Smart Industrial Safety
An approach that ensures safety and reliability for plant operation or the working of infrastructure through the ability to detect warning signs and quickly respond to emergencies by accurately understanding the status of facilities and services based on the scientific foundation of collected data, including images, temperature, pressure, and flow rate.
- Resolving problems with plant operations using digital technology
- Finely detailed sensing of operating conditions with high-performance sensors
- Government assistance and relaxation of industrial safety regulations
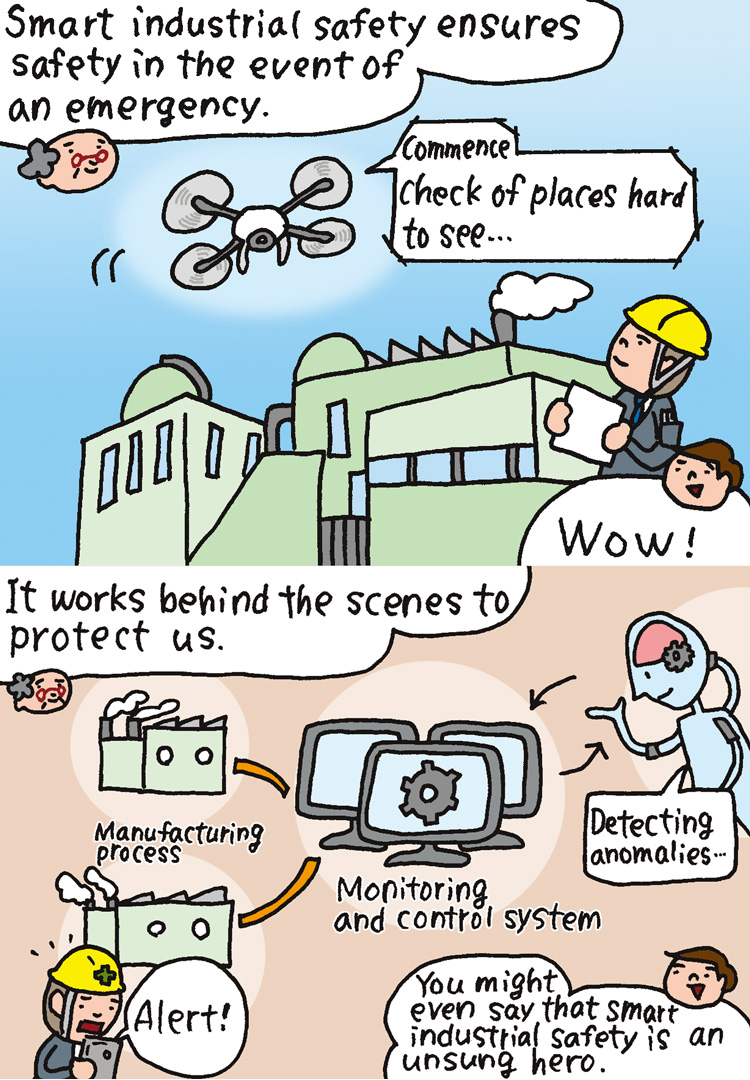
Resolving problems with plant operations using digital technology
In recent years, digital technology like the IoT and artificial intelligence (AI) has been rapidly advancing, and people’s lives and ways of working have also been changing significantly. In the world of manufacturing, collecting information on manufacturing processes via a network and using AI to learn from it and make decisions is one of the trends of Industry 4.0.*1 Also, there are expedited efforts to realize smart factories and plants by making production automated, optimized, and autonomous.
Such smart production sites attract attention because beyond merely improving production efficiency they also help to solve problems faced by the manufacturing industry. For example, at petroleum and chemical plants in Japan, there is growing concern about unexpected problems due to the aging of equipment, and even longterm workers may not have experience with these problems. Since skilled workers retire and hiring personnel is becoming difficult due to the declining working population, the transfer of skills and know-how related to plant operation is an urgent issue in the field.
One approach to problems like these is smart industrial safety, which uses digital technology like the IoT and AI to understand and constantly monitor the status of facilities and equipment, achieves plant operation with high labor productivity, and improves the safety and reliability of plant operation.
Finely detailed sensing of operating conditions with high-performance sensors
A variety of projects related to smart industrial safety are being devised and implemented today. One example is a system that visualizes the condition of important equipment such as the control valves that undergird plant operations. Important facilities and equipment are equipped with high-performance sensors, and data on detailed operating conditions is collected. By analyzing this data, problems or warning signs of problems that cannot be found by normal monitoring and inspection can be caught. Another type of system that is attracting attention helps to keep operation safe and reliable by exposing malfunctions and irregularities from the perspective of overall plant operation rather than individual equipment. This type of system uses data on individual production processes and facilities that is collected by a DCS*2 or other monitoring and control system, and uses the data to detect signs of trouble and prepare for abnormalities expected in the future.
Another example is the use of drones, which have recently been applied in a wide range of areas and are expected to be an important tool for smart industrial safety. For example, drones are used to photograph high places that cannot be monitored by people or fixed cameras in order to provide wide-area monitoring for facilities.
Government assistance and relaxation of industrial safety regulations
In order to advance smart industrial safety, the Japanese government, for example, mainly under the leadership of the Ministry of Economy, Trade and Industry (METI), is also taking various steps, including the revision of industry safety regulations. In the case of drones, one difficulty with their use at plants is that the crash of a drone may result in equipment damage, fire, or explosion, since there are areas where explosive atmospheres may be generated or where the use of fire is restricted. However, the government recognizes that drones are highly useful and has created guidelines that cover specific operating methods, safety measures, and flight planning, so that the use of drones is now partly allowed. Additionally, the government has carried out a comprehensive inspection of relevant safety regulations, bearing in mind the use of new technology such as AI, sensing, and robots in the area of industrial safety. Based on the results, the government is continuing to ease regulations.
One example is the Specified Authorized Business System, which METI started operating in April 2017. Originally, the High Pressure Gas Safety Act defined authorized business systems, giving incentives (that allow self-inspection and continuous operation) to businesses which voluntarily develop safety organizations, etc. The Specified Authorized Business System certifies high-pressure gas companies that use an IoT, AI, etc., to implement even higher levels of self-maintenance for safety as “specified authorized business establishments.” This system simplifies regulations so that the authorized companies by themselves can set a period for continuous operation within a range of eight years.
As society pursues carbon-neutrality, more equipment that uses renewable energy is introduced and new production methods will be required in industry. At such a time, new problems that we never could have expected may arise. To overcome them, smart industrial safety that takes appropriate measures based on data and scientific evidence will be increasingly important.
*1 Industry 4.0
Also called the Fourth Industrial Revolution, this technological concept aims at automation, digitization, and computerization of the manufacturing industry. The IoT and cloud computing are part of Industry 4.0.
*2 DCS
Distributed control system. A dedicated system for monitoring and controlling the manufacturing processes and production equipment of plants and factories. To achieve an even distribution of load, the DCS manages the functions of each device over a network, resulting in safety and excellent maintainability.