小型化,プロセス耐性を高めたサファイアリニューアル真空計の開発
キーワード:静電容量式圧力センサ,MEMS,サファイア,半導体製造プロセス,キャパシタンスマノメータ
半導体製造プロセス用に開発された先行モデルである静電容量式真空計(形 SPG□□)を抜本的に改良した新たな真空計を開発した。センサチップおよび周辺のパッケージ構造も抜本的に変えて小型化および低容積化,高耐圧化を実現するとともに特殊なダイアフラムの構造により耐デポ性能も著しく改善した。さらにセンサ部と計測回路を分離する構造により動作可能温度を従来の200℃から250℃まで上げ,日々進歩が著しい半導体製造プロセスの様々な客先ニーズに対応できるようになった。
1.はじめに
半導体製造プロセスの成膜,エッチングプロセスにはガス依存性がない全圧真空計である静電容量式の圧力センサ,いわゆるキャパシタンスマノメーターがその圧力監視および制御に一般的に用いられている。このプロセスで使用されるガスはハロゲン系のガスのように反応性に富み,腐食性をもつものが多く,センサの構成材料は耐食性があるものが必要である。また,副生成物の真空計内部への付着を防ぐために100℃~200℃に加熱された状態で用いられることが多く,計測圧力レンジは13Paフルスケールの極微圧から大気圧付近の133kPaまでと幅広い。
アズビルではガスの種類,動作温度範囲,レンジ範囲,それぞれ幅広く対応が必要な半導体製造プロセスに適用すべく,耐食性・耐熱性に優れたサファイアを基材としたMEMSセンサチップを搭載したサファイア隔膜真空計,形 SPG□□(以下, 形 SPG)を開発した(1)-(7)。図1に形 SPGの外観を示す。市場に投入してから10年以上がたち,客先で発生する様々な課題が明らかになってきた。特にプロセス副生成物のセンサ内部,具体的には感圧ダイフラム上への堆積による出力への影響をいかに抑制するかが大きな課題となっており,形 SPGでも様々な改良をセンサ構造に施してきた(3)(7)。また,お客さまと対話していく中でより小型で場所をとらないものや真空計の内部容積を小さくして応答速度を早くしたもの,さらには次世代向けの材料に対応するため,より高温で動作するものが求められていることが分かってきた。このような要求を満たし従来の形 SPGのセンサ構造を流用するには, 構造や大きさに限界があるため,センサチップの構造からパッケージ,さらには計測回路まで抜本的に見直した新たなサファイア隔膜真空計 形 V8 (以下,形 V8)の開発に着手した。
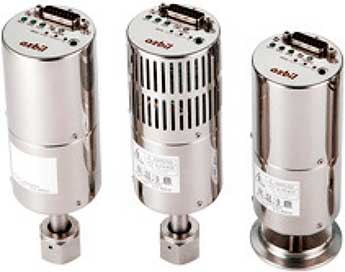
図1 形 SPGの外観図
2.圧力センサ概要
