High-Accuracy Flowmeter for Difficult-to-Measure Micro Flows of 30 mL/min and Less
Micro Flow Rate Liquid Flow Meter Model F7M
Azbil has developed a micro-flow meter, model F7M, which accurately measures extremely small volumes of liquid. The strong point of this product is its measurement of flow rates under 30 mL/min with high accuracy (±5 % rdg.). It was designed in response to high demand for this functionality in fields such as industrial instrumentation and semiconductor manufacturing equipment. High accuracy and versatility were achieved by developing a sensor package using MEMS technology, one of Azbil’s specialties, with the application of expertise in flow rate measurement gained by the production of thermal gas flowmeters and electromagnetic flowmeters.
Background and Needs
Accurate measurement of micro flows
In the industrial world, there are a great variety of situations in which a volume of fluid as small as an intravenous drip must be accurately measured. Specific applications include injection of electrolyte solution in the lithium ion battery manufacturing process, application of photoresist solution in semiconductor manufacturing, mixture and dilution of reagents for biochemical examinations and other purposes, spraying of special solutions, and mixing of washing solutions.
Liquid flowmeters using various measurement methods (such as Coriolis, ultrasonic, and thermal technologies) are available on the market. However, each method has known advantages and disadvantages in terms of measurable flow rate, accuracy, temperature characteristics, susceptibility to vibration, size, supported liquids, and so on. There have been almost no products satisfying the market’s need for flow rates on the order of dozens of mL/min [*1], partly because this level of measurement is technically difficult.
[*1]The intravenous drip is often used as an example of a micro flow. With a catheter for adults, 20 drops is about 1 mL. So, if 1 drop falls every second, the flow rate is about 3 mL/min. If fluid falls at the relatively faster pace of 3.3 drops per second, the flow rate will be about 10 mL/min.
To meet customer needs, Azbil commercialized the F7M thermal micro-flow meter (fig. 1), which is capable of measuring flow rates under 30 mL/min with high accuracy, in November 2017.
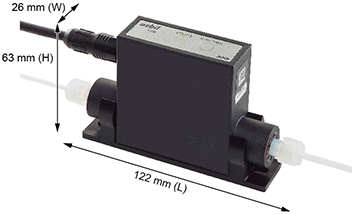
Figure 1. Model F7M micro-flow meter developed by Azbil. The white tubes are the inlet and outlet (left and right respectively) of the flow path. The black cable is for the power and signal lines.
Key Innovations
Flow measurement based on the power required to maintain a temperature difference
As mentioned above, there are many different ways to measure fluid flow rate. The F7M uses thermal measurement, which until now was difficult to apply to liquid flow rate measurement.
The F7M first measures the temperature of the upstream liquid with a temperature sensor. Then, the flowmeter applies power to the heater on the downstream side, raising its surface temperature to create a certain temperature difference with respect to the upstream liquid (fig. 2).
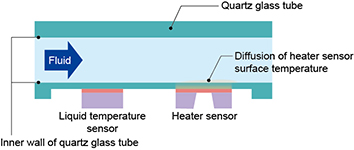
Figure 2. Principle of thermal measurement Azbil developed for the F7M
The faster the flow speed, the more heat is drawn off by the liquid, and therefore the more power (amount of heat) must be applied to the heater sensor to maintain the temperature difference. The contrary is also true: with a slower flow speed, less heat is taken away, which means that less power is required to maintain the temperature difference. In this way the flow speed can be indirectly calculated from the amount of power applied to the heater sensor, and the flow rate can be calculated from the flow speed and the cross-sectional area of the tube.
Although this is an established method for gas flow measurement, application to liquid requires somehow sealing off the liquid temperature sensor and heater sensor to protect and isolate them from contact with the liquid. As a result, only liquids that do not corrode the material of the seal can be used, and it is necessary to ensure that the material of the seal does not contaminate the downstream fluid. For these reasons, this method has rarely been used for liquids.
To address these challenges, Azbil developed the technique of thermally attaching the liquid temperature sensor and the heater sensor to the outside of the quartz glass tube as shown in figure 3. Azbil also developed a sensor structure in which, after measurement through the quartz glass of the upstream liquid temperature and of the downstream diffusion of heat in the liquid, the flow rate is indirectly measured from the power required to maintain the fixed temperature difference.
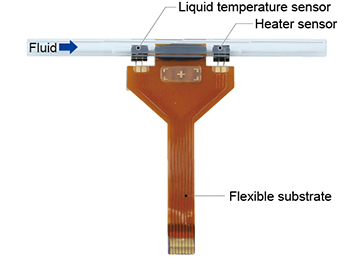
Figure 3. Sensor package incorporated into model F7M
Finding a technique for attaching the sensor chips to the quartz glass tube
A key question in product development was how to attach the flat liquid temperature sensor and heater sensor to the cylindrical quartz glass tube. We examined many different adhesion methods to find one with minimal thermal resistance that would also avoid mechanical stress on the sensor chips. In the end, we devised a method in which part of the circumference of the quartz glass tube is cut to make it flat, and a layer of special adhesive is applied and controlled to a constant thickness (fig. 4).
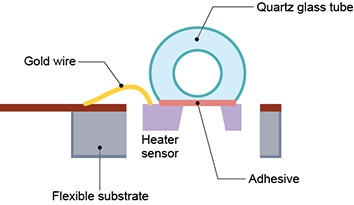
Figure 4. Sensor chip attachment to the quartz glass tube
In addition, we used a flexible substrate for connection with the main substrate on which the microcomputer for control and other components are mounted. The liquid temperature sensor and the heater sensor are connected to the flexible substrate only with bonding wire, so mechanical stress is never applied to either of the sensor chips.
Even when the surface of the heater sensor element generates only a slight amount of heat to maintain the temperature difference, most of the generated heat is transferred to the quartz glass tube. Consequently, the rise in fluid temperature is extremely small and does not affect the physical properties and quality of the liquid.
The liquid temperature sensor and heater sensor were developed using expertise in thermal fluid measurement accumulated by the development of micro-flow sensors for gas, and expertise in MEMS technology, which is one of Azbil’s strong suits. These sensors have a thin-film diaphragm structure and require very little power to operate (fig. 5).
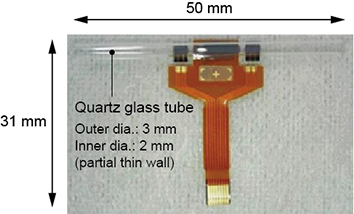
Figure 5. Development of a compact sensor package leveraging MEMS technology
Results and Future Prospects
Expansion of the flow rate range and other improvements
Partly because there were no easy-to-use, high-accuracy micro-flow meters that support flow rates under 30 mL/min on the market, the model F7M has enjoyed a great reputation in the industrial instrumentation and semiconductor manufacturing equipment fields since its launch in November 2017.
In the future, we plan to expand the lineup of flow rate ranges using the same measurement method. We will also attempt to add variations to support hydrofluoric acid, strong phosphoric acid, and other types of liquid that corrode quartz glass.
Azbil is proud that the model F7M is leading the world as a micro-flow meter for flow rates around 30 mL/min, and we will continue our efforts to develop solutions and products needed by customers.
*Handling of products and services described in “azbil techne” may differ by country or region.
Related Information
- Azbil Corporation Info
- Corporate Philosophy / Symbol / Policies
- azbil Group Corporate Social Responsibility
- Investor Relations
- Digital Transformation (DX)
- Medium-term Plan
- Research & Development
- Production
- Safety and Dependability of Products and Services
- Procurement
- Exhibitions & Seminars
- Public Relations
- azbil Group
- Certifications
- Global Network