アズビルMEMSの歴史と今後の展望
キーワード:MEMS,圧力センサ,ピエゾ抵抗式,サファイア,マイクロフローセンサ,MRセンサ,耐食性
「計測と制御」の技術を活用し,「人々の安心,快適,達成感の実現」と「地球環境への貢献」を追求しているアズビルにとって,センサはキーコンポーネントの1つであり,MEMSは高性能で付加価値の高いセンサを実現する上で非常に重要な基幹技術である。早くからその有用性に注目して,1980年代半ばにはクリーンルームの建設とMEMSセンサの研究開発を開始し,これまでに様々なMEMSセンサを自社開発して多くの製品に搭載してきた。今回は主要なMEMSセンサの歴史や技術,特長を紹介するとともに,今後の展望について述べる。
1.はじめに
MEMSとはMicro Electro Mechanical Systems(微小電気機械システム)の頭文字をとった略称であり,電子デバイスの中に電気的な要素だけではなく,3次元的な加工を活用するなどして機械的な要素を組み込んだデバイスであり,近年はセンサへの応用が盛んである。
MEMSが研究され始めたのは1950~1960年代といわれており,国内では1960年代に自動車関連の企業からMEMS式の圧力センサが発表された。アズビルは,1980年代半ばにエレクトロニクス関連の研究開発テーマを検討する中で,事業内容とのマッチングが良く,少量多品種で差別化が可能と考えられるセンサに的を絞りMEMSの研究開発に注力する戦略を選択した。アズビルが得意とする工業市場向けのセンサは,高精度,高信頼性,長寿命,低消費電力,長期にわたる安定供給等,様々な項目において高いレベルで求められるために,市販品では対応が困難なものも多い。自社製品用にカスタマイズしたMEMSセンサを開発して,製品に大きな差異化要素や付加価値を付ける必要があった。当初はクリーンルームもなく, まさにゼロからのスタートであったが,それから37年余りが経過し,様々なMEMSセンサが開発され自社製品に搭載された。上市して30年以上になるマイクロフローセンサ™を筆頭に,現在も生産を継続しているセンサが多数ある。MEMSセンサはその材料や構造,製作プロセスなどが一品一葉であり,開発に非常に多くの時間と労力を要するが,一方でその特殊性や困難性,市場規模などから比較的高い参入障壁があり,ひとたび開発されたセンサは長期にわたり高い競争優位性を有するものが多い。図1にアズビルにおけるMEMS開発の軌跡を示す。
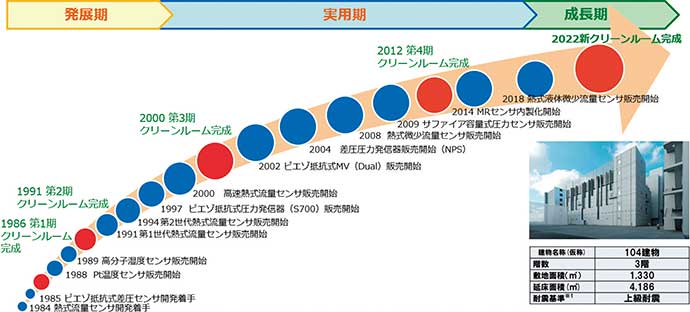
図1 MEMS開発の軌跡
2.主要なMEMSセンサ
これまでにMEMS技術を活用して開発したマイクロフローセンサ,ピエゾ抵抗式差圧・圧力センサ,サファイア静電容量式圧力センサ,MR(Magneto Resistive)センサの4種について,歴史や技術の独自性,今後の展望などについて述べる。
2.1 マイクロフローセンサ
1984年に気体向けのMEMS型フローセンサの研究開発に着手し,1994年に給湯器の空燃比制御用の空気流量センサとして量産が開始された。その後,高流速向けや微小流量向けなどセンサチップのラインアップを拡充し,適用する流速や流量域を拡大するとともに,制御バルブを組み込んだマスフローコントローラーも製品化した。さらに2017年には気体用で培ったMEMS技術を応用して,微小液体向けのフローセンサを開発した(1)。これまでのフローセンサの累計販売台数は600万台を超えた。図2にマイクロフローセンサ応用製品例を示す。
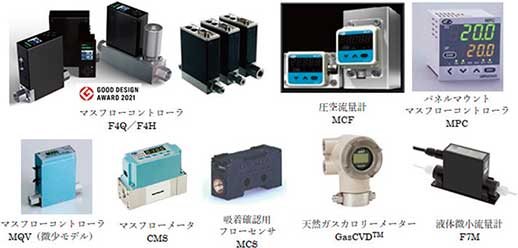
図2 マイクロフローセンサ応用製品例
2.1.1 センサの構造と独自技術
