高付加価値を提供するsavic-net™ G5システムの熱源アドバンストコントローラ
キーワード:熱源アドバンストコントローラ,DDCプログラム,熱源計装,エネルギー管理,省施工,省エンジニアリング
建物の重要設備である熱源機器の制御用として、当社では30年以上にわたり熱源コントローラPARAMATRIX™を販売し、様々な熱源機器の制御のノウハウを蓄積してきた。東日本大震災以降、熱源設備の構成やその運用方法が変化してきており、さらに働き方改革の観点から省施工・省エンジニアリングが必要となっている。また、世界的にもエネルギーの有効活用は重要な課題であり、従来以上に建物における熱源コントローラの重要性が増している。これらの新たなニーズに応えるために、新ビルディングオートメーションシステムsavic-net™ G5のラインナップとして、国内だけでなくグローバル市場も見据えた熱源アドバンストコントローラを開発したのでここに報告する。
1.はじめに
当社では,長年にわたり建物の熱源設備の台数制御,圧力制御を行う熱源設備専用のコントローラであるPARAMATRIXを販売しており,建物における熱源設備の自動運転,省エネルギーに寄与してきた。そのような中,近年のビルディングオートメーション市場においては,特定のメーカーに依存しないオープンシステムが強く求められている。また,熱源設備は,東日本大震災以降,電気だけでなくガスを1次エネルギーとした熱源や蓄熱槽を利用した異種熱源混在システムが多く採用され,季節や時間帯によって運転順序を切り替える運用や,これまで以上の省エネルギー制御をする建物が増えている。さらに,建築業界全体で見ると東京オリンピック・パラリンピック需要により,建築工事に関わる人手不足が懸念されており,働き方改革による生産性向上が要望されている。
当社はこれらの背景を踏まえ,実績のあるPARAMATRIXの機能をベースに「オープンネットワーク対応」「異種熱源混在システムへの対応」「省エネ制御」「見える化」「施工・エンジニアリング負荷低減」などを実現したsavic-net G5の熱源コントローラである熱源アドバンストコントローラの新規開発を行った。また,本製品は国内市場だけでなく「グローバル市場」への販売も行っていくため,海外特有の熱源計装への対応が可能なように設計されている。
本稿では,熱源アドバンストコントローラにて提供する新たな機能とその実現技術について述べる。
2.システム概要
2.1 システム構成
熱源アドバンストコントローラを使用したsavic-net G5システム構成例を図1に示す。

図1 システム構成図
システム構成上,熱源アドバンストコントローラには下記の特長がある。
- 当社の統合コントローラをはじめ,様々な中央監視システiムとオープンネットワークBACnetで接続できる。
- コントローラ本体I/Oに加え,通信接続により拡張可能なI/Oモジュールを遠方の盤内に配置することで,遠方機器からのゾロ引き配線を不要とし,省配線を実現する。
- I/O通信のEthernet幹線をリング接続することにより,断線等の耐障害性を強化する。
- コントローラ本体に熱量計や電力量計等をModbus™またはBACnet MS/TPで接続することにより,積算値以外の全計測データについてもポイントとして監視できる。また,Modbus対応の冷凍機の内部情報をModbus経由で収集することにより,運用改善やメンテナンスに利用することも可能である。
2.2 ソフトウエア構成
ソフトウエア構成上,熱源アドバンストコントローラには下記の特長がある。