2章では形 V8のセンサチップおよびパッケージの構造を形 SPGと比較し、その特長を説明する。
2.1 センサチップ構造
センサチップは基本的に形 SPGの構造(1)(4)を流用しており,センサの動作原理は図2のようにダイアフラムとよばれる薄板の撓(たわみ)による静電容量の変化を出力として感知するものである。基本的にこの圧力を受けて撓むダイアフラムの測定媒体側の反対側に設置したキャビティといわれる空孔の上下にコンデンサーを形成する電極を配置し,信号は裏面から取り出す構造である。
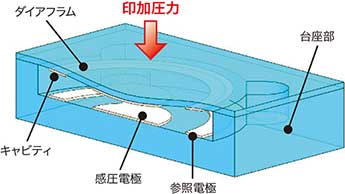
図2 センサ動作原理
図3に示すように,形 SPGから形 V8への改良で大幅に変更したのはセンサチップの外形が単純な正方形ではなく,角部にR形状をつけたことである。これにより過大圧印加時にパッケージの金属板(図4)への負荷を減らし,破壊圧力を従来の1.5MPaから3MPa以上と2倍まで向上させることができた。特にプロセスチャンバーのガスの供給側に設置される真空計にはこのような高い破壊耐圧が要求される。
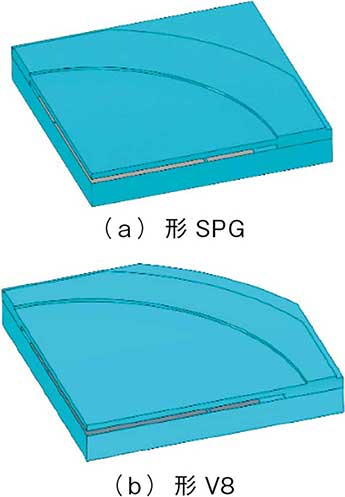
図3 センサチップの形状比較
2.2 1stパッケージ
1stパッケージはセンサ素子を金属筐体に橋渡しするための部材である金属薄板にセンサ素子を接合し,裏面の電極取り出しを行う工程である。サファイアの線膨張係数7~8 ×10^(-6)1/Kは筐体材料であるニッケル基耐食合金の12~14×10^(-6) 1/Kと比べると大きな乖離があり,サファイアのセンサチップをこのような金属に接合するとセンサの温度特性,温度ヒステリシスなどに大きな悪影響を及ぼすだけでなく,接合材として接着剤やロウ材,低融点ガラスなどを用いるとセンサ全体の耐食性を損なうことになる。形 SPGでは直接センサチップを金属に接合することを避け,カバーサファイアといわれる一種の干渉材を間に挟むことにより上記特性の悪化を防いだ。また,金属とサファイアの接合には介在物を必要としない熱拡散接合法を採用した。この接合方法は2枚のサファイアに金属薄板を挟む構造で接合することにより,接合で生じる熱応力のバランスをとるものである(1)。今回形 V8ではこのカバーサファイアを使用せずにセンサチップ同様ウエハから製作したバランスサファイアという部材とセンサチップでニッケル基合金の薄板で挟むことによりパッケージすることを目指した。当然,線膨張係数の異なる材料を直接センサチップに接合するので何らかの対策を打たないと前述のように温度関係の特性は悪化することが予想される。