フローセンサチップは,1.7mm角のシリコン基台に厚さ約1μmの窒化シリコン製ダイアフラムを形成し,その中央に白金薄膜で形成したヒータおよび上下流温度センサを配置している。ダイアフラム下部は異方性エッチング技術を利用して中空構造となっているために,流速検知部分の熱容量が極めて小さく,高感度,高速応答,低消費電力などの特長をもつ。
フローセンサを製作する上で重要になるのがダイアフラムとなる窒化シリコンの膜質である。厚さが1μmに対してダイアフラムの対角線長は1mmを越えており,非常にハイアスペクトな構造であるため,膜の内部応力が大きいと平坦なダイアフラムが形成できない。ダイアフラムの撓みはセンサ出力のバラツキやシフト,信頼性などに影響を与えるために,極めて低い応力の膜が必要となる。一方で,この窒化シリコン膜は流速検知部のヒーターや温度センサの白金薄膜を保護する役目も担っており,段差被覆性が良く,長時間の異方性エッチングにも耐えるように緻密でなければならない。一般的に緻密な膜は内部応力が高くなるが,独自の成膜プロセスを開発し,低応力でありながら所望の段差被覆性,耐薬品性,緻密性を満たすことに成功した。さらにこの膜は高温,低温,高湿度等の様々な環境下においても応力変動が極めて小さく,ゼロ点や感度などの特性シフトが極めて少ないフローセンサの実現に貢献している。図3にダイアフラムの平坦性が分かるようにセンサチップを割断した電子顕微鏡写真を示す。
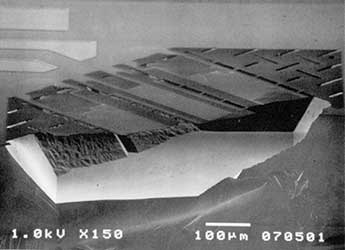
図3 割断したセンサチップの電子顕微鏡写真
2.1.2 フローセンサラインアップ
最初に開発したフローセンサは搭載製品の特長から低流速域を精度良く計測するものであったが,様々な流量域の製品を拡充する中で,高流速までの広い流速域を計測するニーズが高まった。熱式のフローセンサは,ヒーターと上下流の温度センサの距離により流速感度が調整できるため,高流速向けのセンサチップを開発した。その後,新たに微小流量域の計測ニーズが顕在化したが,センサを流路に挿入する従来構造では,流路の断面積が広く流速が遅すぎて精度の良い計測は不可能であった。そこでMEMS技術を駆使して幅1mm,高さ0.5mmの微小な流路を製作し,それをセンサチップの表面に貼り付けた流路一体型構造のフローセンサを開発した。これら3種類のセンサチップラインアップにより,5mL/minの微小流量から2500L/minまでの広い流量域をカバーしている。図4にフローセンサチップラインアップを示す。
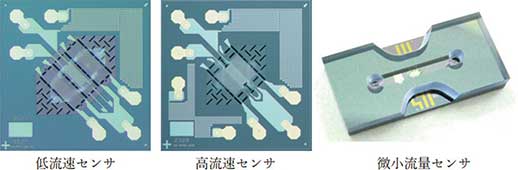
図4 フローセンサチップラインアップ
フローセンサの開発は気体向けにとどまらず液体向けにも対象を広げている。熱式の特長を活かすために微小流量域を中心として,精度や応答速度の向上,流量レンジや適用液種の拡大等を目指して製品開発を続けている。
2.2 ピエゾ抵抗式差圧・圧力センサ
ピエゾ抵抗式センサの歴史は古い。応力により抵抗率が変化するピエゾ抵抗効果は1950年代に発見されており(2), 1962年にHoneywell社(3)で,国内では1964年に株式会社 豊田中央研究所(4)で圧力センサとして発表され,安価な民生機器や自動車向けを中心にその応用範囲を広げてきた。
