マザー工場での生産工程の革新
キーワード:マザー工場、センサパッケージング、ヒューマンエラー、AI、混流生産
新たな製品を生み出すための先進的な生産技術を獲得するとともに、継続的な製造コスト低減と製造品質の向上を図っていくことが、azbilグループの生産をリードするマザー工場としての役割の1つである。長年にわたり構築されたセンサパッケージング技術を活用した高度な生産工程として、AI画像処理技術や力制御技術を用いた部品の精密実装、微細組立の事例を述べる。またazbilグループの強みである顧客の様々なニーズに対応する多品種変量生産/カスタマイズ生産を支える混流生産方式をグローバル生産に展開するための生産システム構築、ヒューマンエラーの排除、および新たな混流生産ライン構築への取組みについて、ここに報告する。
1.はじめに
アズビル株式会社ではこれまで伊勢原工場(神奈川県伊勢原市)、藤沢テクノセンター(神奈川県藤沢市)に分散していた生産機能を、湘南工場(神奈川県寒川町)をazbilグループのマザー工場と位置付け集約し、先進的な生産技術による生産の実証の場として生産革新に取り組んでいる。
現在azbilグループのマザー工場では大きく分けて2つの機能強化を進めている。まず1つには昨今の大きな技術変革の潮流に対応した新たな製品を生み出すための生産技術の獲得による生産強化である。他社が容易にまねできない、追随困難な生産工程による製品を開発することがアズビルならではの製品仕様となり、製品価値を高め顧客満足を得ることができると考える。もう1つはazbilグループの強みである顧客の様々なニーズに対応できる多品種変量生産/カスタマイズ生産体制を維持したうえで、継続的な製造コスト低減と製造品質の向上を図り、グローバル生産に展開していくことである。
1つ目の課題に対しては、長年にわたる各種センサを搭載した製品開発で構築されたセンサパッケージング技術に、新たにAI画像処理技術や微細部品の組立に活用できる力制御技術を加えることで、生産工程の高度化を進めている。
2つ目の課題に対しては、多品種変量生産/カスタマイズ生産を支える混流生産方式に生産情報の一元管理や加工条件の自動設定などICT側面での強化や生産作業者個人の経験や技能に依存した生産工程からの脱却、またヒューマンエラーの排除を目的とした生産工程の自動化に取り組む超混流生産ラインの構築を進めている。
本稿では2つの課題に対する技術的なアプローチによる解決手段を述べ、具体的に得られた結果をその成果として報告する。
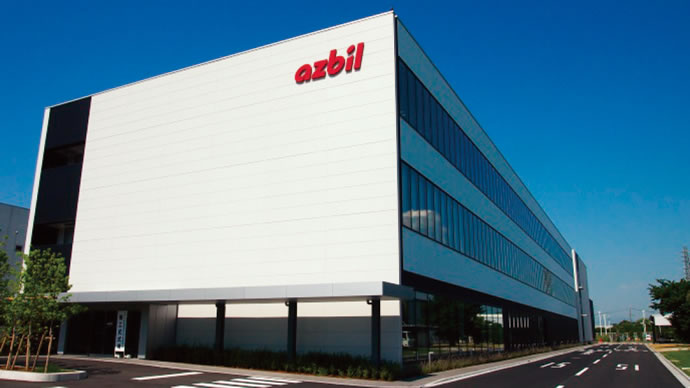
図1 アズビル㈱湘南工場に新設された生産棟
2.生産工程を取り巻く課題
2.1 生産技術による競争優位製品の開発
昨今のIoT、ICTニーズの高まりを支えている計測機器製品を開発する上で、最も重要な技術の1つとしてセンサパッケージング技術がある。センサパッケージング技術とは物理的、電気的にセンサやマイクロデバイスを製品の電気回路に接続するためのモジュールを生産する技術と位置づけることができる。このモジュールを安定的に生産するためには、脆性材料の切削や接合・接着、また微細な金属材料加工や精密組立といった要素技術の蓄積と、それらを生産工程として実現する機械装置を開発できる生産技術力が求められる。このセンサパッケージング技術を高度化することで、計測性能、製品品質を高め、他社が容易に追従できない製品を獲得することが可能となる。高度なセンサパッケージング技術に基づく生産工程を保有することがazbilグループのマザー工場に求められる1つ目の課題であり、使命となる。
