Shinyo Sanso Co., Ltd. Nitta Plant
Shinyo Sanso, a supplier of industrial gases such as oxygen, nitrogen, and argon, has implemented multi-variable model predictive control to optimize the use of human assets involved in plant operations. This has enabled the automation of production processes that were previously adjusted manually. Minimizing human intervention in operations and significantly reducing the workload for operators has created an environment where they can take on new tasks such as maintenance.
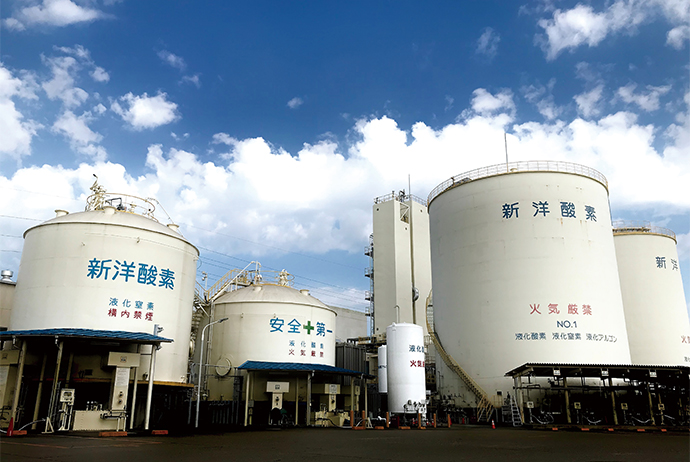
Factories and Plants Chemicals Electric Power and Gas Energy Efficiency Operation Improvement Industrial Automation Control and Monitoring Systems and Software
Products/Services Provided
Efforts to streamline plant operations and automate production processes
Shinyo Sanso Co., Ltd., located in Ota, Gunma Prefecture, northwest of Tokyo, began operations as an air separation plant in 1971 and has been supplying industrial gases such as oxygen, nitrogen, and argon to businesses in the industrial and medical sectors in northern Kanto and neighboring areas since then. Currently, it manufactures and supplies industrial gases as a joint production company funded by four companies: Taiyo Nippon Sanso Corporation, Koike Sanso Kogyo Co., Ltd., Air Liquide Japan G.K., and Kanto Ekisan K.K. It has continuously expanded and upgraded its facilities to strengthen its production system in response to the growing demand for gas due to advancements in industrial technologies and products.
In particular, since 1992, the company has adopted field devices such as control valves and transmitters made by Azbil Corporation, and in 2015 it replaced its old foreign-made DCS*¹ with Azbil's harmonized automation system, Harmonas-DEO™. Additionally, it has introduced the Knowledge Power™ operation support automation package and has been working to automate operations that had previously been performed manually.
“The full-scale effort for automation using Knowledge Power began in earnest in 2020 when the COVID-19 pandemic led to growing demand to minimize human contact. Furthermore, with the number of workers decreasing across society, it became important for our company to consider how we could reduce the amount of labor and manpower required for plant operation,” says Yoshinori Watanabe, Senior Vice President and Plant Manager for Shinyo Sanso Co., Ltd’s Nitta Plant.
Meanwhile, Taiyo Nippon Sanso, one of the parent companies, is building a system to remotely monitor and control the operating status of its own and subsidiary plants from a central location. In preparation for this, Shinyo Sanso, which will be monitored, also needed to reduce labor by further automating its production processes.
Introducing multi-variable model predictive control to automate plant operations
Knowledge Power is software that standardizes the tacit knowledge of operators involved in operations and automates procedures to support stable operations. For example, it focuses on creating sequential workflows, such as performing certain processes after a set number of minutes. However, when the company applied automation using Knowledge Power in liquid oxygen production, there were issues and control did not reach its set goals as intended.
“In our process, for example, the same action could produce results one second later in some cases or one hour later in others, so there were variations depending on the circumstances. Operators needed to be present to change settings and perform other operations, so our goals for automation, enabling remote monitoring and control, were not fully met,” says Atsushi Nagai, a production manager at Shinyo Sanso Co., Ltd.’s Nitta Plant.
It was difficult for Knowledge Power, which operates according to fixed procedures, to handle such processes, so the company turned its attention to advanced control. In response, Azbil proposed the multi-variable model predictive control SORTiA™-MPC in June 2023. Multi-variable model predictive control predicts the behavior of a target process using a model and stabilizes the plant based on that prediction. It was applied not only to steady-state operations but also to the automation of non-steady-state operations.