その後,1983年に工業用途としてHoneywell社からスマート形差圧/圧力発信器ST3000が販売された。1985年に当時は山武ハネウエルであった当社は,パッケージのコストダウンを提案し,さらに1986年には微差圧センサの共同開発を開始し,本格的に圧力センサの開発に着手した。 1991年にはイオン注入機や酸化拡散炉を導入し,完全内製の開発体制を整え,まずはHoneywell社にないラインアップの製品化を進めてきた。1995年には圧力計Bravolight™(5)を開発し,2002年には,センサチップを差圧計測用と静圧計測用に2個使用して質量流量が計測可能なマルチバリアブル型のセンサ(6)の開発を行った。これ以降,マルチバリアブルセンサとしては,工場のエア管理用フローメーターAIRcube™,蒸気流量計STEAMcube™,温度・圧力補正型差圧発信器の開発,販売へと続いた。2004年には,主力製品である差圧・圧力発信器Model GTXに繋がる高精度なセンサを開発し,近年,生産台数累計100万台を突破した(図5)。
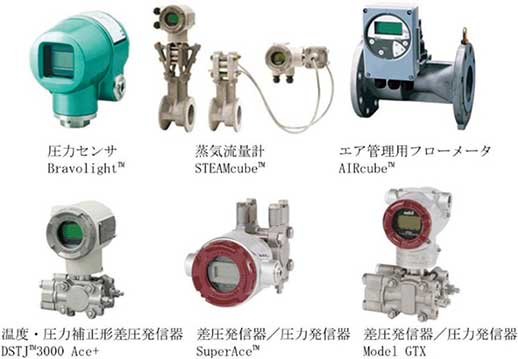
図5 ピエゾ抵抗式圧力センサの製品ラインアップ
2.2.1 ピエゾ抵抗式圧力センサの特長的な独自技術
これらの産業用途で使われる圧力センサは,精度や性能だけでなく高度な信頼性も要求され,製品寿命は非常に長い。次に,この高精度,高信頼性を実現させた独自の高度な内製技術について紹介する。図6に最も代表的な差圧圧力発信器のチップとパッケージを示す。
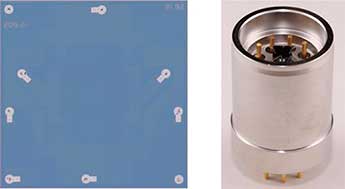
図6 ピエゾ抵抗式圧力センサのチップとパッケージ
Siチップと電気的絶縁のために使用しているガラス台座やパッケージのボディとして使用しているステンレスといった異種材料との界面では,温度変化や静圧により歪(ひずみ)が発生する。これはすべてノイズ成分となるため,接合部における面積やその接合形状について,構造解析を駆使しピエゾ抵抗素子までは伝わらない構造を採用している。温度センサや静圧センサも別途搭載し,それぞれに補正を行っているが,ノイズ成分を徹底的に排除することを追究し,高精度化を実現している。
次に安定性,信頼性については,ピエゾ抵抗素子を形成する不純物濃度プロファイルを独自に最適化したことに加え,表面Si酸化膜層のNa+等のイオン性不純物の耐性を向上させたことで,精度保証範囲外である限界動作条件下の125℃においても12000時間以上で0.01%FSの精度を達成し,極めて高度な安定性,信頼性を実現している(7)。なお12000時間以後は,過酷な試験環境下を続けたことで,先に恒温槽が故障してしまい試験の継続断念を余儀なくされたが,この時点でセンサは完全に正常な状態を保っていたことを付け加えておく。
2.2.2 今後の展望
ピエゾ抵抗式圧力センサは,既に非常に高い完成度を持っているが,今なお進化を続けている。差圧センサにおける耐圧力について,現時点でもチップの裏側加圧となるLow Pressure側の耐圧力には,例えば測定圧力100kPaレンジでは,その約70倍の7MPaを達成している。この耐圧力は今後も圧倒的に高いレベルで更新するべく追究を続けている。
2.3 サファイア静電容量式圧力センサ
工業用途の圧力センサにはシリコンを基材としたものが多く用いられているが,耐食性を確保するために金属のバリアダイアフラムを備えたオイル封入構造となっているものが多い。そのために封入オイルの性能が1つの制約となり,高温や超低真空の計測が困難であるとともに,オイル漏出を嫌う食品や医化学薬品,半導体製造分野などからは敬遠されがちである。これらの問題を解決するために,耐食性や耐熱性が高いサファイアという材料に注目して圧力センサへの応用技術開発を進め,オイル封入が不要なサファイア静電容量式圧力センサを2009年に開発した(8)。現在の主な用途は半導体製造装置のプロセスチャンバー内の圧力計測である。様々な腐食性ガスが利用されるために,サファイアの耐食性が活かされ,MEMSによる小型化メリットもある。図7にセンサチップとパッケージの模式図を示す。