2.2 多品種変量生産/カスタマイズ生産のグローバル生産対応に向けて
顧客の様々なニーズに対応するための多品種変量生産/カスタマイズ生産はazbilグループの強みである一方、これらに対応するために生産工程設計や設備設計は個別最適化が進み、工場全体で見た稼働効率やスペース効率が低下する傾向が顕在化していた。その解決策の1つとして考えられるのが従来から複数の製品や機種を共通の生産工程・設備で流す混流生産ラインの適用拡大である。
昨今では顧客ニーズが多様化しているため多品種変量生産がさらに進む状況にある。生産工程では機種別に生産数量の平準化など生産計画で運用面での効率化を図るものの、頻繁な生産機種の切り替えによる部品変更、組立手順変更、設備の段替え(条件・設定変更)が余儀なくされていた。またこれに顧客ごとのカスタマイズ対応も加わると特別仕立ての部品・組立方法・設備仕様が追加されることになるため、混流生産ラインはさらに複雑化し、生産現場の負担が増大していた。
また、混流生産は国内の生産において、生産作業者の高い習熟度、多能工化や現場管理者のスキルによって、複雑な生産工程にも柔軟な対応を行ってきた。高い現場スキルによって支えられた生産体制であったと言える。混流生産ラインの適用拡大を進めるには、(1)デジタル化された生産情報を生産現場が活用できる状態で蓄積するデータベースを含む工程管理システムの構築、(2)工程管理システムのデータベース情報を使って作業者にタイムリーに正確な作業指示を与えることでヒューマンエラーを排除し、製造品質を安定させることのできる装置の導入、(3)人と機械、システムが協調した新たな混流生産ラインの構築(1)、が必要となる。混流生産をグローバルでも展開するために、生産設備や工程管理システムの標準化を行い、現場で働く人への負担や依存度がさらに軽減された、ストレスのない超混流生産ラインを構築することが、azbilグループのマザー工場に求められる2つ目の使命となる。(2)
3.生産工程の革新への取組み
3.1 高度センサパッケージング技術による生産
3.1.1 部品の精密実装
小型化、高精度化を求められるセンサパッケージングにおいて、微細部品の精密位置決め、組立技術は、不可欠な要素技術である。例えば、汎用アンプ内蔵光電センサ 形HP7では、光を集光するレンズに対してLEDの搭載相対位置精度が光学性能を左右するため、数十μmオーダーの位置精度でプリント基板へはんだ付けを行う必要がある。従来技術としては、LEDをカメラで撮像しモニタに拡大表示させ、熟練作業者が手作業で位置合わせを行い、治具で固定してはんだ付けを行っていた。近年では、画像処理による精密位置決めとはんだコテを使用した自動はんだ付け装置の導入により工程の自動化を進めてきた。しかしながらはんだ付けを行うはんだコテの酸化やコテ先のメッキの消耗などによる経時変化が発生するため、はんだ流れを制御することは困難であり、はんだ付けの出来栄えに不安定さが見られた。加えてコテはんだ付け方式では供給するはんだ量も多くなり、はんだに含まれるフラックスがプロセス中に多く飛散してしまう。これによってLEDを把持する自動はんだ付け装置のツールが汚染されるために、精密な位置決めが阻害され安定生産には至っていなかった。
