smaller footprint, is cleaner, and is easier to wash and sterilize than existing systems, thanks to a mechanism based on a magnetic screw, which transmits a driving force without contact.
Background and Needs
Freeze-drying for the preservation of antibiotics, antibody drugs, and other pharmaceutical products
In the pharmaceutical industry, freeze-drying is used to convert liquid antibiotics and antibody drugs (biopharmaceuticals) to a powder, giving them greater stability and helping to maintain their efficacy. At medical institutions, pharmaceuticals thus powdered are dissolved in distilled water and used in injections.
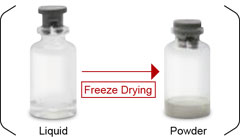
Figure 1. Freeze drying is used to turn liquid into powder.
A freeze dryer is a type of equipment that powders liquid drugs based on freeze-drying principles. For research and development, small freeze dryers are used, but mass-production lines have large freeze dryers that can handle a few thousand or even hundreds of thousands of vials (approximately 16 to 40 mm in diameter) at once.
Azbil Telstar (an azbil Group company headquartered in Catalonia, Spain) provides, a freeze dryer for mass production, with sales mainly to pharmaceutical companies in Europe and North America (Fig. 2).
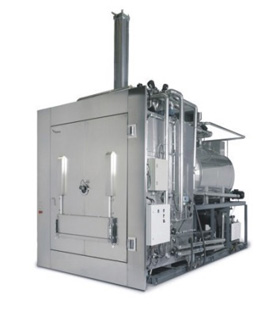
Figure 2. Azbil Telstar freeze dryer for the pharmaceutical industry
Large freeze dryers for pharmaceuticals have problems with loading and unloading.
Vials (sometimes hundreds of thousands at once) must be loaded into the drying chamber of the freeze dryer and unloaded after treatment. To avoid the risk of contamination by various bacteria and other substances as well as the risk of contact with antibiotics and antibody drugs that may have side effects, these processes should be fully automated so that no manual operation is necessary.
To meet these needs, Azbil Telstar provides a loading and unloading system (LUS) for use in combination with a freeze dryer.
Key Innovations
Development of a non-contact drive mechanism based on magnetic screws
In collaboration with Azbil Telstar, Azbil has developed the technology used in the new mechanism in order to improve the LUS and better meet the needs of the pharmaceutical industry.
Figure 3 gives a rough depiction of the mechanism’s structure. Vials are supplied in a row by the conveyor from the side, and a pusher pushes each row-full of vials forward. Once the required number of vials is reached, the slider unit moves the vials onto the green shelf located in the back.
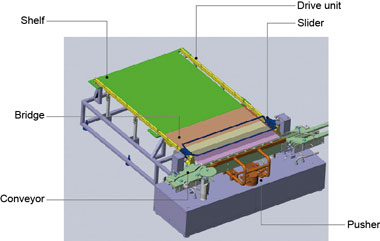
Figure 3. Structural diagram of the newly developed loader-unloader
The previous push-push system used a pusher to push vials all the way, which required a long stroke and necessarily a large footprint. With the new mechanism, the pusher pushes only one row of vials at a time, significantly reducing the footprint.
The most important point in the development of the new system is the drive mechanism, shown in the figure as the drive unit. This mechanism was developed to satisfy the following severe requirements for the inside of the freeze-drying chamber.
(a) Durability even after a -30 to -50 °C pharmaceutical freezing process and sterilization by high-temperature steam (this requirement basically rules out electronic circuits inside the chamber).
(b) To minimize the risk of contaminating pharmaceuticals inside the chamber, no debris (e.g., microscopic shavings generated when metals come into contact with each other) may be produced, and substances that may vaporize (for example, lubricants) cannot be used.
(c) To minimize the risk of contamination, surfaces must be free of concavities where gas could accumulate and must be smooth to allow effective cleaning and sterilization.
To satisfy these requirements, we focused our attention on magnetic screws, which are capable of transmitting driving forces without contact, and we developed a mechanism that enables permanent magnets embedded into the part equivalent to the nut to move along a threaded shaft without contacting the thread (Fig. 4). The magnetic screw indicated as the drive unit in Figure 3 moves the right and left sliders back and forth, and the blue bars connecting the sliders load (push) and unload (pull) the vials.
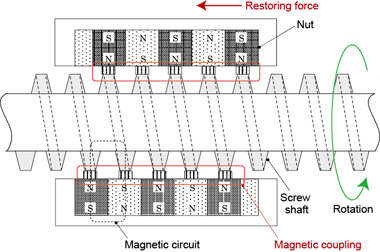
Figure 4. A magnetic screw was developed that causes sliders (which contain permanent magnets) to follow (i.e., to move back and forth with) the screw thread (made of a soft magnetic material) when the threaded shaft is turned. The thread shaft is actually enclosed inside a stainless steel pipe so that the screw thread is not exposed.