- 制御演算を行うDDCプログラムブロックを組み合わせたDDCプログラム(図2)にて送水圧力制御,始動時負荷制御,台数制御といった熱源制御のアプリケーションを構築できる。
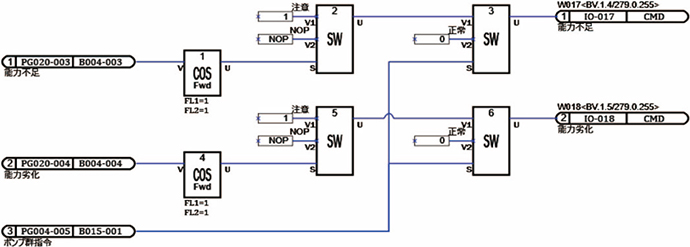
図2 DDCプログラム例
- I/O構成,ポイント構成,DDCプログラム構成を標準形番化した計装コード(表1)を用意しており,これを手配することにより,現場の計装に必要なH/W・S/W構成を入手でき,現場ごとにポイントやアプリケーションの構築が不要となる(現場では,標準形番から異なる現場計装特有部分の追加・変更のみを実施することとなる)。
表1 計装コード
WJ-1102Q①②③④⑤⑥
① 計装タイプ | ② 機器台数 | ③ 台数制御方式 | ④ 圧力制御/一次ポンプ変流量制御 | ⑤ その他 | ⑥ 電源仕様 | ||||||
1 | ワンポンプ システム | 2 | 2台 | 3 | 流量1系統(熱量演算付) | 0 | なし | 0 | 固定 | w | AC100~240V |
4 | 4台 | 4 | 流量4系統(熱量演算付,熱量4系統加算付) | 1 | 比例バイパス(電流/電圧) | ||||||
8 | 8台 | 3 | 一次ポンプ変流量制御インバータ全台+比例バイパス(電流/電圧) | ||||||||
2 | ツーポンプ システム | 2 | 2台 | 2 | 流量1系統(熱量演算付) | 0 | なし | 0 | 固定 | w | AC100~240V |
4 | 4台 | 6 | 流量4系統(熱量演算付,熱量4系統加算付) | 1 | 一次ポンプ変流量制御(負荷按分) | ||||||
8 | 8台 |
WJ-1102P①②③④⑤⑥
① 計装タイプ | ② 機器台数 | ③ 台数制御方式 | ④ 圧力制御 | ⑤ その他 | ⑥ 電源仕様 | ||||||
1 | 固定 | 2 | 2台 | 3 | 流量1系統(熱量演算付) | 0 | なし | 0 | 固定 | w | AC100~240V |
4 | 4台 | 4 | 流量4系統(熱量演算付,熱量4系統加算付) | 1 | 比例バイパス(電流/電圧) | ||||||
8 | 8台 | 3 | インバータn台+比例バイパス(電流/電圧) | ||||||||
5 | インバータ全台+ON/OFFバイパス |
- savic-net G5システム用のエンジニアリングツールに全計装コードのコントローラデータを内包しているため,従来製品と異なり,コントローラ納入前からポイント変更・追加やDDCプログラムの追加作業が開始でき,現場調整期間の短縮が期待できる。
- エンジニアリングツールのDDCプログラムエディタ機能により,現場でも容易にDDCプログラムを構築可能である。また,各プログラムブロックの出力をグラフィカルに確認でき,従来製品に比べて制御動作の確認が格段に容易となった。
3.多様な熱源計装への対応
近年見うけられるようになった多様な熱源計装や現場運用ニーズに応えるため,従来製品からの機能拡張や機能追加を行った。
3.1 機能拡張
3.1.1 熱源機台数の拡張
東日本大震災以降,熱源設備のリスク分散とピーク電力カットのためターボ冷凍機(電気),ガス吸収式冷凍機(ガス),熱交換器(蓄熱槽)といった複数種の熱源設備を時間帯や季節で切替えて運用することが増え,熱源機台数が増加傾向にある。大規模物件の場合にそれが顕著となることから,本製品ではコントローラの容量を拡大することで台数制御可能な熱源機(冷凍機/ポンプ)の台数を拡張した。これにより過去最大規模の物件でも本製品で対応できるようにした。