これらコテはんだ付け方式の課題を解決するために、非接触式のレーザー加熱によるはんだ付け方式を採用した。これにより酸化や消耗などの経時変化に影響されづらい安定したはんだ付け装置を生産導入することができた。非接触式のレーザー加熱では、はんだコテ側に残るはんだがなくなるため、供給するはんだ量、すなわち1回のプロセスで溶融させるはんだ量を少なくすることができるため、フラックス飛散によるツールの汚染を低減することができた。しかしながらツール表面がフラックスで汚染されると、その粘性によってLEDがツールに付着する現象を完全に防止するまでには至らず、位置決め後のLED解放時に突発的な位置ずれが発生する。また短いサイクルでの連続実装によってツール先端の温度が上昇するためツールの伸びが発生し、連続的に変化する位置ずれも発生していることから長期的な安定性を実現するまでには至らなかった。そこで実装されたLEDの位置ずれ量を計測し、LEDの位置決めの狙い値にフィードバックすることで、実装位置を補正する制御方式を導入した。
図2に補正制御の有無によるLEDの位置ずれ量の比較を行った結果を示す。補正制御を行っていない従来の実装方法ではLEDの実装位置は狙い値に対して横方向も縦方向も生産台数が増えるとともに位置ずれ量の変化が発生していることが分かる。これに対して補正制御を行った今回の実装方法では、狙い値に対して一定の位置ずれ量で安定していることが分かる。
今回導入した制御ではLEDの位置ずれ量に統計的処理を行い、経時的に発生している位置ずれとLEDのツールへの付着など突発的に発生する位置ずれを分離し、経時的な変化のみを補正している。また突発的な位置ずれの発生頻度からツールのクリーニング時期を判断し、作業者に対してアラートを上げることにした。これにより高精度な位置決めでのLEDの実装を実現している。
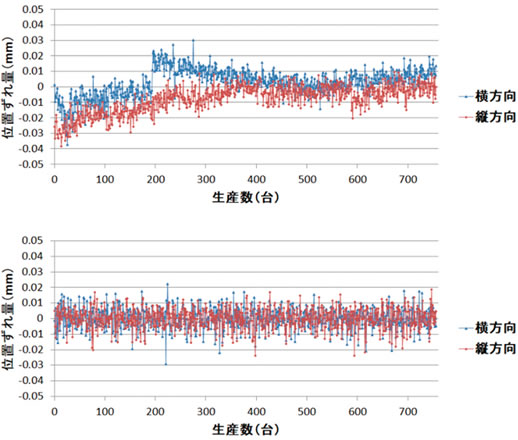
図2 補正制御の有無によるLEDの位置ずれ量の比較
(上:補正制御なし、下:補正制御あり)
3.1.2 はんだ付けの出来栄え検査の自動化
次にはんだ付けの出来栄え検査工程について説明する。従来は熟練作業者がすべて目視により検査を行っていたが、AIを活用した画像検査を適用することによりグローバル生産に展開できる自動検査へと移行する生産改革を進めている。
一般的なAI学習であれば、良品・不良品画像の両者を教師データとして学習させるが、生産現場では多量の不良品画像を取得することは困難であること、また未知の不良が発生した場合、不良と良品のどちらに近いかという判断を行ってしまえば、生産工程では許されない不良品を良品として判定する可能性が生じる(3)。これを防止するために良品画像のみを教師データとして機械学習を行い、不良品を次工程に流出させることのない検査アルゴリズムによる検査プログラムを作成した。