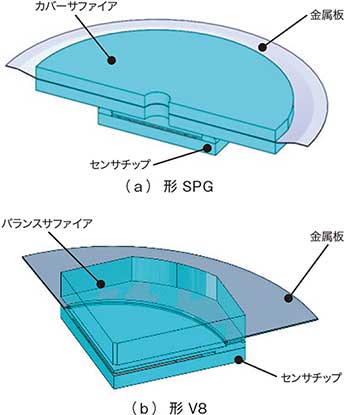
図4 1stパッケージの構造比較
各種シミュレーションを行った結果,接合部の内径をダイアフラムの可動部の径よりも大きくすることにより温度特性が改善されることが判明した。図5にその計算結果を示す。横軸に接合部の内径を,縦軸に温度を変化させたときの出力の変化をダイアフラム可動部の径と接合部の内径(φ7.5)が一致したときの値を100%としてプロットしたものである。
いずれのレンジのセンサにおいてもセンサの接合部内径を広げることによりこのような異種材料間の接合による影響を抑制することができることが分かる。これは異種材料接合に起因する変形の中立面にダイアフラムを配置することで全体が変形してもダイアフラムが変形しないという原理に基づいている。
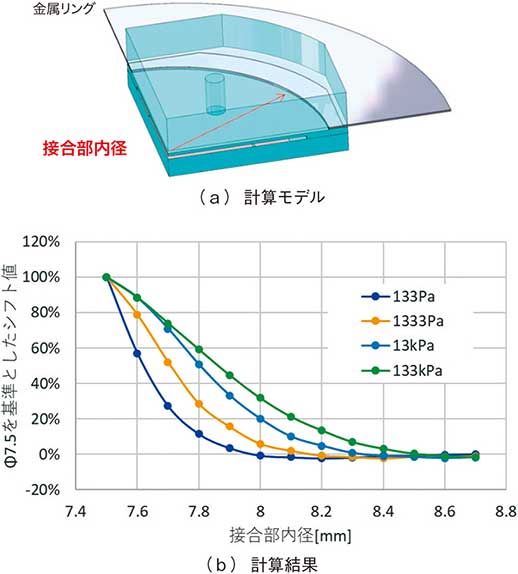
図5 温度特性のシミュレーション結果
また,実際の1333Paレンジセンサの温度特性を図6に示す。45~200℃の温度特性はφ7.5のものに比べてφ8.1まで拡張したものは1/100以下に改善されている。
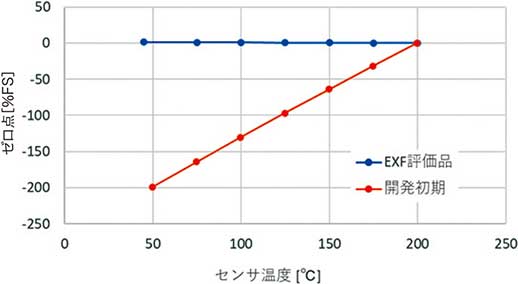
図6 温度特性
併せてセンサチップのところで説明した耐圧のシミュレーション結果を図7に示す。ここではセンサに1MPa印加したときの各部位の応力を材料非線形モデルで計算し,使用した金属板の破壊応力である540MPaに達するかどうかを検討した。四角いチップの場合,角部が金属板に接触する箇所で最大応力を生じ,約0.8MPa印加したときに破壊応力に達する。これに対し,Rをつけた場合は1MPa印加しても応力は497MPaで破壊応力には達しないという結果になり,耐圧を向上させることができることが分かる。
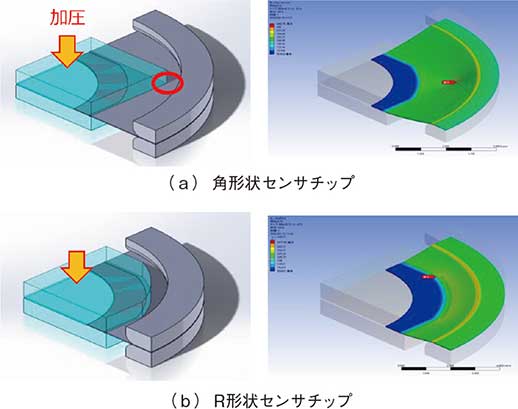
図7 過大圧印加シミュレーション結果
このように各種特性を維持しながらカバーサファイアをなくした1stパッケージを実現することによりセンサ全体の大きさを小さくするとともに圧力応答に大きな影響を与えるセンサ内部容量も大幅に減らすことが可能となった。
2.3 2ndパッケージ
2ndパッケージは1stパッケージを信号の取り出しを行うガラスハーメチックシール部や堆積防止用のバッフルとともに金属筐体に溶接し,最後に真空封止を行う工程である。真空封止後にはアクチベートされた活性金属からなるゲッター材料が,真空基準となるリファレンス室の真空度を超高真空(~ ×10-10Pa)に維持し,絶対圧を計測できるようになる。ここも形 SPGとは基本コンセプトを変えず,ダウンサイジングした1stパッケージに合わせて筐体設計を行った。