予兆検知・診断技術の開発
製造装置における製造ロス削減と省エネの取組み
キーワード:異常検知,予兆検知,状態基準保全,カーネル密度推定
製造装置を用いたプロセスでは,装置の異常に伴い製造ロスやエネルギーロスが発生する。製造装置の多くは自動化されており,同種の製造物に対する装置動作は繰り返し再現性があり,製造時の物理量を計測・比較することで装置動作の変化を可視化できる。これを利用して異常の発生や予兆を検知し,TBMからCBMへ移行することで,ロスを削減できる。今回開発した予兆検知・診断技術では,繰り返し再現性のある製造プロセスにおいて,基準データをもとに,異常やその予兆を検知する。そこで本稿では,この異常の予兆検知・診断技術の概要と,その有効性確認のために行った実証実験について述べる。
1.はじめに
持続可能な社会の実現に向けてカーボンニュートラルへの取組みは社会全体で求められている。ファクトリーオートメーションにおいても,その実現に向けて製造ロス削減やエネルギーロス削減への関心は高まっている。
近年使用されている製造装置の多くは自動化されており,同種の製造物を繰り返し製造する。これらの製造装置は長期にわたって運用され,安定した操業を維持するためには製造装置を保守点検し管理する必要がある。
従来,製造装置の管理はTBM(Time Based Maintenance:時間基準保全)が主流とされていた。これは,あらかじめ規定回数や規定時間を設定し,その周期に合わせて点検する手法である。この保全により,製造装置の異常についてある程度の抑制が可能である。しかし,製造物や製造装置には個体差があり,異常が発生するまでの回数や時間にはばらつきがある。規定回数や規定時間が, 異常が発生する回数や時間に対して短すぎる場合,過剰な対応を行ってしまう可能性が高くなる。一方,規定回数や規定時間が長すぎる場合,異常な状態で製造を行ってしまう可能性がある。これらを見極めて適切な規定回数や規定時間を決めるのは難しい。
そこで近年では,CBM(Condition Based Maintenance:状態基準保全)と呼ばれる手法が取り入られ始めている。この保全は,製造装置を特定の手法を用いてロットごとに状態を診断し,異常があれば対応するものである。これにより,TBMで発生していた規定期間内の異常に対応できるほか,過剰な対応を削減できるため,製造ロスや製造品の手直し,追加生産によるエネルギーロスを削減できる。
本稿では,繰り返し再現性のある製造プロセスにおける異常の予兆検知・診断技術の概要と,実証実験による有効性の確認結果を述べる。
2.課題
製造装置におけるCBMの手法の1つとして,センサ等を用いて装置内異常を自動検出する手法がある。これは,ロットごとに製造装置の異常検査を行い,異常があれば装置内の故障箇所を修繕する手法である。なお本稿では同じ条件で製造される製造物の製造数量の最小単位をロット,1つの製造物を製造するための製造プロセスをサイクルと表現する。これにより,もし装置が異常な状態で製造を行っても,その直後の検査により異常が発覚するため,製造品のロスは1つで抑えることができる。一方,ロットごとに装置の検査を行うためタクトタイムが長くなり,生産性が低下してしまう欠点が存在する。