しかしこの方法の最大の難点は不良品の過剰判定による過検知である。これまで行っていたコテを使用した自動はんだ付け装置ではコテの表面状態、温度の変化などの要因によってはんだの出来栄え形状が多岐にわたり、良否判定そのものが難しかった。実際のはんだ不良率の数倍から数十倍の過検知が発生しており、自動検査後に不良判定された製品を再度目視検査するというムダな作業が必要であった。今回導入したレーザー加熱方式では要因変化とはんだ出来栄え形状がAI画像検査技術で扱いやすい範囲に収まり、自動検査が可能になったと考えられる。
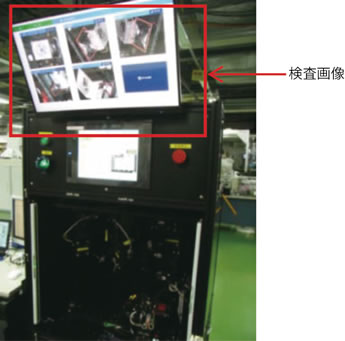
図3 画像検査装置
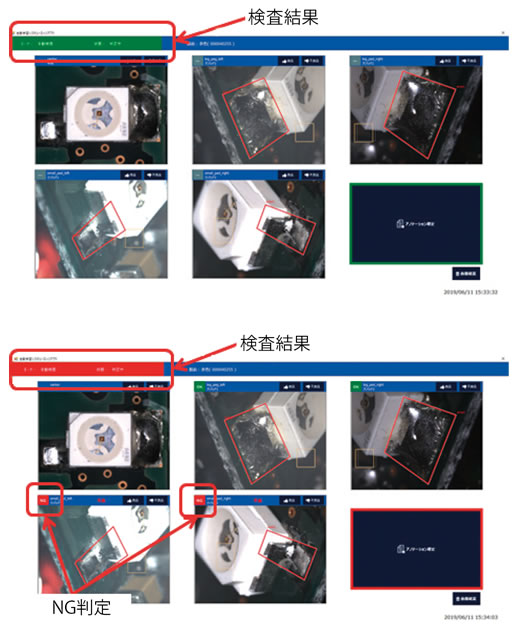
図4 画像検査結果(上:OK判定、下:NG判定)
3.1.3 微細組立
センサパッケージングでは、脆性材料からなるセンサチップを接着、接合などの組立を行うため、力制御ができる部品の搬送技術も重要な要素技術である。スマート・バルブ・ポジショナ200シリーズ、300シリーズ、700シリーズに搭載される磁気抵抗センサのセンサパッケージでは、センサホルダと呼ばれる樹脂の部品に対し、センサチップを接着するダイボンディング構造となっており、磁界を印加するマグネットとセンサチップの相対位置精度が計測性能を決定する。そのためセンサチップの搭載高さ、回転等、高精度な位置決めが要求される。また脆性材料であるセンサチップの搬送時の破損を防止するために、ピックアップ時やセンサホルダへの搭載時の力制御も不可欠である。センサの微細組立は、位置制御と力制御を同時に行うことができるアズビルの独自技術であるアクティブコンプライアンス™制御を用いることで、実現している。(4)
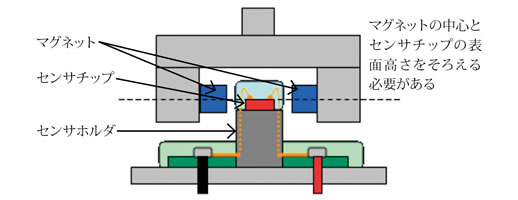
図5 磁気抵抗センサイメージ図
具体的な生産工程の説明を行う。センサチップは、チップトレーに入った状態でダイボンディング装置に供給され、はじめに画像処理により、センサチップの座標位置、回転角度を計測したあと、吸着式ノズルによってピックアップされ位置補正を行う。その後あらかじめ精密ディスペンサによりダイボンド剤を塗布したセンサホルダに固着させている。センサチップのピックアップ時には、センサチップを破損しないように弱い力でセンサチップに近づき、センサチップをピックアップする吸着式ノズルの移動量の変化を見ることでセンサチップに接触したことを検知して、把持を行っている。
一方、センサホルダへの接着時には、接着剤の粘度に応じて、センサチップを破損しない力で所定の搭載高さまで押し込むことで、位置精度の安定したダイボンディング工程を実現している。このように力制御を応用したアクティブコンプライアンス制御の適用により、回転角度だけではなく高さ方向の制御が安定して接着できるようになったため、後工程での実装検査も削除することができた。
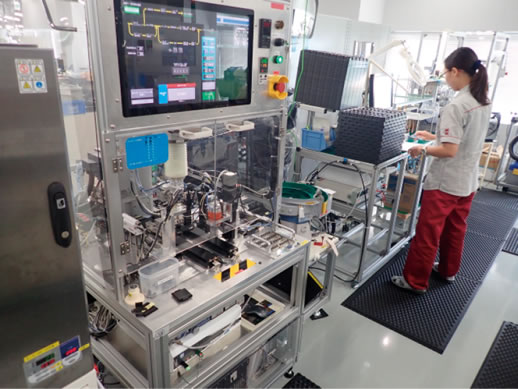
図6 磁気抵抗センサダイボンディング装置