3.1.2 ポイント数の拡張
従来製品のポイント数は最大99点であり,これは標準形番のアプリケーションを実現する上では問題ない。しかし,複雑な制御アプリケーションをカスタマイズで追加したり,ポイント数の多い形番にカスタマイズ機能を追加する場合にポイントが足りなくなるケースがあり,アプリケーションを実現できなかったり,既存のポイントを削って何とか対処したというケースがあった。また,後述する海外の熱源計装では多数のポイントが必要となる。本製品では従来製品以上の計測・制御性能を確保した状態で,コントローラのポイント点数を300点に拡張した。これにより複雑な制御アプリケーションへも容易に対応できるようにした。
3.2 運転順序切替への対応
従来製品では1日の中での熱源機の運転順序切替として昼/夜による切替のみを想定していた。これは昼間の負荷が大きい時間帯は能力の大きい熱源機を優先して稼働することで負荷への追従性をよくし,負荷が小さい夜間(残業時間)は能力の小さい熱源機を中心に稼働することで省エネルギーを図った機能である。
しかし,1日の中でも時間帯により,熱交換器を優先した運転順序(蓄熱優先)/ガス吸収式冷凍機を中心とした運転順序(ガス優先)/ターボ冷凍機を優先した運転順序(電気優先)というように昼/夜切替のみでは対応できない運用が要求されるようになり,従来製品では対応が難しいケースがあった。
そのため,本製品ではこれらの運用を考慮した運転順序切替機能とした。機能拡張にあたっては,昼/夜切替のみで対応可能なケースも多々あるため,それらのケースでエンジニアリング方法が変わらないように,昼/夜切替機能は既存製品のままとし,それとは別に運転順序を複数パターン(最大8)設定できるようにし,いずれかのパターンを選択することにより昼テーブル内容を目的の運転順序に切り替えられるようにした(表2)。また,運転順序パターン自体はポイントで指定できるようにすることで,中央監視からのユーザーの手動操作/タイムスケジュール/DDCプログラムからの切替を実現した。特にDDCプログラムを利用することにより,切替条件への適用に対して自由度が高く,ユーザーの多種多様な要望に応えることが可能である。切替条件,運転順序パターン数については実際のJOBでのケースに適合した上で妥当性を確認した。
表2 運転順序切替例
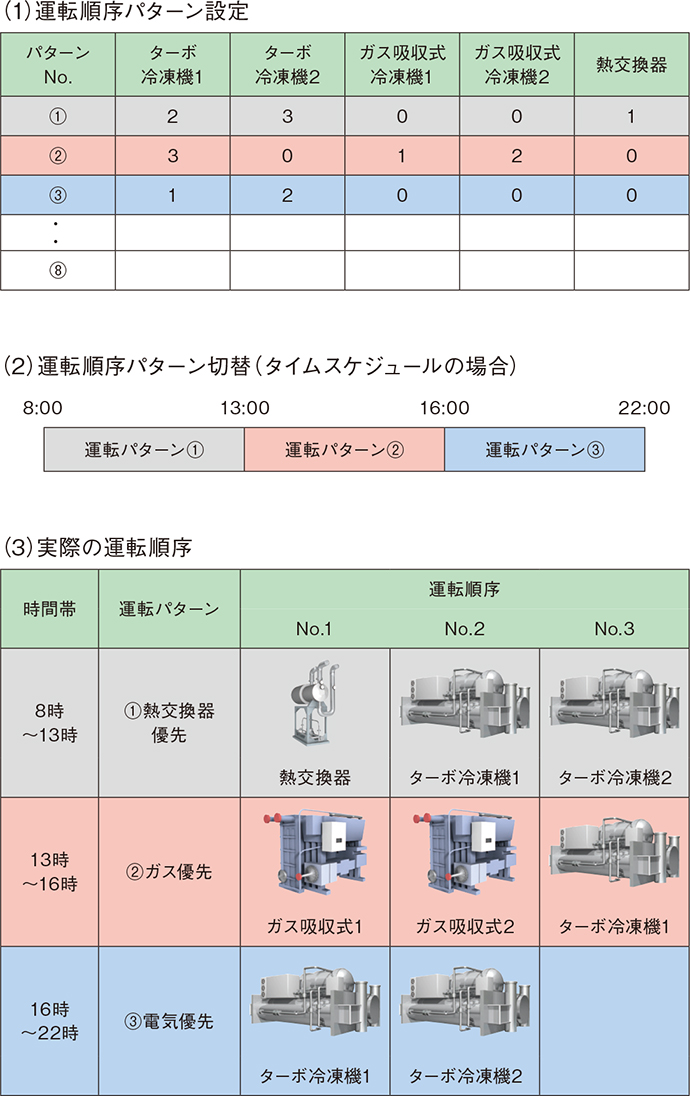
3.3 海外の熱源計装への対応
国内の熱源計装の場合,図3に示すように冷凍機と1次ポンプ・冷却水ポンプが1対1の関係になっており,冷凍機の発停により対応するポンプがシーケンス回路により連動発停する。また,自動制御メーカー(当社)が冷凍機の発停(台数制御)までを行い,ポンプとの連動発停は冷凍機メーカーが担っている。
これに対して,海外の熱源計装(日系企業を除く)の場合,図4に示すように冷凍機と1次ポンプ・冷却水ポンプが1対1ではなく,それぞれの運転機を自由に組み合わせられるようになっている。また,自動制御メーカー(当社)には冷凍機の台数制御以外に,1次ポンプ・冷却水ポンプの台数制御が求められる。
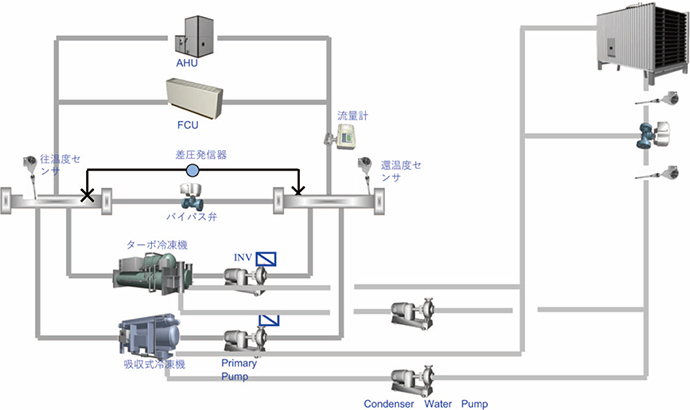
図3 日本の計装(ワンポンプシステム)
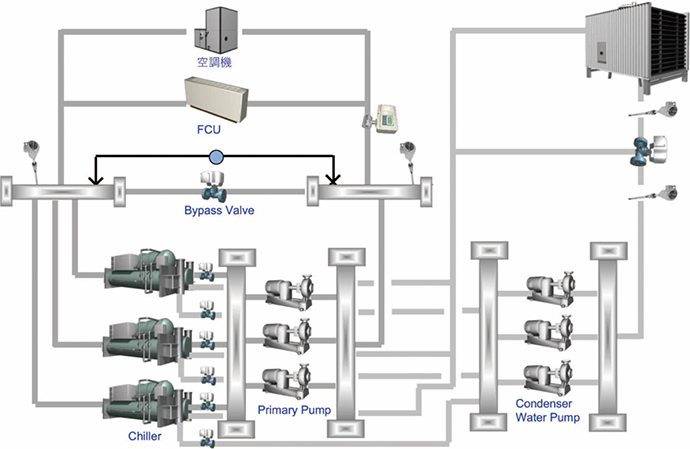
図4 海外の計装(ワンポンプシステム)