この欠点を回避するために,製造中の動作を計測して装置内の劣化する箇所の状態を推定する手法が注目されている。状態推定に使用されるパラメータは多種にわたり,装置内の画像を撮影し異常を検知するものや,製造時の動作音から装置状態を推定するものなどが存在する。これらは適切な学習をすることにより,通常時との違いを検知でき,異常状態による製造を低減することができる。しかし,光や音などは測定条件に制約があるなど,利用にあたって高い障壁がある。
また,繰り返し再現性のある製造プロセスは同種の製造物に対するサイクルのみで,製造物が異なれば装置の動作は異なる。状態推定を行う前段階で,計測した物理量が同種の製造物に対するものかを識別する必要がある。
そこで今回開発した予兆検知・診断技術では,製造にともなって変化する物理量のうち,光や音などに比べて測定条件の制約が少ない電流や電圧といった電気信号を対象とし,その信号の推移を品種ごとに検査し異常を検知することを目指した。
3.診断対象・計測方法
繰り返し再現性のある製造装置の一例として,今回は旋削加工を行う工作機械を診断の対象とした。工作機械へ適用した予兆検知・診断技術のシステム構成例を図1に示す。工作機械内部のサーボアンプから加工用モータに接続されている三相電流ケーブルのいずれかに電流センサを設置し,電流値を計測する。計測した電流値情報をもとに,工作機械の加工用モータの負荷を推定する。工作機械がモータを低負荷で回転させる場合には機差が存在するが10 A弱の電流が流れ,高負荷で回転する場合には10 A~100 A程度の電流が流れるため,電流を計測することで加工用モータの負荷を推定できる。
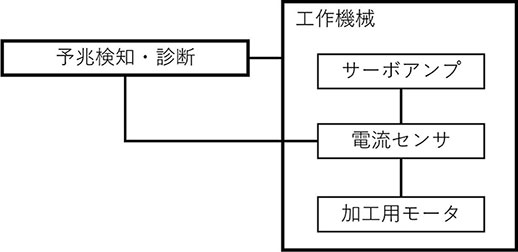
図1 システム構成例
今回は,1サイクル中に得られた加工用モータの負荷状況を複数回分取得し,正常時の基準データを生成する。基準データとして用いるサイクルの数は装置や製造工程に応じて異なるため,装置ごとに適切な回数に調整する。装置のこの基準データと現在の加工データを比較し,工具異常の予兆検知・診断を行う。
4.異常の予兆検知・診断
今回開発した異常の予兆検知・診断技術は,基準データ作成ステップと検査ステップに分かれている。検査を行うには,製造する品種ごとの基準データが必要となるため,新品種を加工する場合や設計,加工条件が変更になった場合は,新たにモータ電流値を計測し,基準データを生成する必要がある。
4.1 基準データ作成
基準データ作成は,使用者が今後加工する予定である任意の品種について行う。
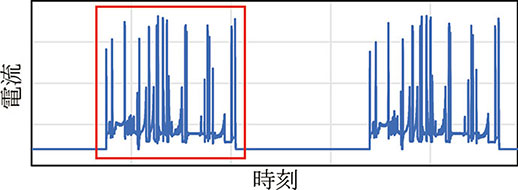
図2 電流値の取得例とサイクルの切出し
まず初めに,図2のようにセンサから得られる連続の電流値をサイクルごとに切り分ける。切分けでは,取得した電流値が一定時間以上0でなかった部分をサイクルとする。