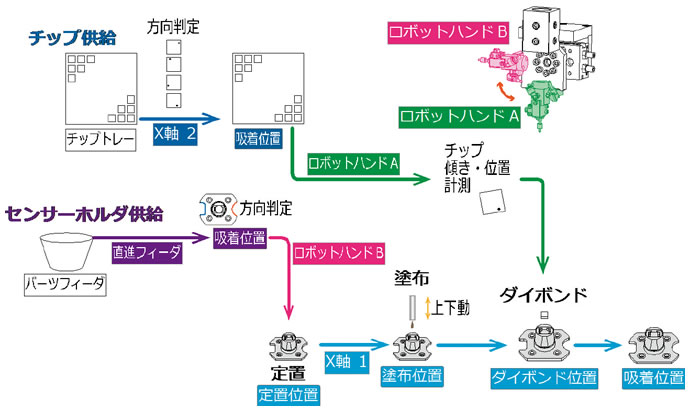
図7 磁気抵抗センサダイボンディング工程
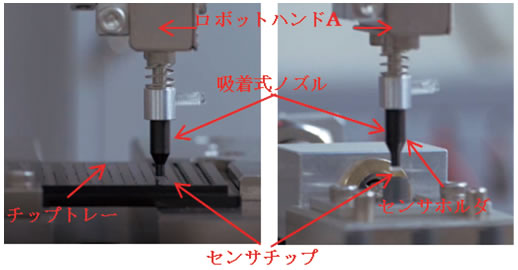
図8 センサチップピックアップ写真(左)、センサチップダイボンディング写真(右)
3.2 超混流生産ラインの構築のための具体策
3.2.1 工程管理システムの構築
生産現場へのInput情報、現場からのOutput情報をデジタル化し、管理、活用するためには、全社の基幹システムと生産現場をつなぐMES(Manufacturing Execution System)が必要となる。市場には各種のパッケージソフトウェアが用意されているが、導入による費用対効果やアズビル生産形態とパッケージソフトウェアの親和性の検証など選定は容易ではない。また検討開始時点では超混流生産ラインのシステム要件定義も困難であることから、azbilグループの生産特性に適したMESの機能の一部を果たす工程管理システムを開発することからスタートした。
今回開発した工程管理システムは全社の基幹システムとMicrosoft® SQL Serverと生産設備をネットワークでつないだシステム構成となっている。製造指示情報(シリアル番号・機種識別情報)、生産進捗・来歴データ、M-BOM(製造部品表)、機種別設定情報など生産現場が活用するための各種情報をデータベースに蓄積することができる。生産される製品の個体認識によって工程管理システムから使用する生産設備を特定し、生産設備の加工条件など必要な情報を自動的に取り出すことができる。また生産工程の検査データや部品情報など来歴データのOutput情報も工程管理システムのデータベースに製品の製造シリアル番号をキーとして保管することができる。例えばプラント工場などで気体、液体、蒸気の流量、圧力、液位などを測定できる差圧・圧力発信器Advanced Transmitter Model GTX□□□などでは年間に7,800種類を超える形式を生産しており個々の製品が適切な工程で生産されたことを保証する生産トレース情報は重要である。これを今回導入した工程管理システムではリアルタイムに取り出すことができるようになった。
3.2.2 多品種、カスタマイズ生産におけるヒューマンエラーの排除
多品種、カスタマイズ生産において作業者の習熟度や多能工化状態など人の管理スキルに依存する領域が多く存在することでヒューマンエラーのリスクは増大する。多種類の部品ピッキング、作業指示、高頻度の設備段替えの際に人の関与を減らすことがヒューマンエラーリスクを低減し、高品質・高効率な生産ラインを維持することができる。今回導入した工程管理システムによって、生産設備が製品シリアル番号を認識し、データベースにアクセスすることで機種ごとのピッキング情報や設備の条件設定情報を取り出すことができる。部品ピッキング支援装置や製品に製品形番や機種ごとに固有の情報を印字するマーキング装置への自動設定などに適用することで、生産作業者のスキルに依存することなく、差圧・圧力発信器 Advanced Transmitter Model GTX□□□のような多品種製品の組立工程においてもヒューマンエラーを排除した生産工程の確立が可能となった。

