組立作業ミスの予測・通知技術の開発
キーワード:ポカミス,ヒューマンエラー,AI(Artificial Intelligence),機械学習,予測,通知
近年のものづくりでは、グローバル競争力の強化のため、IoT(Internet of Things)やAI(Artificial Intelligence)などを活用し、品質の向上や生産性の向上などを目的としたスマート化が重要と考えられており、そのスマート化の目的の1つにポカミス削減が挙げられている(1)。本稿では、このヒューマンエラーであるポカミスに着目し、AIの技術である機械学習によって作業者の思い込みによるポカミスを予測し、ミスしそうな注意点を作業の前に通知する技術を開発したので報告する。この技術によりポカミスを抑制することで、製品品質の確保と生産性向上に寄与できると考える。
1.はじめに
近年のものづくり企業では,グローバル競争力の強化のため,第4次産業革命をもたらしつつあるIoTやビッグデータ,AI,ロボットなどの技術を活用し,品質の向上や生産性の向上などを目的としたスマート化が重要と考えられている(1)。そのなかで,ものづくりの現場では,現在も「人」が作業する工程があり,この「人」の作業にともなうスマート化の目的の1つにポカミス削減が挙げられている。
そこで,このポカミスをヒューマンエラーととらえ,その要因から考える。ヒューマンエラーの要因は,12分類あると言われている(2)。このヒューマンエラー要因の12分類を図1-1のように「経験」「作業環境」「情報不備」「作業者の状態」の4つのグループに分けて考える。
「経験」「作業環境」「情報不備」の要因グループに関しては,現場作業者の訓練や教育,作業環境の改善,MES (Manufacturing Execution System:製造実行システム)などのシステム導入によりヒューマンエラーを減らすことができるが,「作業者の状態」は常に変化し続けるため,これを起因とするヒューマンエラーへの対策は難しいと考える。例えば,単調作業や疲労からの集中力低下,工程進捗による焦りやストレスなどが要因になるヒューマンエラーである。
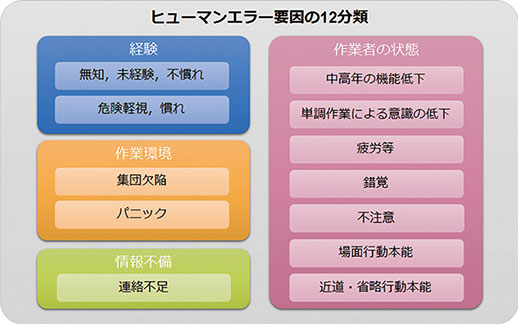
図1-1 ヒューマンエラー要因の12分類
このような作業者の集中力や注意力が低下した状態では,図1-2のような作業指示(指図)の各項目が都度変わる多品種少量生産の現場環境において,実際の指図とは異なった作業をしてしまうというポカミスが懸念される。
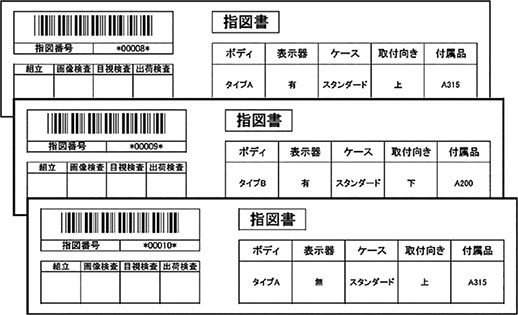
図1-2 指図書イメージ
これは,図1-3のように作業者は作業前に指図を見てはいるものの,直近や過去に多く作業していた指図内容と同じと思い込んで誤認知し,指図内容の違いを見落としてしまうと考えられる。
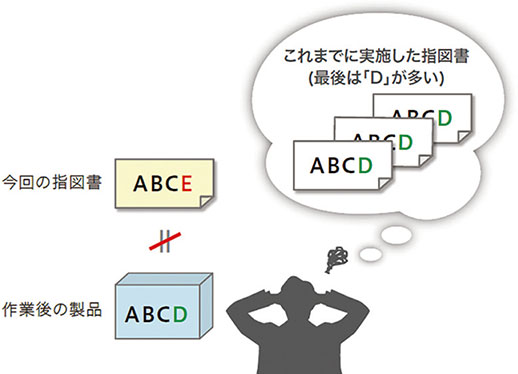
図1-3 思い込みによるポカミスの一例
上記の思い込みによるポカミスは,発生すると工程の手戻りとなり,場合によっては製品の廃棄が必要になることがある。また,後の検査工程で不適合を検出できなければ,お客さまに仕様が異なった製品が流出することにより顧客クレームとなる。
このような生産性や製品品質に影響を与える思い込みによるポカミスを削減するには,作業者が作業後ではなく作業前に自ら注意点を認知し,そもそもポカミスをしないことが最善である。
そこで,筆者らは,AIの技術である機械学習によって作業者の思い込みによるポカミスを予測し,ミスしそうな注意点を作業前に通知する技術(図1-4)を開発した。次章で,この技術に関して説明する。
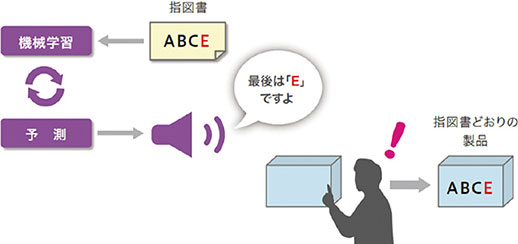
図1-4 作業ミスの予測・通知のイメージ
2.作業ミスの予測・通知技術
2.1 入出力と教師データ