1サイクル切出しの完了後,オフセット補正とジッタ補正を行う。オフセット補正は,図3-aのようにサイクルごとに電流が異なる場合があるため,オフセット補正することで図3-bのようにサイクルによらない波形を取得でき,異常波形の検出を容易にする補正である。一方ジッタ補正とは,各工程のタイミングのずれを調整する補正である。図4-aのように同一品種の加工であっても外部要因により生じるサイクル内の各工程のずれを,1回目に取得したサイクルを基準として,図4-bのように補正する。これにより,加工タイミングのずれなどによる誤検知を低減することができる。
その後,オフセット補正とジッタ補正済みのサイクルの電流データについて規定回数分の取込みを行う。取込みが完了すると,サイクル内の加工区間の推定を行う。加工区間とは,サイクルのうち実際に加工が行われている区間,つまり工具が使用されている区間のことである。加工区間のみを診断の対象とすることで,工具の状態を精度よく推定することができる。材料の加工時には工作機械のモータの負荷電流が変動することを利用して加工が実施されていると予想される区間を検出する。図5に,サイクルの加工区間切出し例を示す。
以上の工程により得られたデータを基準データとして記憶する。
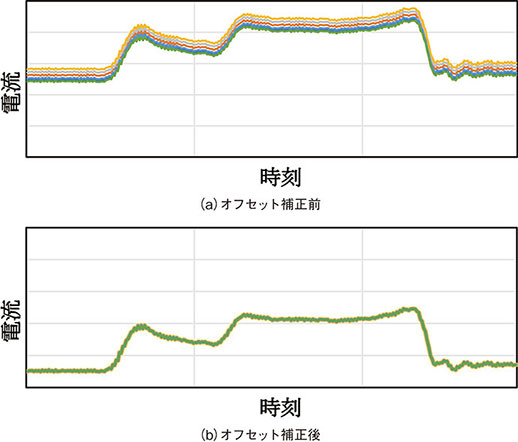
図3 オフセット補正による電流の変化
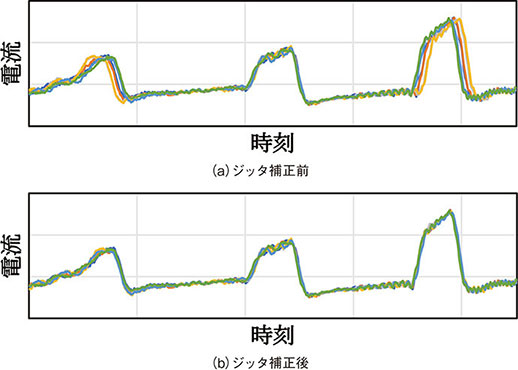
図4 ジッタ補正による電流の変化
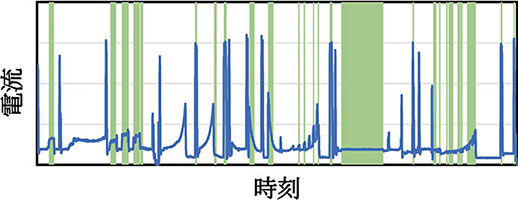
図5 加工区間切出し例
4.2 検査
検査は,実際に加工する際に得られた電流波形を検査データとして,基準データ作成で得られたデータを参照し,その乖離度によって異常か否かの判定を行う。検査工程は主に,サイクル切出し,品種判別,オフセット補正,ジッタ補正,カーネル密度推定量の算出,スコアの算出,診断結果の出力の工程から成り立っている。
サイクルの切出しは基準データ作成時と同じアルゴリズムを利用する。その後,切り出された電流波形を参照し,加工された品種を判定する。品種の判定では,電流波形の形状を,生成済の基準データと照合して一番近いものを,当該の加工品種と判別する。なお,工作機械から信号入力により品種情報を得ている場合はこれを優先する。また,品種の自動判別機能を利用せず,使用者の判断で加工品種を設定することも可能である。
品種判別完了後,その品種の基準データを参照してオフセット補正とジッタ補正を行う。なお,補正手法は基準データ作成時と同じである。補正により成形された電流波形の出力後,KDE(Kernel Density Estimation:カーネル密度推定)を用いた異常判定を行う。KDEを用いた異常判定はオンライン異常予兆検知システムBiG EYES™にも取り入れられている(2)。図6にKDEによる推定正常範囲を導き出した一例を示す。KDEにより,複数回の電流波形から正常範囲を推定し,サイクル内の一点一点でこの範囲との乖離度合をスコア化する。これにより,サイクル内の各タイミングにおいてスコアが算出される。図7にその一例を示す。図7-aに示す基準データ作成時の電流波形に対し,図7-bに示す検査時の電流波形は赤枠部分の波形が大きく異なっている。図7-cにおいて,図7-bで囲われた赤枠のうち,特に差異が大きい部分については,スコアがサイクル内のいずれのタイミングに比べて上昇していることが分かる。