図9 工程管理システム概要
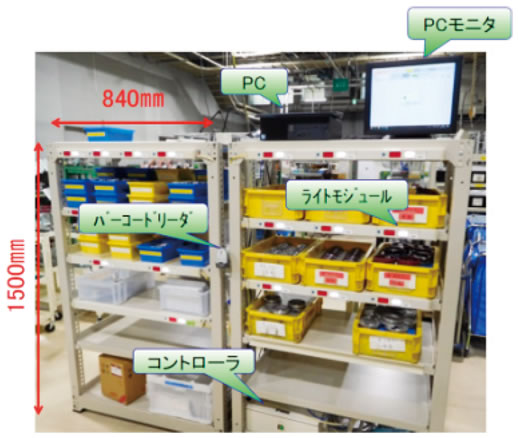
図10 ピッキング支援装置
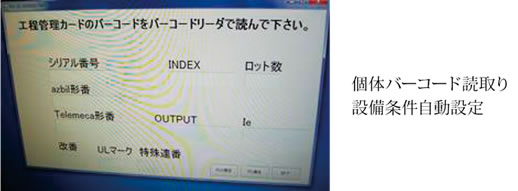
図11 マーキング条件設定
3.2.3 新たな混流生産ラインの構築
工程管理システム、ヒューマンエラー排除の仕組みの構築をベースにして、混流生産ラインの再構築を行った。共通機能工程を多く持つ生産ライン(製品シリーズ)を対象に定め、混流による効率化が可能な工程を抽出した。実際には、気体流量計の生産ラインを対象にして、以下の工程に対して混流化を図った。
はんだ付け工程
耐圧リーク検査工程
電気機能検査工程
流量調整、校正工程
同一製品シリーズといっても各製品の開発時期が異なるため同じ電気基板のはんだ付け工程にしても、はんだパットの形状やレイアウトはまちまちであった。そこで1台の自動はんだ付け装置で対応できるようにするためには、電気基板の共通化、統一化も並行して行う必要があった。同様に混流化工程の部品の共通化を行い、結果として部品点数を10%削減することができた。
生産エリアでは従来の製品シリーズごとに専用ライン、専用設備を導入する場合に比べ、スペース効率、設備稼働効率を向上させることが実証できた。
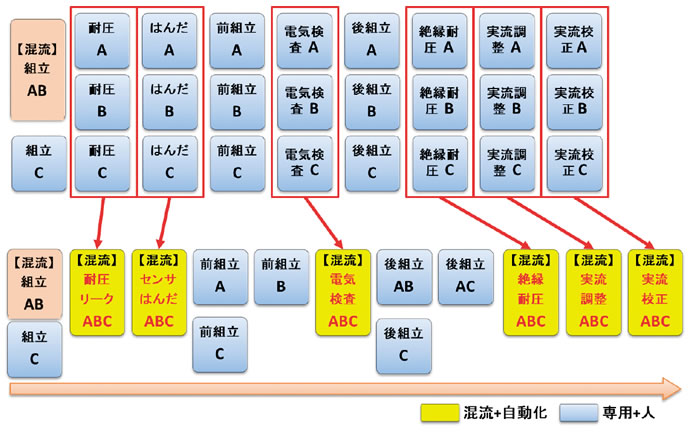
図12 混流生産概要
4.成果
4.1 センサパッケージング技術による製品の競争力強化
センサパッケージングではセンサチップの取扱い等で微妙な力加減が要求されるため、組立工程での自動化が限定的であったが、アクティブコンプライアンス制御の適用により工程の自動化を加速することができた。アクティブコンプライアンス制御と非接触式のレーザーはんだ工法,精密位置決め技術、位置制御を組み合わせることにより,より小型のセンサパッケージングの生産が可能となった。
また、AI画像検査の導入により、後工程への不良品の流出の排除を実現し、そのトレードオフとなる過剰判定率(過検知率)も従来の画像検査の1/10以下と精度が高い検査となった。現在AI画像検査は、はんだ検査に加え、官能検査の領域となる他の検査工程への展開を進めている。
4.2 超混流生産に向けて
(1) azbilグループの生産特性に適した工程管理システムの構築
(2) 工程管理システムを活用し、ヒューマンエラーを排除する装置導入
(3) 新たな混流生産ラインの構築
これらの取組みによって、小規模で投資効率が高く、人への依存が低い混流生産ラインとなった。
今回の気体流量計の生産ラインでは3シリーズの製品に対して、混流化を行い、専用ラインを設置する場合に比べ、専有面積はおよそ50%で構築可能となった。設備タクトの長い設備稼働率は17%向上した。自動化や工程管理システムを活用したガイダンス装置により、製造不良削減に一定の成果を得ている。混流生産をきっかけに、開発部門と協業した製品の共通化設計に貢献した。
今後は生産工程の情報の把握のリアルタイム性を上げてさらに生産性や品質の向上を図っていく。加えて、製品設計との情報連携により、生産設備設計・構築の短縮化へも繋げていくことも必要と考える。