従来製品で海外の熱源計装に対応する場合,冷凍機, 1次ポンプ,冷却水ポンプ,冷却塔(台数制御の必要がある場合)の台数制御のために最大4台の熱源コントローラが必要であった。また4台でデータの連携をとるために汎用コントローラが1台必要となり多台数かつ複雑な構成となっていた。
そのため,本製品では制御容量と処理能力を大幅に向上させることで,従来製品では1つであった台数制御機能を持つDDCプログラムブロックを最大4つまで同時稼働可能とした。これにより熱源アドバンストコントローラ1台のみで4種類の熱源設備を同時に台数制御できるようにした。
4.エネルギー管理・省エネ制御への対応
現場のエネルギー管理や省エネルギー要望に応えるため,建物全体の熱源に関する消費エネルギーの見える化や新たな省エネ制御のための機能を搭載した。DDCプログラムブロックとして機能を実装することで,演算単位を熱源機個別や熱源機一括というように現場ごとに自由に組めることに加え,他のアプリケーションで演算結果を利用可能とした。
4.1 冷凍機のCOP見える化
冷凍機のCOP(Coefficient Of Performance:成績係数)は冷凍機の効率を表す指標であり生産熱量÷消費電力により求められる。本製品では,COPを演算するためのDDCプログラムブロック「CPC」を開発した。COP演算の結果1時間当たりのCOPと1日当たりのCOPを出力できるようにしたため,それらを確認することで送水温度設定見直し等の運用改善や,冷凍機内部の凝縮器や蒸発器の汚れによりCOPが悪化してきた場合のメンテナンスが容易となる。
DDCプログラムを利用すれば,COPの悪化が疑われる場合に,確認を促すようにポイント通知するといったアプリケーションを構築することも可能である。
4.2 ポンプ消費エネルギーの見える化
熱源周りのポンプ(1次ポンプ,2次ポンプ,冷却水ポンプ)の消費エネルギーを見える化する場合,今までは計量が必要であった。本製品では,図5に示すようにポンプ特性を考慮した演算アルゴリズムを開発し,DDCプログラムブロック「PC1」と「PC2」として実装することで,計量することなしにポンプ運転状態から消費電力量を演算できるようにした。これにより低コストでのポンプ消費エネルギーの見える化を実現した。

図5 「PC2」の電力量演算方法
「PC1」は1次側ポンプの消費電力量を演算するプログラムブロックであり,1~全台までの任意台数のポンプ合計消費電力量を演算できる構造とすることで,熱源機個別あるいは熱源機一括というように現場のニーズに応じた単位で演算可能である。また全ポンプが定格運転(商用運転)だった場合の消費電力量を演算できるようにすることで,現時点の消費電力量のみならず,インバータによる省エネ効果の見える化を実現した。
「PC2」は主に2次側ポンプの変流量制御(省エネ制御)を実施している場合の消費電力量を演算するプログラムブロックであり,PC1と同様に1~全台までの任意台数のポンプ合計消費電力量を演算できる構造とすることで,熱源機個別あるいは熱源機一括というように現場のニーズに応じた単位で演算可能である。また吐出圧一定だった場合および全ポンプが定格運転(商用運転)だった場合の消費電力量を演算できるようにすることで,現時点の消費電力量のみならず,変流量制御による省エネ効果とインバータによる省エネ効果の見える化を実現した(図6)。

図6 省エネ効果の確認(イメージ)
4.3 冷凍機消費エネルギーの見える化
