Mitsubishi Chemical Corporation, Ibaraki Plant
The Mitsubishi Chemical Ibaraki Plant, which produces a wide variety of petrochemical products in the Kashima Coastal Industrial Zone, has recently focused on control valves, which play an important role in production, in order to achieve reliable plant operation. The plant has selected a cloud service that analyzes and diagnoses the data on the condition of operating control valves that is detected by azbil Smart Valve Positioners, and has established a system to identify valve problems and warning signs in order to improve maintenance.
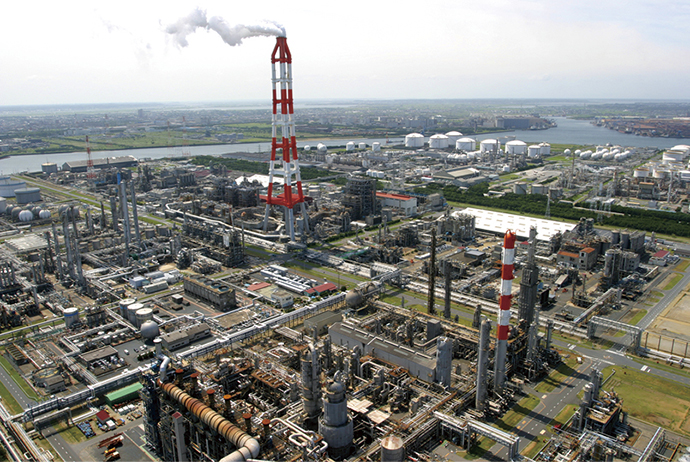
Factories and Plants Chemicals Safety & Dependability Reliable Operation Maintenance Support Cloud, IoT, and AI Control Valves and Actuators Life Cycle Support
Products/Services Provided
Optimal maintenance by monitoring the control valves on which plant operations depend
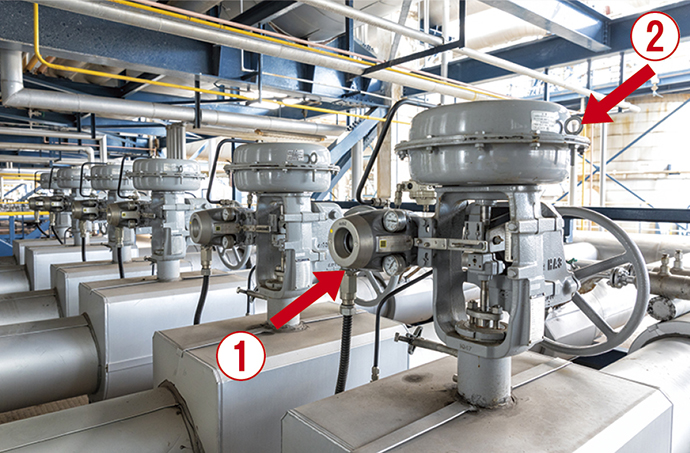
Pressure-balanced cage type control valve equipped with ②700 Series Smart Valve Positioner. The valve controls the flow rate of steam that is supplied with the raw materials for petrochemical products.
Located within 80 km from Tokyo, Kashima Coastal Industrial Zone boasts a vast area of 28.77 million square meters around Kashima Port. It is one of the largest production zones in Japan, with factories for petroleum refining, petrochemicals, electric power, steel, machinery, pharmaceuticals, etc. The Mitsubishi Chemical Corporation, known as Japan’s largest comprehensive chemical manufacturer, began operations at its Ibaraki Plant in January 1971 at the Eastern Complex, which extends to the eastern part of Gono Pond in the industrial zone. Using naphtha as a raw material, the plant produces a wide variety of petrochemical products such as ethylene, polypropylene, ethylene oxide, and ethylene glycol. These are used in packaging film and containers for foods, in automobile parts, home appliance parts, household synthetic detergents, and other products, all of which are useful for our lives in many ways.