5.おわりに
azbilグループのマザー工場でのセンサパッケージング技術による生産工程の高度化および、多品種変量生産/カスタマイズ生産をグローバル生産展開するための“超”混流生産への取組みについて報告を行った。
センサパッケージング技術ではAIを活用した画像処理技術などを積極的に取り入れ、アズビルらしい計測機器を顧客に提供できるように生産技術開発をこれからも強化していく。
また超混流生産では徹底した標準化を進め、日本国内、海外のどの工場でも同様に高い品質レベルで生産を行うとともに、生産工程で得られた貴重なデータを製品開発にフィードバックすることで、より高度な製品をより早く開発することに貢献できるものと考える。
<参考文献>
(1) 北條良光、競争力あるアズビルならではの生産体制構築に向けて-人と機械・システムとの協調を通じた生産改革-、azbil Technical Review、2018年4月発行号、p.2
(2) 経済産業省中部経済産業局、「2040年のものづくりの未来の姿」〜時流に先んじた戦略⽴案に向けて〜2040年ものづくり未来洞察調査(概要版)
(3) 田中拓哉、笠原亮介、画像を用いた自動外観検査技術、日本画像学会誌、2016年、第55巻、第3号、pp.348-354
(4) 川瀬茂、津村高志、小黒直輝、アクティブ・コンプライアンスデバイスの開発、azbil Technical Review、2009年12月発行号、pp.63-67
<商標>
Microsoft®は、米国Microsoft Corporationの米国およびその他の国における登録商標または商標です。
アクティブコンプライアンス™はアズビル株式会社の商標です。
<著者所属>
關 宏冶 アズビル株式会社 技術開発本部工程開発部
矢野 貴史 アズビル株式会社 技術開発本部工程開発部
片桐 宗和 アズビル株式会社 技術開発本部工程開発部
この記事は、技術報告書「azbil Technical Review」の2020年04月に掲載されたものです。
- 2025
- 2024
- 2023
- 2022
- 2021
- 2020
- 巻頭言:感性を計測する時代
- 特集に寄せて:多様性と一体感でイノベーションを起こす
- 赤外線アレイセンサシステム
- 制御システム向けサイバー攻撃センサの開発
- IPv6におけるノードの発見とプロミスキャスモードの検出
- 価値創出を指向するメーターデータプラットフォーム ガスミエール™
- 組合せ最適化手法によるLPガス容器配送方法とその効果
- 安全な動力プレス機械を実現するためのデュアルバルブの開発
- CFDを用いた調節弁に発生するキャビテーション壊食の予測
- 凍結乾燥機用ローダアンローダによるバイアルトレース機能の開発
- マザー工場での生産工程の革新
- 熱量演算器 WJ-1203
- マルチベンダー通信に対応するIoTゲートウェイ 形 NX-SVG
- 熱式微小液体流量計 形 F7M
- 2019
- 2018
- 2017
- 2016
- 2015
- 2014
- 2013
- 2012
- 2011
- 2009
- 2008
- 2007
- 2006