図8に形 SPGの構造と形 V8の構造を比較したものを示す。大きな変更点は形 SPGで設けたハーメチックシールの信号線のシールド部をなくしたところである。容量計測は外部の電気ノイズに敏感であるので信号線はシールドする必要があるが各種試験の結果,ハーメチックシール部にはなくてもノイズ耐性上問題がないことが分かったので構造を簡略化することとした。

図8 形 SPGと形 V8の2ndパッケージ構造比較
2.4 製品パッケージ
2ndパッケージ以降,製品完成までの工程である製品パッケージは用途によって構造および工程が変わってくる。製品をプロセスチャンバーに取り付ける継手部の形状はもちろんのこと,今回形 V8の開発にあたっては計測回路を分離した分離型モデル(図9b)も新たに開発した。このモデルは一体型モデル(図9a)とは異なり,自己加熱ヒーターをもたず,装置側の配管と一体で加熱することになる。一体型では回路がセンサの近傍にあるため200℃以上に上げることはできないが,このモデルでは250℃までの加熱が可能である。このようなセンサが必要とされるのはプロセスチャンバー本体ではなく,ガス供給側のラインである。近年ALD(Atomic Layer Deposition)という成膜プロセスで様々な液体材料や固体材料を気化,あるいは昇華させてチャンバー側に供給する必要があるため,より高温で動作する圧力センサや流量計,バルブのニーズが高まっているということが背景にある。
製品のパッケージが完了したら次は組み込んだ計測回路でセンサのキャラクタリゼーションを実施し,特性検査を行って出荷することとなる。計測回路も大幅に見直し,応答速度を上げるなどの改良を実施した。
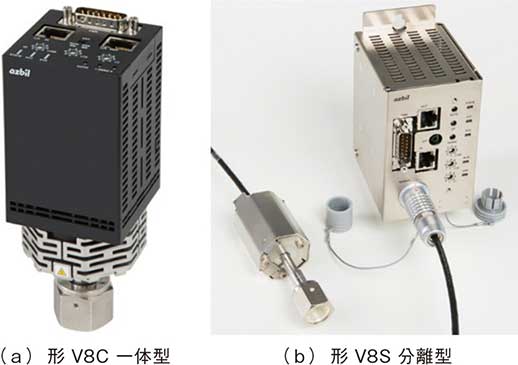
図9 分離型と一体型
3.センサ特性
この3章では1000Paレンジセンサの特性の評価結果の代表的なものを示す。
図10は複数のセンサの圧力感度を示したもので縦軸が容量値変化,横軸が印加圧力である。センサの製造公差から規定した規格値に収まっていることが分かる。
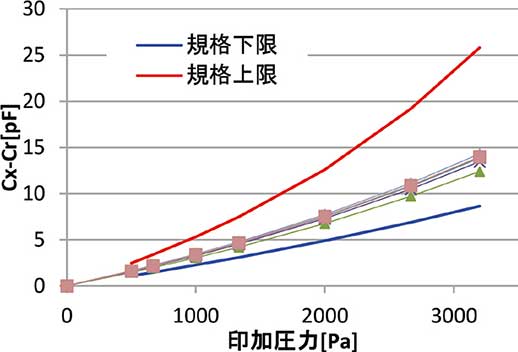
図10 圧力特性
図11はサーマルヒステリシスの測定結果でセンサ温度を150℃から一旦230℃に上げ,もう一度150℃に下げたときのおよびスパン点のずれを示したものである。スパン点は圧力を印加したときの出力から圧力ゼロのときの出力の差分である。
ゼロ点は0.5%フルスケール以下,スパン点はほとんどずれない結果となり,広範囲に温度を振っても特性は安定している。
