The azbil Group’s Largest Valve Maintenance Center Established in Thailand
Providing new DX-powered value and creating solutions for ASEAN and for countries and regions beyond
Azbil (Thailand) Co., Ltd., which is the azbil Group’s Thai subsidiary, has been providing maintenance services for valves installed at customers’ plants in Rayong Province, located in Thailand’s Eastern Economic Corridor, for more than 15 years. When the company’s aging facility was renovated, it was also reborn as the Solution and Technology Center, which provides smart security and digital transformation (DX) to ASEAN customers. As the largest valve maintenance center in the azbil Group, it provides solutions for reliable and safe plant operation.
- Advanced technology and the azbil Group’s largest valve maintenance center
- Providing global customers with technology cultivated in Japan
- With an eye to the future, becoming a major technology and HR base
Advanced technology and the azbil Group’s largest valve maintenance center
The azbil Group’s aim is to make contributions leading “in series” to the achievement of a sustainable society and to its own growth by solving the new problems that society faces. To strengthen company management and achieve medium-to-long-term growth, the azbil Group is laying the foundations for global business. China, Thailand, and Japan have been set as the three main bases for production, and work is underway to improve production efficiency, conduct business continuity planning (BCP*1), etc. Also, in order to provide services*2 for overseas customers’ buildings, plants, and factories that are equal in quality to the services provided in Japan, the azbil Group is expanding and strengthening its service system and training its personnel.
Azbil (Thailand) was established in 1995 as the Thai subsidiary of Azbil Corporation. With its head office in Bangkok and branch offices in Rayong and Chonburi Provinces, the company is located in the Eastern Economic Corridor,*3 a special economic zone created by the Thai government for the development of advanced industry. Rayong Province faces the sea, and its industrial area is home to many petrochemical complexes where control valves of various types control a variety of chemicals and other fluids used in important production processes. Since it is no easy task to replace a control valve when it fails, efforts are made to prevent a valve failure and maintain stable plant operation through regular disassembly, inspection, and repair. Azbil (Thailand) has the largest valve maintenance center among the azbil Group’s six ASEAN subsidiaries (which are in Vietnam, Thailand, Philippines, Malaysia, Singapore, and Indonesia). For more than 15 years the center has provided maintenance services by receiving valves (regardless of their manufacturer), taking them apart, and inspecting them. When the opportunity to renovate the old facility in the southern part of Rayong Province came along, the center took advantage of the trend in recent years toward DX*4 and was reborn in December 2019 as the more advanced Solution and Technology Center.
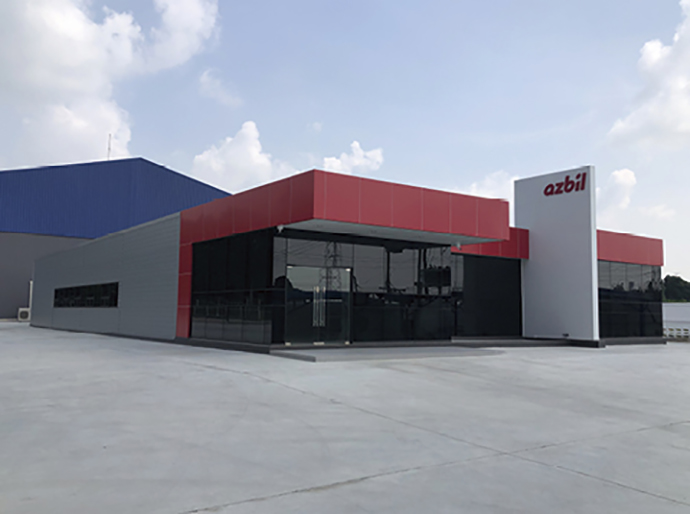
The Solution and Technology Center in Rayong Province
Providing global customers with technology cultivated in Japan
Azbil has been developing products and services to enhance productivity and quality in the area of smart industrial safety, which uses technological advances such as the Internet of Things (IoT), big data, and artificial intelligence (AI). Proactive proposals are being made to provide this technology to ASEAN customers, with the Solution and Technology Center as a major base. Conventional plants need a high operating ratio and on-schedule production to earn a profit, so steady and reliable operation is required. However, unlike other plant equipment, when a valve is affected by internal abrasion or corrosion, the problem cannot be seen from the outside. To keep availability (operating ratio) high, it is important that many valves operate reliably, so planned systematic maintenance has long been applied. The Solution and Technology Center can service about 10,000 valves per year, and in addition to regular maintenance, it also provides a service to monitor the condition of valves using Azbil’s control valve maintenance support system. With Azbil’s control valve maintenance support system, data on valve operation at the production plant is collected and trends in valve diagnostics are monitored online, making it possible to detect valve problems at an early stage, without stopping the plant. In this way problems like a sudden failure that shuts down the plant can be prevented. In the Solution and Technology Center, data collected by Azbil’s control valve maintenance support system is analyzed and visualized by engineers, and the results of diagnosis are provided to customers quickly. Using these results, plant personnel can select only the necessary valves for disassembly and inspection, which helps to reduce maintenance costs, and personnel can optimize the plant maintenance plan.
The azbil Group is also striving to develop its human resources, and is passing on valve maintenance technology created in Japan to its ASEAN engineers. Engineers from Japan who are skilled in valve maintenance stay at the center and provide on-the-job training for local engineers, as well as online training and consultation for ASEAN subsidiaries. Also, when another subsidiary needs help with a customer’s valve, a system has been established in which an engineer is dispatched from Thailand as part of the Solution and Technology Center’s role as a valve maintenance hub for ASEAN subsidiaries.