上記で得られたサイクルのスコア推移と,基準データ作成時に推定した加工区間範囲を参照し,その加工における代表スコア値を決定する。この代表スコア値が,しきい値を超えた場合はなんらかの異常が発生したとして,使用者に通知する。
以上により,各加工で代表スコアが算出される。この代表スコアは,工具が新品なほど小さく,使用回数が増えるほど大きくなる。これは摩耗などにより工具状態が変化するためであり,この代表スコアの推移を観察することで,工具の異常だけでなく摩耗状態を推定することも可能である。
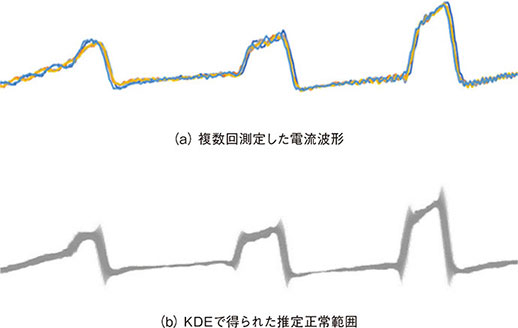
図6 測定した電流波形と得られた正常範囲
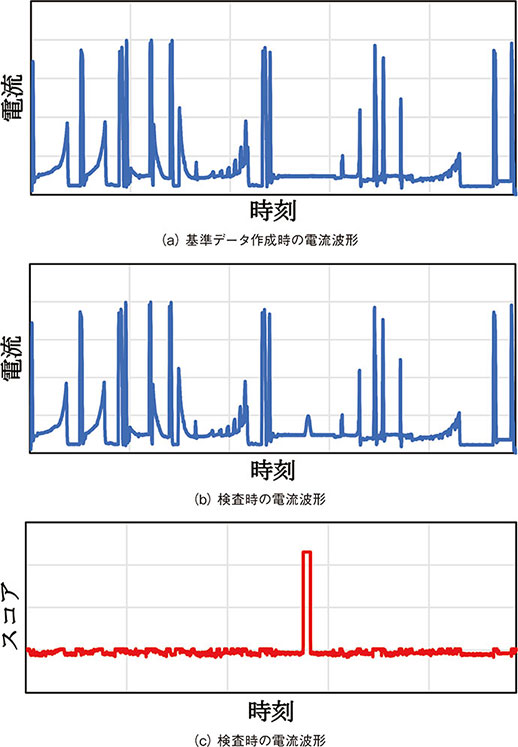
図7 電流波形とスコアの関係
5.検証
工具異常の予兆検知・診断機能の有効性確認のため,実験を行った。今回の検証では,一品種を加工し続ける工作機械の,加工用モータに接続されるサーボアンプのケーブル出力に電流センサを設置し,新品工具での加工を基準データとして取込んだ。その基準データをもとに検査を行い,適切な予兆検知が行われるかについて確認した。なお基準データ作成に用いるデータは工具を新品に変えた直後の15サイクルとし,品種判別は使用者による指定で行った。また,検査の対象は基準データ作成直後の加工から一定期間内に加工された全加工を対象とした。
6.実験結果
図8に今回対象とした品種を加工した際の基準データの電流推移を示す。切削負荷により電流が上昇している部分が加工区間と推定されたことが分かる。
この基準データをもとに,1818回の加工について検査を行った。図9に,基準データと異常と思われる加工(1385回目の加工)の電流波形を示す。基準データの波形と比較すると,赤枠部分の電流値が大きく異なっていることが分かる。
図10に示すサイクルのスコア推移を示す。1サイクル中のスコアは基準データ波形と異なるほど大きくなるため,特に赤枠部分の電流値が基準データと大きく異なっていたことが分かる。これをサイクルごとに算出し,それぞれについて代表スコアを決定した。
図11に,サイクルごとの代表スコアを示す。図11より,一定周期ごとに代表スコアが下がっていることが確認できる。これは,一定の加工回数ごとに工具を新品のものに交換しているため,基準データの電流波形に近くなるためである。また図9で取り上げた1385回目の加工で代表スコアが上昇していることが見て取れる。
以上より,工具の異常発生時や,工具の摩耗傾向が観察できることが確認できた。
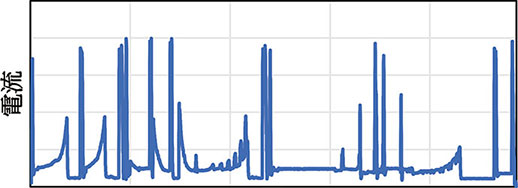