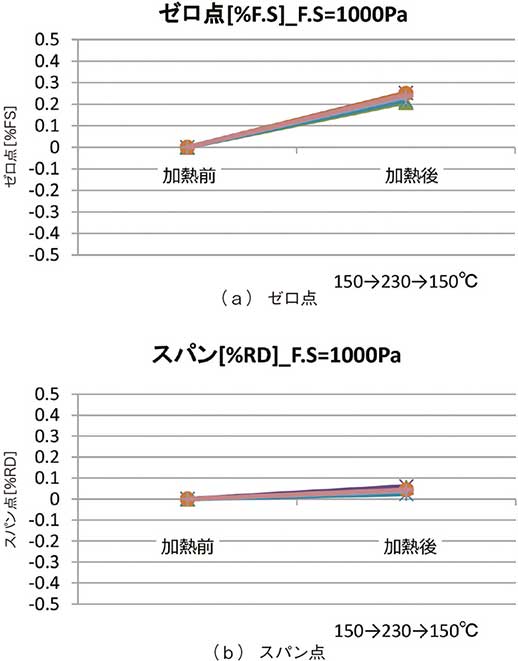
図11 サーマルヒステリシス
図12はゼロ点の230℃における長期出力変動を評価したものである。180時間後も0.1%フルスケール以下で推移しており,極めて安定している。
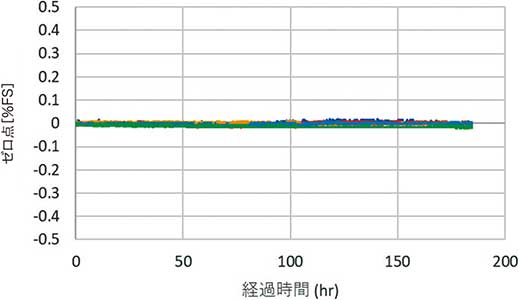
図12 230℃ゼロ点ドリフト
図13は-20℃と80℃間の気相熱衝撃試験の結果を示したものである。ゼロ点は0.1%フルスケール,スパン点は0.02%RDであり,試験前後で大きな動きはない。
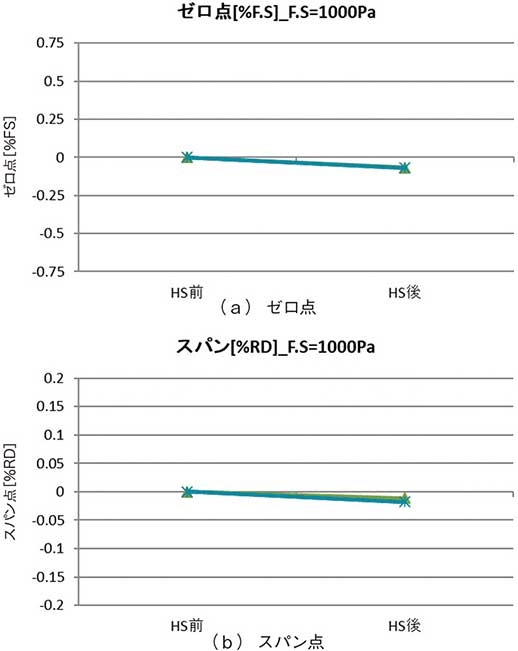
図13 気相熱衝撃試験
図14は許容圧力印加試験で,230℃で300kPaを250回印加後にゼロ点とスパン点の変化を示している。いずれも大きな変化はなく,チャンバー大気開放などの過大圧印加後も特性に大きな変化がないことが分かる。
これらの結果は今回開発した形 V8センサの特性が非常に優れたものであることを示している。
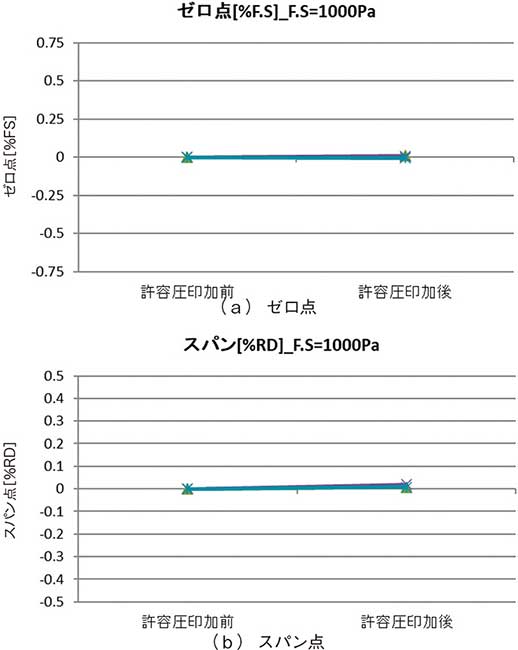
図14 許容圧印加試験
4.耐デポ性能
半導体製造プロセスに使用される真空計は内部にプロセス副生成物が堆積することがあり,これが原因でゼロ点のシフトが発生するため装置を止めてゼロ点の調整を行ったりセンサを交換したりする必要が生じる。これをいかに防ぐかが「耐デポ性能」であり,装置メーカーに採用されるかどうかの最も大きな判断基準であるといえる。実際,センサを加熱するだけではこの問題を防ぐことができず,形 SPGでは様々な対策を実施したがプロセスそのものが副生性物を発生させ易いALDのようなものが主流になってきたり,ウエハのスループットを上げるためにガスの供給量を増やし,副生成物の量が増えたりしたことなどもあって不十分なものにとどまっていた。その代表的なものの挙動を図15示す。これはCVD(Chemical Vapor Deposition)のプロセスで使用したあとの1333Paセンサを社内で再評価したものでありゼロ点が13Paシフトしているだけでなく,加熱や圧力印加に伴ってシフトやドリフトが生じるのが特徴である。この様な挙動を示しているということは何等かの粘性をもった材料がダイアフラム上に残存していることを意味しており,対策が必須である。
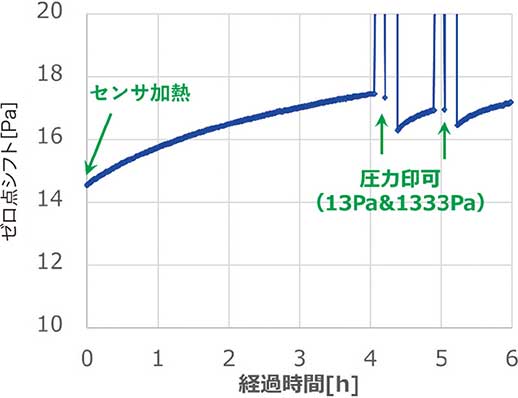
図15 CVDプロセス後のセンサ挙動
4.1 形 V8のデポ対策の基本コンセプト