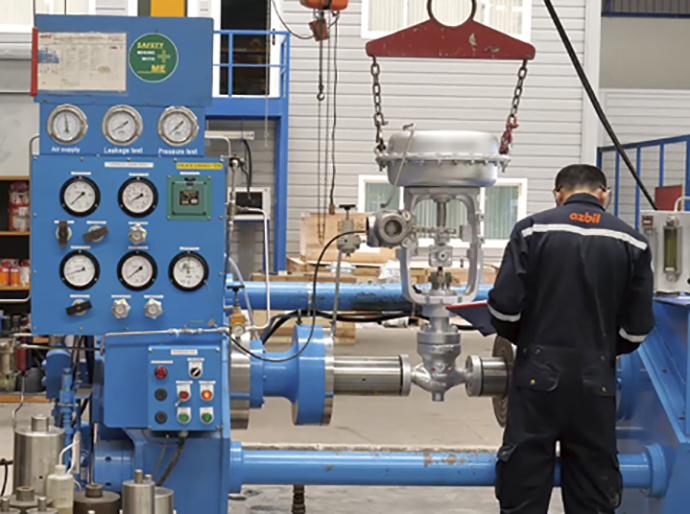
After the assembly, inspection, and repair of valves, a pressure-resistance test and airtight test are done to ensure quality.
With an eye to the future, becoming a major technology and HR base
At the Solution and Technology Center, besides taking a valve maintenance tour or obtaining advice on a valve based on analysis of data by Azbil’s control valve maintenance support system, visitors to the center’s showroom can experience the latest technology, including a DCS*5 and instrumentation devices that are used in plants, and can handle actual products. Additionally, there is an online collaboration environment where Azbil can demonstrate the strengths of its various bases beyond the Thai business, allowing the exchange of opinions across national and regional boundaries. It is possible to collaborate online with the Fujisawa Technology Center and the Shonan Factory in Japan (the two facilities constitute Azbil’s “mother factory”), and with the Strategic Planning & Development Office for Southeast Asia in Singapore, which is an Azbil organization with the mission of comprehensive expansion and growth throughout Southeast Asia. In this way Thai customers can see the Japanese production sites and showrooms and get to know the background of Azbil (Thailand)’s technological capabilities. Efforts are underway to make customers in various countries, including Japan, aware of the activities of the azbil Group in ASEAN countries such as Thailand and Singapore.
Since 2016, the azbil Group has been accepting interns every year from three famous Thai universities, Chulalongkorn University, Kasetsart University, and King Mongkut’s Institute of Technology. With Chulalongkorn University, in particular, Azbil collaborates in technical forums, joint research, and seminars. One intern from there has joined the azbil Group and is a valuable employee.
By becoming a major base for technology in ASEAN, the Solution and Technology Center, along with other subsidiaries, fulfills its role as a “long-term partner for customers and society” by developing solutions based on Azbil’s technology and products, and helping to enhance the value and boost the development of Azbil’s customers.
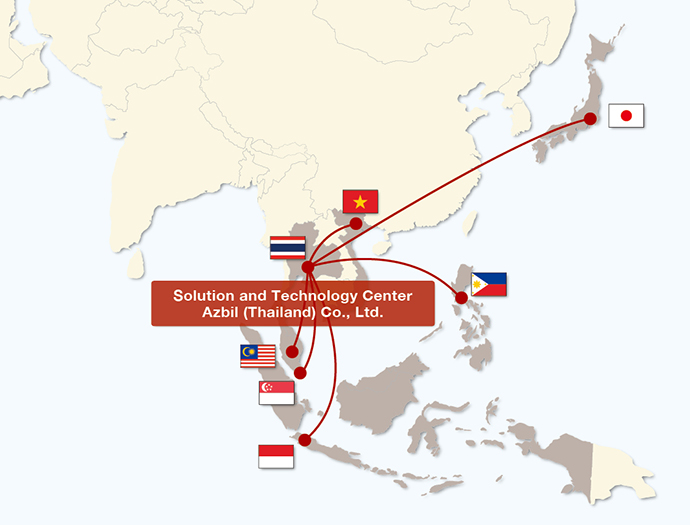
The Solution and Technology Center continues to strengthen the cooperation among the six local subsidiaries in the ASEAN region and Japan, so that information can be shared and opinions can be exchanged efficiently.
*1 Business continuity planning (BCP)
Planning performed by a company to minimize damage and continue or restore business activity in the event of a disaster.
*2 Services
Service engineers familiar with the equipment and systems in buildings, plants, factories, etc., provide optimal operation, perform periodic inspections, and handle maintenance. In addition to responding to urgent problems quickly, they meet various customer needs, such as collecting data at remote locations, providing remote maintenance, analyzing collected data, and proposing solutions.
*3 Eastern Economic Corridor (EEC)
A special economic zone designated by the Thai government in order to enhance industry, create high added value, and bring about the long-term “Thailand 4.0” vision presented in 2015 by the Thai government. The EEC focuses on 10 priority industries, including next-generation automobiles and robotics, and works to attract and develop advanced industries.
*4 Digital transformation (DX)
Efforts to change people’s lives for the better with digital technology
*5 Distributed control system (DCS)
A dedicated system for monitoring and controlling the manufacturing processes and production equipment of plants and factories. To achieve an even distribution of load, the DCS manages the functions of each device over a network, resulting in safety and excellent maintainability.
This article was published on July 1, 2021.