ポンプと同様に,冷凍機の消費エネルギーを見える化する場合も今までは計量が必要であった。冷凍機の場合,そのCOPは冷却水温度で大きく変わるため,冷凍機メーカーから供給される冷却水温度条件ごとの冷凍機の負荷率-COP,もしくは負荷率-投入エネルギーの特性データをパラメータ設定しておけば,冷却水と負荷率の状態から消費電力を演算できるアルゴリズムを開発し,DDCプログラムブロック「CPT」として実装することで,計量することなしに冷凍機の消費電力を演算できるようにした(図7)。これにより低コストでの冷凍機消費エネルギーの見える化を実現した。

図7 「CPT」のイメージ図
4.4 最適台数制御への応用
通常の台数制御では負荷が1台の冷凍機能力より大きくならない限り2台に増段することはない。しかし,部分負荷効率の高い冷凍機(インバータターボ冷凍機,インバータスクリュー冷凍機)を複数台導入し,ポンプも変流量制御による省エネ制御を行っている熱源設備の場合,図8のように負荷の状態によっては1台運転ではなく2台運転させた方が熱源システムのトータル運転コストが小さくなる場合がある。
熱源アドバンストコントローラでは,前述のDDCプログラムブロック「PC2」と「CPT」を利用して,現在の運転状態での熱源システムの消費エネルギーと,増段したケースでの熱源システムの消費エネルギーをシミュレーションすることにより,増段した方が省エネルギーとなる場合には増段する最適台数制御のアプリケーションを構築できる。最適台数制御を実施することで最適タイミングでの増段となり,通常の台数制御と同様に快適性を維持するとともに,省エネ性を追求できる。

図8 最適台数制御の省エネ効果(イメージ)
5.施工・エンジニアリング負荷低減
現場の施工・エンジニアリング負荷低減の要望に応えるため,省配線化となる機構の採用やオンラインエンジニアリング機能を開発し搭載した。
5.1 施工における負荷低減
従来製品は,コントローラ本体にI/Oモジュールを直接接続する構成であったため,コントローラとやり取りする設備機器が遠方にある場合,複数の配線を設備機器の盤からコントローラの盤まで配線する必要があった。また,配線作業後に配線本数が追加となった場合には,再度配線作業を行う必要があった。
本製品ではコントローラ本体とI/Oモジュールを高速通信可能とするEthernetで接続することで,従来製品以上の計測・制御性能を確保した状態で,I/Oモジュールの分散配置を可能とした。これにより,コントローラ本体とやり取りする設備機器が遠方にある場合でも,I/Oモジュールだけを設備機器の入っている盤に設置することで,従来製品に比べて配線作業を大幅に容易とした(図9)。
また,設備機器増設等によりI/Oモジュール追加が必要となった場合でも,I/Oモジュール間のEthernetに渡り配線を採用することで,新たにHubを増設することなくI/Oモジュール間の配線のみで容易に対応できるようにした。この渡り配線にはリング接続技術を搭載することで,断線に対する耐障害性を強化した。

図9 施工における負荷低減(イメージ))
5.2 エンジニアリングにおける負荷低減
従来製品は,コントローラのファイルを修正(ファイルのダウンロード,パラメータの変更)する際,コントローラの制御を停止させる「オフラインモード」にする必要があった。そのため,建物運用後に,コントローラのファイルを修正する場合には,夜間や長期の連休などに行う必要があった。
本製品では図10のようにデータをマスタとワークの二重構造とし,ワーク領域に対するデータ設定後に関連するアプリケーションのみを停止し,そのマスタデータを更新する仕組みとすることにより,コントローラの制御を停止せずにコントローラのファイルを修正することができるようにした。これにより従来製品で1分以上あったダウンタイムがなくなり,建物運用時のメンテナンス作業を容易に行えるようにした。また,ワーク領域に対するデータ設定後には全設定間の整合性を検証し,複数アプリケーション間に渡る不整合でも検出できるため,本製品では異常設定による誤動作を回避することを可能とした。