形 V8の開発にあたってはこのようなデポが起きてもゼロ点のシフトなどを起こさない,ある程度汎用性がある対策を講じることとした。その原理は堆積した膜を物理的に分断することができれば各個で応力が発生しても全体ではダイアフラムを撓ませるモーメントを生じることはない,というものである。図16にその原理をシミュレーションで検証した結果を示す。モデルは一次元の梁の上に堆積物を設置し,それに応力を与えて梁を撓ませたものである。膜にはスリットを入れて分断し,その効果を確認した。この計算結果では膜を200個に分断すれば分断しない場合に比べて梁の最大撓みは1/10程度まで減らすことができることが示されている。
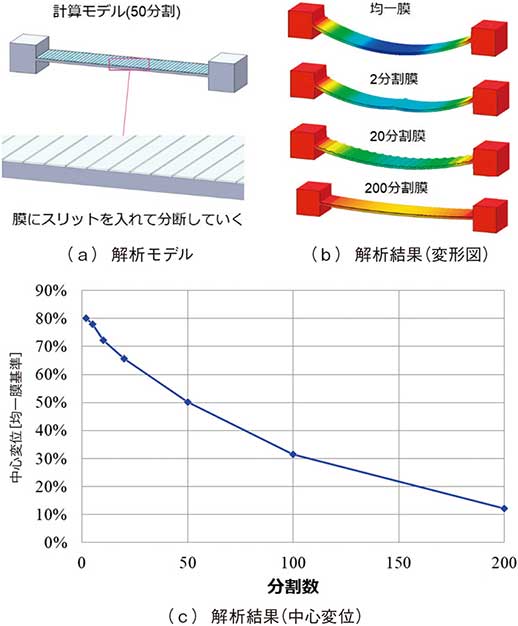
図16 1次元モデルによる堆積膜の分断効果シミュレーション
さらに実際の形状に近い3次元の円板モデルで計算した結果を図17に示す。膜を分断したモデルの変位は,しないものに比べて1/12になることが分かる。
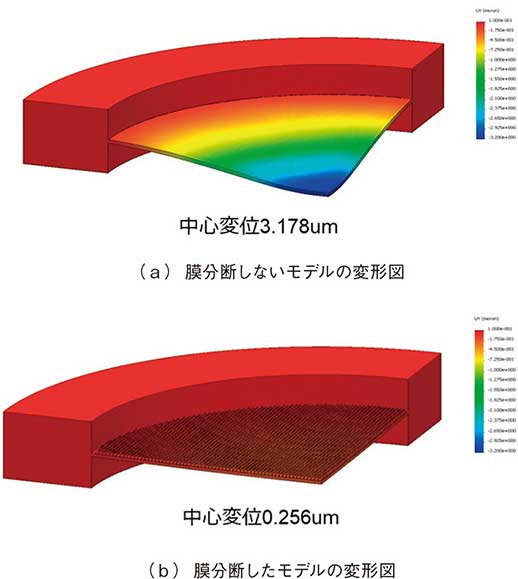
図17 3次元モデルによる堆積膜の分断効果シミュレーション
以上の結果からシミュレーション上はセンサダイアフラム上に堆積膜が形成されても,その膜が細かく分断されていればダイアフラムへの応力影響を抑制することができる。
4.2 デポ対策の凹凸ダイアフラム
次はいかにして膜を分断する構造を実現するかである。今回はMEMS加工技術を活用してセンサダイアフラム上に微細な溝を形成し,成膜時のガスの侵入しやすさに差異を設けることで堆積膜が分断されることを狙うこととした。成膜プロセス中のガスの平均自由工程,すなわち他のガス分子と衝突せずにガスが飛行できる距離は温度,圧力から計算するとおおよそ50um程度である。これよりも狭い空間にガス分子が侵入する確率は急激に下がる。その結果,堆積する膜の量は溝の外と中で差異ができ,このことを分断に利用する。具体的にダイアフラム表面に加工した構造を図18に示す。
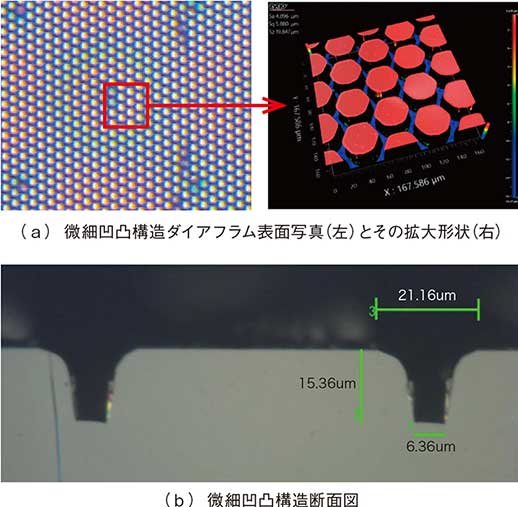
図18 微細凹凸構造
さらに希薄流体シミュレーション(DSMC:Direct Simulation Monte Carlo)を用いて堆積のシミュレーションを行った結果を図19に示す。溝の外と底でおよそ3:1の吸着量の差が発生しており,この溝をハニカム状に配置した構造が分断に寄与することが分かる。
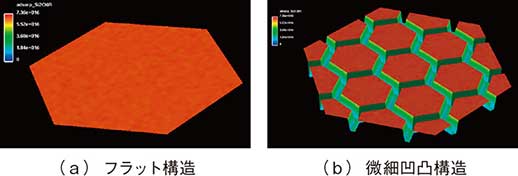
図19 DSMCによる堆積シミュレーション
4.3 デポ対策の効果