まず,作業者の思い込みによりポカミスしやすい箇所を予測するため,作業者の「思い込み」を機械学習のモデル対象として考えた。
与えられた指図をもとに作業する「作業者」を1つのシステムととらえると,図2-1のように,入力は作業者がそれまで過去に実施した指図の情報であり,出力はその作業者の思い込みの内容になる。この出力,つまり作業者の思い込みの内容も指図の情報である。そのため,入力も出力も指図の情報という形をとるモデルとなる。

図2-1 入出力
また,このモデルを学習させるための教師データは,作業者の「思い込み」の「学習」と考えれば,作業者が実際に実施した指図情報とすればよい。
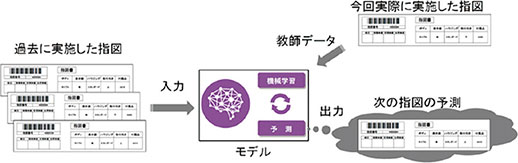
図2-2 教師データと学習
なお,作業後の検査工程でポカミスが見つかった際,その間違えた指図情報が利用できれば,実際にミスした内容で教師データ用の指図情報を作り,学習することで,作業者の「思い込み」のモデルは,さらに精度向上が見込める。
2.2 学習モデル
次に,機械学習のモデルについて示す。
「思い込み」に関しては,認知と記憶が大きく関係している。それは,認知された情報が記憶となり,その記憶に基づいて判断・行動が行われると考えられるためである。この「記憶」には直近の情報を処理するためのワーキングメモリと呼ばれる短期記憶と,繰り返し経験することで形成される長期記憶があると言われている(3)。工場での組立工程に例えると,「赤色の蓋が続いている」といった直近の作業が短期記憶に相当し,「この型番の製品には,この部品が使われることが多い(全てがそうではない)」といった経験に基づく記憶が長期記憶に相当すると考えられる。
この2つの記憶のモデル化に対して,時系列データを学習してモデル化できる再帰型ニューラルネットワークRNN (Recurrent Neural Network)に属するLSTM(Long Short-Term Memory)アルゴリズム(4)を適用する。このLSTMアルゴリズムを応用したモデルを適用するのは,時系列のデータを繰り返し学習させることで,「赤色の蓋が続いている」といった時系列のパターン(短期記憶)や,「この型番の製品には,この部品が使われることが多い(全てがそうではない)」といった各々の入力項目の相関関係(長期記憶)を学習できると考えたからである。このモデルは,実際の次の指図情報を正確に予測するモデルではなく,過去に実施した指図から次の指図を予測(思い込み)する作業者のモデルである。
なお,作業者の思い込みは新しい指図の作業を行うたびに変わるため,この「思い込み」のモデルは作業するたびに学習して更新する必要がある。そのため,今回実施した指図情報を教師データとして,モデルを学習により更新する。
ここまでの流れをまとめると,図2-1のように,入力としてそれまでに行った指図情報を順に与えることで,出力である作業者の思い込みの内容を予測する。
次に,図2-3のように,その予測と今回実施すべき指図情報との差(スコア)が大きい項目が「思い込み」によるポカミスしやすい箇所となる。
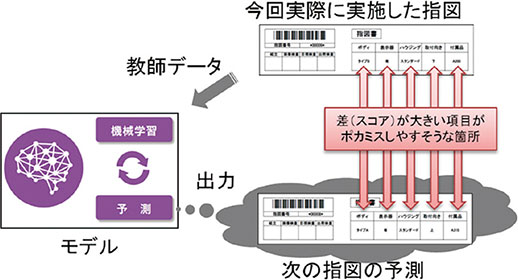
図2-3 ポカミスしやすい箇所
さらに,今回実施した指図情報を新たに教師データとして学習させ,モデルを更新した後,今回実施した指図情報を入力に加えることで,次の思い込みの予測ができるようになる。
2.3 作業者への通知方法
作業者に対しての思い込みによるポカミスの注意通知方法は,現場端末の画面とともに,スピーカによる音声でも通知することとした。現場に設置した端末画面での通知のみとすると,従来の「指図を確認して,作業する」といった作業の流れに,「注意点を画面で確認する」という追加の作業が発生する。注意点がない場合にも画面の確認が必要であるとすると,常に無駄な意識移動や作業時間のロスが発生する。音声併用ならば,注意点の有無と内容を作業準備中に聞きながら情報を得ることができ,聞き逃した場合にも画面の表示で確認できるからである。