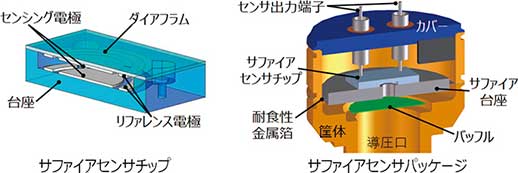
図7 サファイアセンサチップとパッケージ模式図
2.3.1 サファイア圧力センサの特長的な独自技術
センサチップの製作プロセスにおいて,異種材料を介在させずにサファイア同士を接合する直接接合技術を開発した。サファイア製のキャビティ部基板とダイアフラム部基板に表面清浄化処理を施して,位置合わせと加圧接着を行い,さらに加熱処理することでサファイア同士が強固に接合されセンサの感圧部が形成される。断面TEM(Transmission Electron Microscope)像から原子レベルで接合されていることが分かる(図8)。
また,センサチップをパッケージ筐体に固定する際に,耐食性の確保と機械的・熱的応力の低減が求められる。この方策として両者の間に耐食性金属の薄板を介在させて応力低減を図るとともに,その接合には拡散接合を適用した。必要な強度,耐食性,耐熱性,気密性を有しており,TEM像によると原子レベルでの接合を確認することができる(図9)。
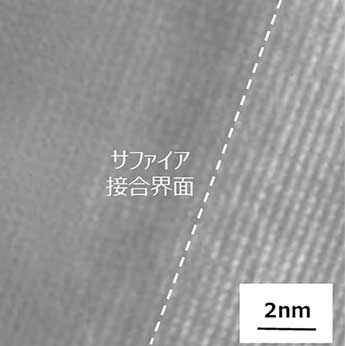
図8 サファイア直接接合部の断面TEM像
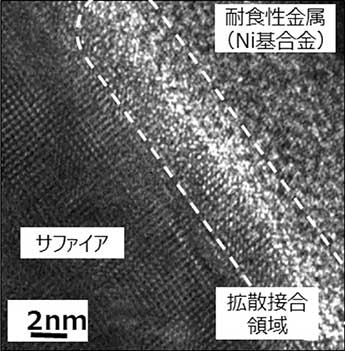
図9 拡散接合部の断面TEM像
2.3.2 サファイアの耐食性
サファイア自体の耐食性が高いことは周知の事実であるが,半導体プロセスで使われる腐食性ガスに対する耐食性には不明な部分が多い。そこで大阪大学と共同研究を実施してサファイアの耐食性に関する共同研究を進めている(9)。評価時の帯電問題があるために,サファイアの代わりに酸化アルミニウム多結晶膜(\({Al}_2{O}_3\))を利用して,ArおよびF,Clのイオンビーム照射に対するエッチング速度を計測したところ,耐食性金属のインコネルよりエッチング速度が遅く有利なことが明らかになった。図10に各種ガスにおける材料別のエッチング速度比較を示す。今後はサファイアでの実験を進めて行く予定である。
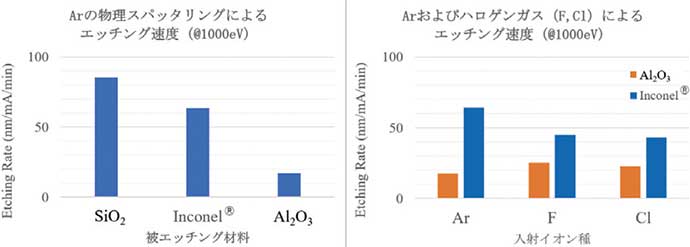
図10 各種ガスにおける材料別エッチング速度比較
2.3.3 今後の展望
進化が著しい半導体プロセスのニーズに応えるために,サファイアという材料の優位性を活かしながら,現行製品のセンサ構造を大きく改良し,小型化,高耐圧化,低コスト化などを図ったリニューアルモデルを開発している。さらに,半導体プロセスで課題となっている,センサ表面への反応生成物堆積に起因した特性シフトの対策や(10),新たなプロセス用材料ガスに対応するための動作温度高温化など様々な施策を進め,サファイア圧力センサの応用範囲拡大を図っていく。
2.4 MR(Magneto Resistive)センサ
MRセンサはバルブ位置検知用センサとして,スマート・バルブ・ポジショナ300シリーズおよび700シリーズに搭載されている。このセンサは,それまでは社外から調達していたが,供給メーカーの事業撤退を受け,長期にわたり安定的に入手する必要性から,2009年から内製開発を開始し,2013年に開発が完了して製品への搭載を開始した。製品適用から9年以上経過し,累計生産数は55万台に達したが,フィールドでのセンサ起因の故障は1件も報告されておらず,非常に信頼性の高いセンサとなっている。
2.4.1 センサ構造と独自技術
MRセンサは強磁性金属薄膜の異方性磁気抵抗効果 (AMR効果) を利用したものである。薄膜に印加する電流と外部から印加した磁界の相対角度\(θ\)によって電気抵抗\(R\)が変化し,温度が一定であれば式(1)のように表される。