最後に凹凸ダイアフラムによる耐デポ効果を実験で実証した効果を下記に示す。図20は熱CVDによるSiO2セスの後段に単純なフラットなダイアフラムチップと微細凹凸ダイアフラムチップをそれぞれ搭載した真空計を配置し,プロセス前後でゼロ点を連続的に計測したものである。レンジは1333Paでそれに対してシフト値はフラットチップで0.3Pa程度と小さいが明確な差異が確認された。
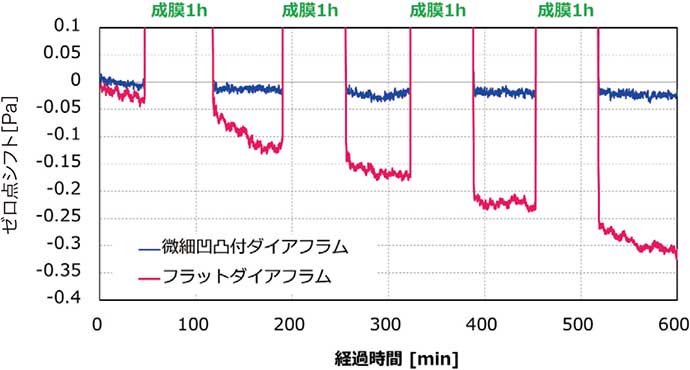
図20 SiO2のゼロ点挙動比較-CVDプロセス後のゼロ点挙動比較
次に図21にポリシリコンCVD成膜プロセス後のセンサ挙動をフラットなダイアフラムチップと微細凹凸ダイアフラムチップで比較した結果を示す。
図から明らかなようにポリシリコンではSiO2の場合と異なり,微細凹凸チップでは大幅に改善されていることが明らかになった。まずフラットチップでは14.5Pa(1%強に相当)のゼロ点シフトが発生しさらに加熱後のドリフトや圧力印加後にシフトが起きていることが分かる。これに対し,微細凹凸チップではゼロ点シフトは1.4Pa(0.1%に相当)にとどまり,さらに加熱後や圧力印加後は直ちに0に復帰し,フラットチップで見られたようなドリフトやシフトは起きない。この2つのセンサは同時に成膜評価を実施しているので相対的ではあるが明確な耐デポ効果が確認された。
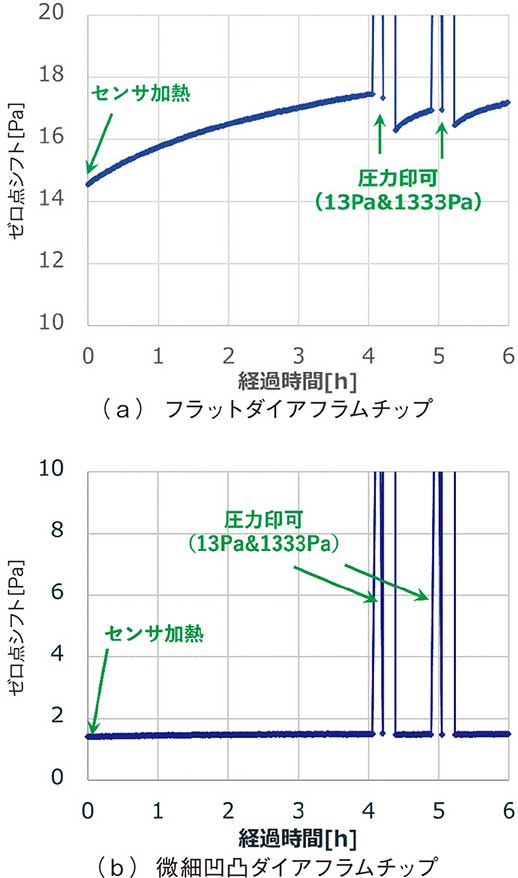
図21 ポリシリコン-CVDプロセス後のゼロ点挙動比較
5.おわりに
デバイスの微細化や3次元化に伴い,半導体製造プロセスで用いられる工法や材料が日々進歩しており,その圧力制御に用いる真空計に対しても求められる機能が拡大していく傾向にある。特に耐デポ性能はエンドユーザーの装置稼働状況に直接影響を与える重要な特性であり,今回評価したSiO2やポリシリコンのCVDだけでなく,プラズマプロセスなど幅広く対応していく必要がある。今後はこの形 V8を基盤として顧客ニーズを取り込み,随時機能を強化したモデルを開発・リリースしていく予定である。
<参考文献>
(1) 関根,差波,石原,谷:サファイア高温隔膜真空計のセンサ素子・パッケージ開発,azbil Technical Review, 2011
(2) 吉川,原田,市原,長田,山口:サファイア高温隔膜真 空計の開発,azbil Technical Review, 2011
(3) 石原,関根,栃木:原子層堆積法向けサファイア隔膜 真空計の開発,azbil Technical Review, 2014
(4) 石原,長田:高温型サファイア隔膜真空計の開発,第 23回センシングフォーラム, 2006, pp.130-135