また,音声で常に注意点が通知されると,その音声が作業者にとっての定常的な刺激となり,その刺激への慣れ(馴化)が発生し,作業者が通知に気付かなくなる可能性がある。そのため,本システムでは,ポカミスしそうなスコアを算出し,閾値によって通知の有無,さらには通知内容を切り替えることで対応した。なお,音声は音声合成の技術を使用している。
2.4 処理フロー
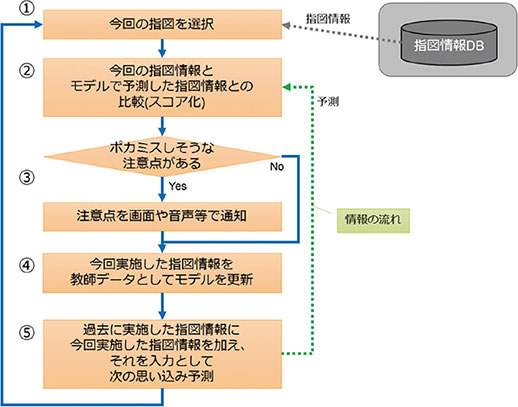
図2-4 処理フロー
(1) 作業者が今回実施する指図(情報)を選択する。
(2) 本システムは事前に予測していた思い込みの指図情報と今回実施する指図情報を比較して差異をスコア化する。このスコアが大きい項目が,ポカミスしそうな箇所となる。なお,ポカミスしそうな注意点の有無の判定や通知内容を決定するための閾値は,運用に合わせて調整できる。
(3) ポカミスしそうな注意点があれば端末の画面や音声で築通知する。
(4) 今回実施した指図情報を教師データとしてモデルを更新する。。
(5) モデルの更新が終わった後,今回実施した指図情報を直近の入力として加えることで,次の思い込みの指図情報(予測)を出力する。
なお,当然であるが「思い込み」は人それぞれに異なるため,この「思い込み」のモデルは作業者ごとに作成する。
2.5 システムの有用性
本システムの有用な点は,ポカミスしそうな箇所を1つのみ予測するのではなく,対象とする作業項目全てに対してミスしそうなスコアを算出できる点である。そのため,そのスコア,つまりポカミスしそうな危険度の順に通知することや,図2-5のように電子的な指図の画面などで注意すべき項目を危険度に応じて色分けしてハイライト表示することもできる。

図2-5 ハイライト表示のイメージ
上記の特長は,指図情報の単純な変化検出では実現できない優位点である。
また,機械学習を用いたシステムの導入において,課題となるのが事前準備作業である。例えば,学習用の大量のデータの準備や,その教師データのラベリング作業(正解を教える作業),学習時間やパラメータのチューニングなどである。しかし,本システムでは,過去の指図情報のみで各々の入力項目の相関関係(長期記憶)の事前学習が可能であり,導入後,およそ数十回の使用でその作業者が実施した指図情報の時系列のパターン(短期記憶)の学習ができるため,短期間かつ少ない労力でその作業者のモデルとして使用できるのである。
3.システム導入の効果
ご協力いただいた工場の多品種少量製品の組立工程において,ポカミスが多い11の作業項目を対象として,図3-1の構成で実証検証を実施した。
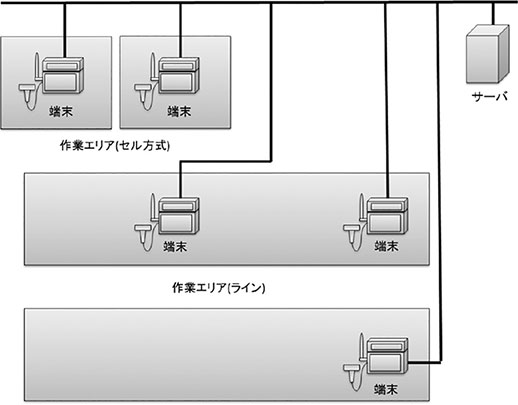
図3-1 設置イメージ
図3-1に示されたサーバは,指図情報を管理するデータベースと指図を学習して作業項目の注意点の予測を行うエンジンを搭載している。作業エリアには作業項目の注意点を通知する端末を設置し,ネットワークで接続した。なお,事前学習には約1カ月分の過去の指図情報を使用した。
作業者の変更やラインの変更などにより定常的な検証データが3カ月分しか収集できなかったが,工程内検査において対象項目の不適合の割合が導入前1年間と比較して約3割抑制された。
また,この間の指図の注意点の通知を記録したログを分析した結果,ある指図においてポカミスしそうな項目の注意点が通知されていたが,その後の工程内検査でその指図の同項目の不適合が検出された。これは,本システムでポカミスを事前に予測・通知できていたが,作業者が聞き逃したことを示している。通知方法を改善することで,さらにポカミス発生を抑制されることが期待できる。
この検査工程での不適合検出件数の減少は,検査工程から組立工程への手戻りが減っていることを示し,同時に作業品質も上がっていることを示している。また,ポカミスが減ることで作業者が検査員からポカミスを指摘される回数も減り,お互いのストレス軽減にもつながっていると考えられる。