センサチップは2mm角のガラス基台に強磁性体のNiFe膜をつづら折り形状にして,パターン長手方向を90度回転させた4つの抵抗でブリッジを形成している。角度センサ(ポテンショメータ)として動作させるために,回転するローターにネオジム製マグネット2個でセンサチップを挟むように固定して磁界を印加する構造になっている(図11)。
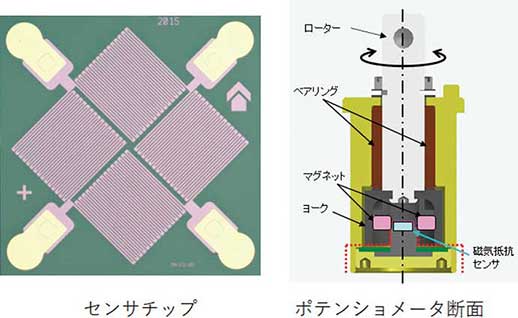
図11 センサの構造
バルブポジショナは産業用機器であり,高精度,高信頼性,長寿命,低消費電力等が要求される。低消費電力については4-20mAの計装電流のみで他に搭載された電気回路を含めて駆動させる必要があり,センサは10kΩと高い抵抗値が求められた。磁気特性も鑑みてNiFeの膜厚は30nmと非常に薄い膜厚を採用している。
NiFe膜は外部から印加される磁界以外にも,応力が加わると抵抗値が変化して計測精度が悪化するため,応力低減に配慮している。NiFe膜の表面に形成するパッシベーション膜には,マイクロフローセンサで培った低応力で緻密な窒化シリコン膜を利用しているが,成膜条件によって特性のシフト量が変化するため,MRセンサ用に特性シフトが少なくなる成膜条件の最適化を行った。ほかにはチップを固定する接着剤や表面コーティング剤の硬化応力にも敏感に反応するため,硬化後のヤング率が低くセンサチップに応力を与えない接着剤やコーティング剤を選定し,塗布量や塗布条件なども最適化した。
また,センサチップの中心と磁界の回転中心がずれると,センサの出力が理想のsinカーブから外れて計測精度が悪化する。この課題に対しては,磁気シミュレーションの活用と実験により許容位置ズレ量を明確にして,各部品の公差設計を行った。特にセンサチップを搭載するセンサホルダという部品には,樹脂成型の寸法精度が高い熱硬化性樹脂を採用するとともに,センサチップを搭載する際に,位置ズレが許容範囲以内になるようにアライメント機構を組み込む工夫を行った。
2.4.2 今後の展望
バルブポジショナ向けのMRセンサ開発で磁気センサの要素技術を獲得したが,我々がビジネスを行っているフィールドでは,バルブ以外にもポジションを検知したい対象物は数多くある。磁気センサは非接触でのポジション検知が可能であり,耐環境性や信頼性の面で非常に有利であるとともに,消費電流も小さく低コストである。この技術を応用して計測対象の位置検出を推進していくとともに,位置情報のデータ解析などを加えて異常の予兆検知や寿命予測などに繋げていきたい。
3.おわりに
ここまでアズビルのMEMS技術を使ったセンサについて述べてきた。今後もMEMSは図12に示す潮流のとおり,単純な量の計測から質の計測への転換, AIとの融合やDXとの相乗効果,オートメーションにおける自律化やモノからコト売りといった進化で,確実にその応用範囲を広げていく。こういった状況の中で,当社のコアコンピタンスである計測と制御において,MEMSは計測デバイス,フィールド機器の核として,MEMS技術のさらなる深耕を推進するとともに,新たな挑戦からその柱となる技術を増やし,SDGsを道標として持続可能な社会へ「直列」に繋がる貢献を目指していく。
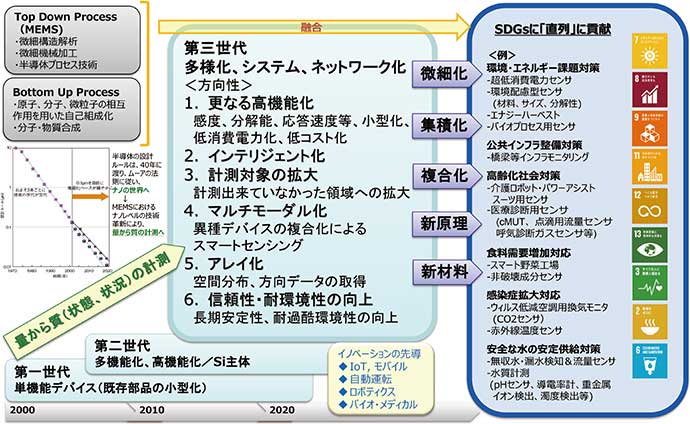
図12 MEMSの潮流
<参考文献>
(1) 池信一ほか:微少流量向け熱式流量センサの開発,azbil Technical Review 2011年1月号
(2) C.S.Smith:Phys. Rev. Vol.94, No.1, p42-49, 1954