図8 取得した電流推移
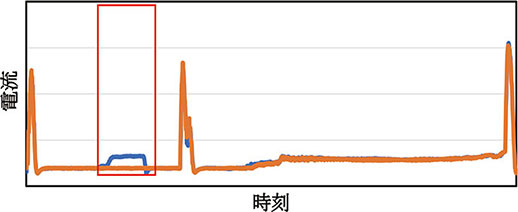
図9 正常時と1385回目の電流波形
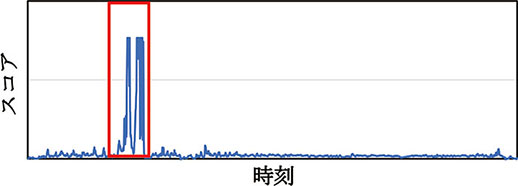
図10 サイクルのスコア推移例
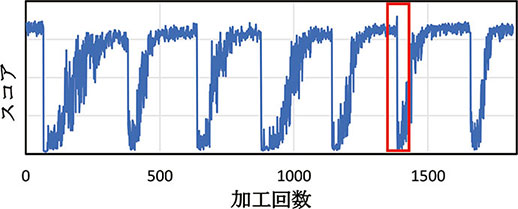
図11 サイクルごとの代表スコア
7.おわりに
繰り返し再現性のある製造装置の異常とその予兆を検知する技術を開発するにあたり,一例として,工作機械で使用している工具の状態を可視化し,工具の摩耗状態の推定や工具異常の検知について検証した。この技術により,現場の製造ロスやエネルギーロスの削減といった,市場の要求に大きく寄与できると考えている。
今後は,この手法をその他の事象に適用させ,様々な分野での予兆検知を行えるようにしたい。
<参考文献>
(1) 松村隆, 切削技術における動向と産学連携, 精密工学会誌, Vol.84, No.1, 2018, pp.33-37, 公益社団法人精密工学会
(2) 鈴木毅洋, 西口純也, オペレータの意思決定を支援するバッチプロセス向けオンライン異常予兆検知手法の開発, azbil Technical Review, 2018年, Vol.59, pp.14-20,アズビル株式会社
<商標>
BiG EYESはアズビル株式会社の商標です。
<著者所属>
丸野 智広 アズビル株式会社 アドバンスオートメーションカンパニー 戦略事業開発1部
西澤 慶祐 アズビル株式会社 アドバンスオートメーションカンパニー 戦略事業開発1部
保坂 儒人 アズビル株式会社 アドバンスオートメーションカンパニー 戦略事業開発1部
この記事は、技術報告書「azbil Technical Review」の2024年04月に掲載されたものです。
- 2025
- 2024
- 巻頭言:期待
- 特集に寄せて
- DR・VPPのためのリソース割当計画の自動作成
- 新技術を「試し」「議論し」「育てる」ための新実験棟
- 予兆検知・診断技術の開発
- オンライン異常予兆検知システムの大規模プラント向け拡張機能の開発
- 生成AIのアプリケーションへの導入に向けて
- オフィスのABW実装による効果検証法
- SUBLIME: Single-use battery-less wireless temperature sensor for lyophilization process
- 赤外線アレイセンサシステムの開発
- 生産性向上の実現に向けたIO-Link™対応誘導形近接センサ用ICの開発
- savic-net™G5コンパクトモデル
- 空間の価値を高めるsavic-net™ G5 入退室管理システム
- 小型デジタル指示調節計
- 2023
- 2022
- 2021
- 2020
- 2019
- 2018
- 2017
- 2016
- 2015
- 2014
- 2013
- 2012
- 2011
- 2009
- 2008
- 2007
- 2006