図10 オンラインエンジニアリングの仕組み)
6.今後の展開
データセンターやDHC(District Heating and Cooling:地域冷暖房)の市場では,万一,コントローラが故障した場合にも迅速に代替機に切替え,制御を継続できるような「コントローラの二重化」が求められる。
コントローラの二重化では,図11のようなシステム構成とする。アクティブ系とスタンバイ系のコントローラは相互に状態監視を行い,また上位,下位のネットワークの通信状態を監視する。万一,アクティブ系のコントローラが故障,または通信異常となった場合,スタンバイ系のコントローラがアクティブ状態に切り替わり,制御を継続実行する。
「コントローラの二重化」システムは,今後リリースする予定である。

図11 コントローラの二重化(イメージ)
7.おわりに
熱源アドバンストコントローラの全体像と,従来製品と比較して新たに現場に提供できる機能について紹介した。今後は先の二重化に加えて,基本機能として蓄熱制御機能の追加を予定している。また統合コントローラ側との連携を強化していくことにより,ビッグデータの利用による制御目標値の予測やパラメータ更新による運用改善,さらなる省エネ制御機能を提供していきたい。
<商標>
savic-net,PARAMATRIXはアズビル株式会社の商標です。
Ethernetは富士フイルムビジネスイノベーション株式会社の日本または他の国における商標です。
Modbus is a trademark and the property of Schneider Electric SE, its subsidiaries and affiliated companies.
<著者所属>
久保田 秀雄 アズビル株式会社 ビルシステムカンパニー開発本部開発2部
関根 秀太 アズビル株式会社 ビルシステムカンパニープロダクトマーケティング部
この記事は、技術報告書「azbil Technical Review」の2019年04月に掲載されたものです。
- 2025
- 2024
- 2023
- 2022
- 2021
- 2020
- 2019
- 巻頭言:革新的技術への社会の適応
- 特集に寄せて:ビルに新たな付加価値をもたらす空調制御を考える
- 快適空間制御を実現するための3次元温熱環境可視化システムの開発
- 居住者の温冷感情報を活用する新しい快適性評価技術の開発─個別単位の環境満足度を評価する
- 高度なエネルギー管理と快適な空間を提供するsavic-net™ G5システムの統合コントローラ
- 建物ライフサイクルを支えるsavic-net™ G5システムのリモートコントローラ
- 高付加価値を提供するsavic-net™ G5システムの熱源アドバンストコントローラ
- 大口径流量計測制御機能付きバルブの流量計測精度向上技術
- 全館空調VAVシステム用集中リモコンの開発
- 放電音を防止した電子式エアクリーナの開発
- 微小液体流量の計測を可能にする熱式液体微小流量計の開発
- 組立作業ミスの予測・通知技術の開発
- 2018
- 2017
- 2016
- 2015
- 2014
- 2013
- 2012
- 2011
- 2009
- 2008
- 2007
- 2006