(3) O.N.Tufte, P.W.Chapman,D. Long : J. Appl. Phys. Vol.33, No.11, p3322-3327, 1962
(4)五十嵐伊勢美:自動車技術, 18(9), p706, 1964
(5) 米田雅之:ピエゾ抵抗式圧力センサの最適設計, Savemation Review, 2000年8月号
(6) 末高聡:CNGディスペンサ用流量計向けマルチバリア ブル圧力センサの開発, Savemation Review, 2002年8月号
(7) 徳田智久:世界最高水準の精度と安定性を有するピエゾ抵抗式圧力センサの開発, azbil Technical Review, 2009年12月号
(8) 関根正志ほか:サファイア高温隔膜真空計のセンサ素 子・パッケージ開発,azbil Technical Review 2011年1月号
(9 )Hojun Kangほか:“Experimental and computational study on aluminum oxide surfaces exposed to halogen containing plasmas” [PO16PM-071], XXXIV International Conference on Phenomena in Ionized Gases.
10th International Conference on Reactive Plasmas,(Center for Atomic and Molecular Technologies, Osaka University, Azbil Corporation)
(10)石原卓也ほか:原子層堆積法向けサファイア隔膜真空計の開発,azbil Technical Review, 2014年4月号
<商標>
マイクロフローセンサ,DSTJ,SuperAce,Bravolight, AIRcube,STEAMcube,GasCVDはアズビル株式会社の商標です。
InconelはSpecial Metals Corporationの商品名であり,商標です。
<著者所属>
図師 信彦 アズビル株式会社 技術開発本部マイクロデバイス部
米田 雅之 アズビル株式会社 技術開発本部マイクロデバイス部
この記事は、技術報告書「azbil Technical Review」の2023年04月に掲載されたものです。
- 2025
- 2024
- 2023
- 巻頭言:センサなどの製作に用いられる半導体微細加工技術 MEMS
- 特集に寄せて
- アズビルMEMSの歴史と今後の展望
- 小型化,プロセス耐性を高めた サファイアリニューアル真空計の開発
- MEMS技術を駆使して過大圧保護機構を集積化した 超高耐圧差圧センサの開発
- オイルフリー高感度圧力センサの開発と応用検討
- ユーザビリティを向上させた マスフローコントローラの開発
- MEMSセンサの能力を最大限に発揮させる センサパッケージング技術
- 新クリーンルームの設計コンセプト ─ 独創的MEMSセンサの効率的な市場導入促進に向けて
- savic-netTM FX/G5におけるサイバーセキュリティ対応
- 個別快適ニーズに対応するための空調ゾーン細分化技術
- クラウドMESを活用した生産現場における IT基盤の構築とDX推進
- Pharmanag™ Ⅴ 顧客固有の業務プロセスのシステム化を容易にする医薬向けMESの開発
- マルチエリア対応ユーザターミナル(QJ-1201)
- 2022
- 2021
- 2020
- 2019
- 2018
- 2017
- 2016
- 2015
- 2014
- 2013
- 2012
- 2011
- 2009
- 2008
- 2007
- 2006