The plant has been pursuing the company’s kaiteki concept, aiming to realize safe, reliable, and highly efficient manufacturing of high-quality products. As a part of this effort, plant operators focus on control valves (hereafter “ valves”), which play an important role in plant operations. In order to quickly identify valve problems or warning signs and utilize that information for appropriate maintenance, the plant introduced azbil Smart Valve Positioners, which can detect the operating condition of the valves. In 2012, Azbil Corporation’s PLUG-IN Valstaff (hereafter “Valstaff”) control valve maintenance support system was installed, which monitors valves using the operating data collected by the positioners.
“Generally, valves are disassembled for inspection every 8 to 12 years,” explains Masayuki Yanagisawa, group manager of the Advanced Technology Group. “During the period between the cycles, only regular inspections are performed and a limited amount of information is available, so it is difficult to detect signs of deterioration and correctly understand the state of the valves. I thought, as an engineer, that if I had enough data, I could improve our operations further. By installing Valstaff, which monitors data sent from the positioners, it would be possible to quickly discover valve problems and warning signs and optimize maintenance.”
Selection of a cloud service that provides valve data in the desired way
In 2017, the plant began using a service in which Azbil analyzes valve condition using the data collected by Valstaff and reports the diagnostic results every six months. In 2018, using the data from this service, the plant started select-ing valves to be overhauled*1 when planning regular maintenance.*2 Moreover, the plant compared the data provided by Azbil with the actual degree of deterioration found during inspection to check the credibility of the service.
“We started using Valstaff to predict anomalies and optimize maintenance,” says Koji Fukuda, team leader in the Instrumentation Group. “But when it came to getting more detailed information on valves, engineers needed to extract the desired data from the asset system used for managing the data in order to analyze it. This process requires a good level of skills.”
Some of the engineers at the plant were not good at advanced use of the asset system and analyzing data.
“ There are engineers who cannot fully utilize the asset system, but if they see the data on operating conditions and signs of abnormality, they can decide whether the maintenance cycle can be a bit longer or whether overhauls are required. Until now, it was difficult for some of our personnel to collect such data and to obtain analytic results,” adds Mr. Yanagisawa.
Given these circumstances, Azbil suggested using the Dx*3 Valve Cloud Service, which provides the results of valve analysis and diagnosis on the Web. (The service is available in Japan only.) The service automatically sends the operating data collected by Valstaff to the cloud for analysis and diagnosis, and unlike the service that provides a report every 6 months, the user can check the condition of valves in detail at any time. On the Web, engineers can easily obtain valve data collected by Valstaff in the desired way, which solves the problem of not being able to fully utilize the asset system.
In June 2020, before the service was officially released, a trial operation began at an ethylene plant at the Ibaraki site.
“ This service makes valve diagnostic information more accessible to engineers. In response to inquiries from manufacturing departments, engineers can now provide explanations based on reports downloaded from the cloud. We are also compiling the knowledge obtained from Valstaff’s diagnostic data and from overhauls into a casebook for the plant,” says Shusuke Asahi, assistant manager of the Instrumentation Group.
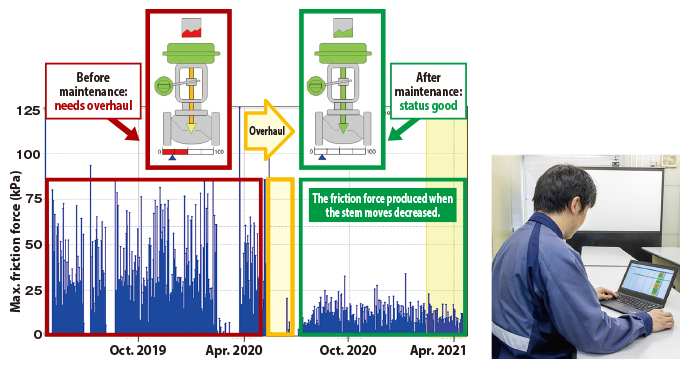
Because it is in the cloud, the user can access the Dx Valve Cloud Service using various devices such as laptops and tablets anytime from anywhere.