なお,本実証検証においては,組立工程の作業者が作業前に指図を特定するバーコードをバーコードリーダで読み取るだけで,その指図の注意点が端末の画面とスピーカからの音声で通知されるように構成した。これにより,作業者は従来の作業の流れを乱すことなくポカミスに関する要注意情報を得られるとともに,その指図の作業開始をシステムに記録できるようになった。
この作業開始の記録は,いつ,誰が,どこで作業したかの記録であり,「人」が実行する工程の実績データとして工程管理に利用できるだけでなく,さらには,この記録と検査工程での検査記録を結びつけることで工程改善や作業者への教育にも活用することができる。
5.おわりに
今回,ヒューマンエラー対策の1つとして作業者の思い込みによるうっかり作業ミス(ポカミス)に焦点を絞り,AIの技術である機械学習を応用した作業ミスの予測・通知技術を開発した。
今後は,ポカミス予測機能の向上と作業者へのより適切な通知方法の検討・改善を行っていきたい。また,本システム導入によってヒューマンエラーがゼロにできるわけではない。ヒューマンエラーにはほかにも多くの要因があり,その要因に合った対策が必要である。それぞれの要因に適合する解決策を検討・実施していきたい。
なお,本システムは当社の新しい製造実行システム(MES)のヒューマンエラー防止機能の1つとして提供することを検討している。これら機能とシームレスに連携できるMESによって,お客さまの品質確保,生産性向上へ貢献したいと考えている。
<参考文献>
(1) 第4次産業革命期におけるIoT・ロボット導入促進調査「ものづくりスマート化ロードマップ調査」調査報告書」2017年3月 経済産業省 中部経済産業局
(2) 「安全活動にカツを入れる本」中村秀樹・高木元也・志 村満・降籏達生 (2007) 労働調査会
(3) 「認知心理学」箱田 裕司,都築 誉史,川畑 秀明,萩原 滋 有斐閣社(2010/6/30)
(4) 「Learning to Forget: Continual Prediction with LSTM」 Felix A. Gers, Jurgen Schmidhuber, Fred Cummins Article in Neural Computation・October 2000
<著者所属>
近藤 政紀 アズビル株式会社 AIソリューション推進部
北條 達也 アズビル株式会社 ITソリューション本部ITソリューション開発部
この記事は、技術報告書「azbil Technical Review」の2019年04月に掲載されたものです。
- 2025
- 2024
- 2023
- 2022
- 2021
- 2020
- 2019
- 巻頭言:革新的技術への社会の適応
- 特集に寄せて:ビルに新たな付加価値をもたらす空調制御を考える
- 快適空間制御を実現するための3次元温熱環境可視化システムの開発
- 居住者の温冷感情報を活用する新しい快適性評価技術の開発─個別単位の環境満足度を評価する
- 高度なエネルギー管理と快適な空間を提供するsavic-net™ G5システムの統合コントローラ
- 建物ライフサイクルを支えるsavic-net™ G5システムのリモートコントローラ
- 高付加価値を提供するsavic-net™ G5システムの熱源アドバンストコントローラ
- 大口径流量計測制御機能付きバルブの流量計測精度向上技術
- 全館空調VAVシステム用集中リモコンの開発
- 放電音を防止した電子式エアクリーナの開発
- 微小液体流量の計測を可能にする熱式液体微小流量計の開発
- 組立作業ミスの予測・通知技術の開発
- 2018
- 2017
- 2016
- 2015
- 2014
- 2013
- 2012
- 2011
- 2009
- 2008
- 2007
- 2006