Figure 4 shows the screw thread as exposed, but in fact the entire threaded shaft is housed inside a stainless steel pipe, since the uneven surface of the screw would be very difficult to clean. The stainless steel used is a type that does not affect magnetism, so it does not interfere with the drive mechanism.
The threaded shaft is turned by a motor located outside the drying chamber. In order for the chamber to be airtight, we also developed a system by which the threaded shaft can be separated into two parts by removing mechanical links (Fig. 5). Links between the bridge and shelf are removed to close the chamber door.
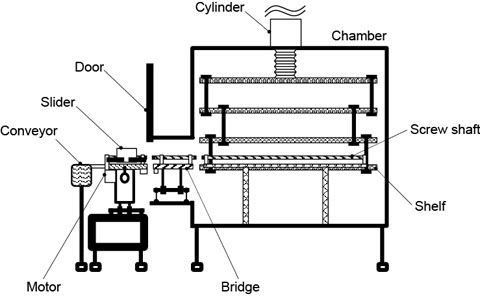
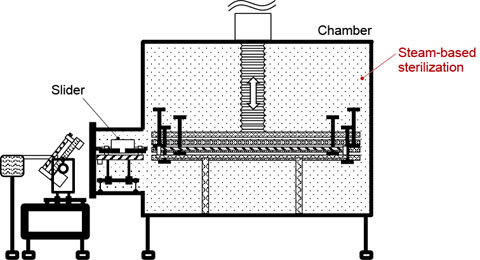
Figure 5. System in operation (above) and being sterilized (below). Sliders are left inside the chamber, which is airtight when the door is closed. This improves sterilization efficiency, leading to higher quality.
Results and Future Prospects
Smaller footprint, cleanliness, and more effective washing and sterilizing
The new loader-unloader is remarkable for achieving the following four improvements.
- Smaller footprint
The conventional push-push system requires a cylinder approximately 2 m long, because it pushes vials all the way into the drying chamber. It therefore requires considerable space in front of it to accommodate the cylinder’s back-and-forth movement. By contrast, the pusher stroke of the new system is short (10–20 cm), which saves space in cleanrooms (Fig. 6).
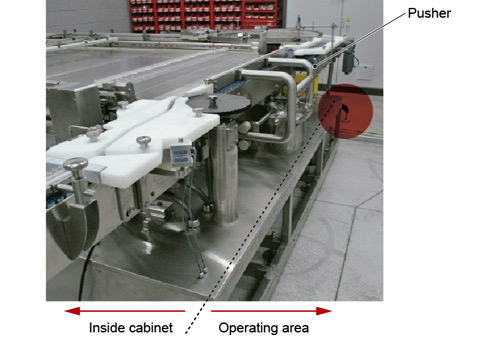
Figure 6. Thanks to the shorter stroke of the pusher, the loader-unloader has a significantly smaller footprint.
- Greater cleanliness
The system uses a magnetic screw that transmits the driving force without contact. This mechanism minimizes mechanical sliding and wear, resulting in significantly reduced debris generation. - Easier to wash
The magnetic screw and sliders are completely enclosed, enabling the system to undergo the cleaning and steam-based sterilization processes inside the chamber following the freeze-drying process. Moreover, since the threaded shaft is inside a stainless steel pipe, there are no projections or depressions, so it is easy to wash. - Easier to sterilize
The magnetic screw and sliders are all designed to stay inside the chamber and can therefore be sterilized in the periodic steam-based sterilization process used for the chamber (Fig. 5). In conventional systems, the carrier bar is located outside the chamber, and therefore it must be sterilized manually.
The prototype loader-unloader received an advance viewing by visitors to a pharmaceutical manufacturing equipment exhibition held in Barcelona, Spain. On that occasion it was highly rated for its small footprint, cleanliness, and ease of washing and sterilizing. With the goal of early commercialization, we are currently working with the development team at Azbil Telstar to conduct endurance tests and lock down the details.
*Handling of products and services described in “azbil techne” may differ by country or region.
azbil Technical Review
A Vial Loading System with Non-Contact Drive Mechanism Using Magnetic Technology
- Azbil Corporation Info
- Corporate Philosophy / Symbol / Policies
- azbil Group Corporate Social Responsibility
- Investor Relations
- Digital Transformation (DX)
- Medium-term Plan
- Research & Development
- Production
- Safety and Dependability of Products and Services
- Procurement
- Exhibitions & Seminars
- Public Relations
- azbil Group
- Certifications
- Global Network