Fostering a mindset for data utilization and transforming existing maintenance processes
In the trial operation, the Ibaraki Plant enjoyed the desired effect, which was that every engineer responsible for plant maintenance accessed the diagnostic data on the valves and utilized the visualized information. With this successful result, full-scale use of the service for four plants began in April 2021. For the future, there are plans to apply the service to all 12 plants at the site as soon as possible.
“Because information on each valve is provided on the Web, engineers can check in-depth analyses of valves even from home. I feel that we may be able to create a new way of working,” comments Mr. Asahi.
“It is important to make data visible in this way, and I feel that it is necessary to improve the skills of engineers so that the data can be used effectively. Azbil’s staff, which is familiar with the plants, provides us with consulting services regularly and gives us suggestions for improvement. I feel that this kind of communication is very important,” adds Mr. Fukuda.
“With this initiative, we have established a system to further utilize the data related to valve maintenance. Many devices at the site that support production are equipped with smart sensors. In the future, we would like to build a system for concentrating data from these sensors into the cloud so that it can be shared and utilized by the entire plant, in order to make operation safer and more stable. We are looking forward to further suggestions from Azbil for realizing such a future,” says Mr. Yanagisawa.
Valstaff is a trademark of Azbil Corporation in Japan.
glossary
*1 Overhaul
To disassemble a valve during regular maintenance or at another time to make necessary repairs, etc.
*2 Regular maintenance
Large-scale inspection and repair work that is regularly carried out at production facilities and plants.
*3 Dx
An abbreviation for “diagnosis” in the field of medicine. Azbil uses this phrase to imply that the service will enable the customer to always use valves safely by understanding whether or not their condition is sound.
Learn about the customer
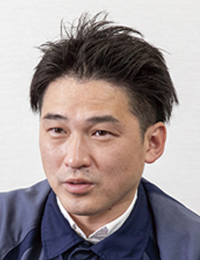
Group Manager
Advanced Technology Group
Maintenance and Engineering Department
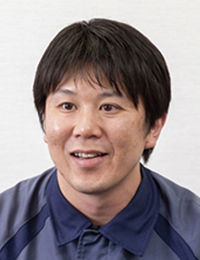
Assistant Manager
Instrumentation Group
Maintenance and Engineering Department
Plant Accreditation Inspection Department
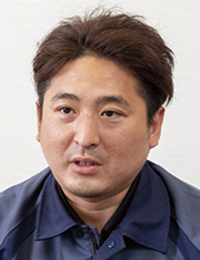
Team Leader
Instrumentation Group
Maintenance and Engineering Department
Plant Accreditation Inspection Department
Mitsubishi Chemical Corporation, Ibaraki Plant
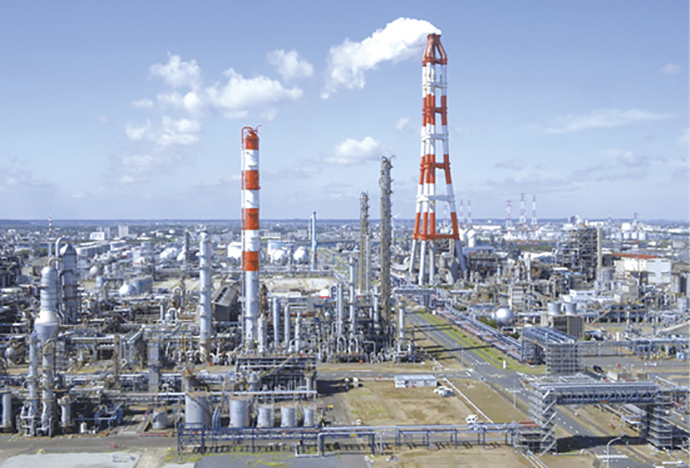
Mitsubishi Chemical Corporation, Ibaraki Plant
- Location: 17-1 Towada, Kamisu-shi, Ibaraki Prefecture
- Start of operation: January 1971
- Products: Basic chemical products including ethylene, polyethylene, ethylene oxide, ethylene glycol, propylene, polypropylene, cumene, acetone, phenol, and benzene.
This article was published in July 2022.