(5) S. Kimura, Y. Ishikura, T. Kataoka, M. SoedaT. Masuda, Y. Yoshikawa, M. Nagata:Stable and Corrosion-Resistant Sapphire Capacitive Pressure Sensor for High Temperature and Harsh Environments, Transducers’01,2001,pp. 518-521
(6) M. Soeda, T. Kataoka, Y. Ishikura, S. Kimura, Y. Yoshikawa, M. Nagata:Sapphire-Based Capacitive Pressure Sensor for High Temperature and Harsh Environments Application,2002, Proceedings of the IEEE Sensors 2002 conference,pp.950-953
(7) 栃木:原子層堆積法向けサファイア隔膜真空計の開発,第30回センシングフォーラム, 2013, pp.125-130
<著者所属>
石原 卓也 アズビル株式会社 技術開発本部マイクロデバイス部
この記事は、技術報告書「azbil Technical Review」の2023年04月に掲載されたものです。
- 2025
- 2024
- 2023
- 巻頭言:センサなどの製作に用いられる半導体微細加工技術 MEMS
- 特集に寄せて
- アズビルMEMSの歴史と今後の展望
- 小型化,プロセス耐性を高めた サファイアリニューアル真空計の開発
- MEMS技術を駆使して過大圧保護機構を集積化した 超高耐圧差圧センサの開発
- オイルフリー高感度圧力センサの開発と応用検討
- ユーザビリティを向上させた マスフローコントローラの開発
- MEMSセンサの能力を最大限に発揮させる センサパッケージング技術
- 新クリーンルームの設計コンセプト ─ 独創的MEMSセンサの効率的な市場導入促進に向けて
- savic-netTM FX/G5におけるサイバーセキュリティ対応
- 個別快適ニーズに対応するための空調ゾーン細分化技術
- クラウドMESを活用した生産現場における IT基盤の構築とDX推進
- Pharmanag™ Ⅴ 顧客固有の業務プロセスのシステム化を容易にする医薬向けMESの開発
- マルチエリア対応ユーザターミナル(QJ-1201)
- 2022
- 2021
- 2020
- 2019
- 2018
- 2017
- 2016
- 2015
- 2014
- 2013
- 2012
- 2011
- 2009
- 2008
- 2007
- 2006