“Specifically, it provides feedback on the operational status every 15 seconds while predicting one to two hours ahead. It makes small corrections based on the situation, compensating for any deviations, to ensure that the plant’s processes behave in the required manner, achieving operation as though a human were in charge,” says Mr. Nagai.
To apply SORTiA-MPC, Azbil conducted interviews with onsite staff and event analysis based on accumulated operational data to identify issues. Then, the existing operating processes at Shinyo Sanso were examined in detail, and engineering staff modeled and tuned them. Onsite application work was completed in June 2024.
“Azbil’s personnel had extensive knowledge about the air separation equipment used in gas production, and even when we explained things to them in abstract terms during our interviews, they were able to accurately grasp our intentions and properly implement them in the model,” says Koichi Sekine, an assistant manager of production at Shinyo Sanso Co., Ltd.’s Nitta Plant.
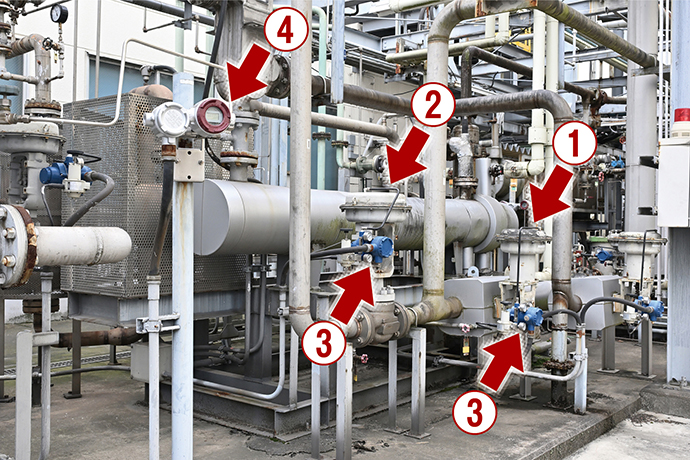
An eccentric rotary control valve (①) that adjusts temperature installed on argon production equipment, an electric top-guided single-seated control valve (②) that adjusts pressure, and smart valve positioners (③). The gauge pressure transmitter (④) measures the pressure at the compressor inlet of the suction tank.
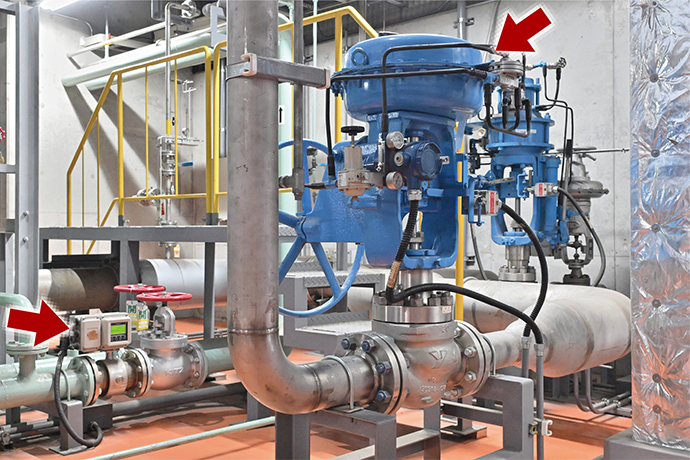
A top-guided type single-seated control valve (right) that adjusts the pressure of the oxygen gas compressor and an electromagnetic flow meter MagneW™ FLEX+ (left) that measures the flow rate of cooling water.
Using the time saved through automation to acquire new skills
By applying advanced control, Shinyo Sanso has been able to push forward with the automation of plant operations, something that had been previously difficult to achieve. Additionally, they have optimized the alert output, reducing the burden on operators responding to alerts. By dividing control tasks, the automation of the entire process has progressed: Knowledge Power is used for processes that do not require predictive control, such as starting and stopping equipment, and SORTiA-MPC is used for those that require more advanced control.
“Before we moved towards automation, operators told us they were worried about leaving operations unattended. Now, they are increasingly comfortable entrusting operations to SORTiA-MPC,” says Mr. Nagai.
“This automation has reduced the routine work of our operators, and the time gained is being used to acquire knowledge in new areas of maintenance,” says Mr. Sekine.
These automation efforts have also laid the groundwork for remote monitoring and control that Taiyo Nippon Sanso is promoting within the group.
Going forward, Shinyo Sanso plans to further improve the precision of the advanced control system it has adopted in this project. They also intend to expand its application to the total automation and optimization of plant operations.
“Azbil supplies us with a complete range of products, from various field devices to DCS and advanced control. They are well-positioned to handle the big data related to our operations, so I believe they will be able to respond effectively to such initiatives. We look forward to their future proposals,” says Mr. Watanabe.
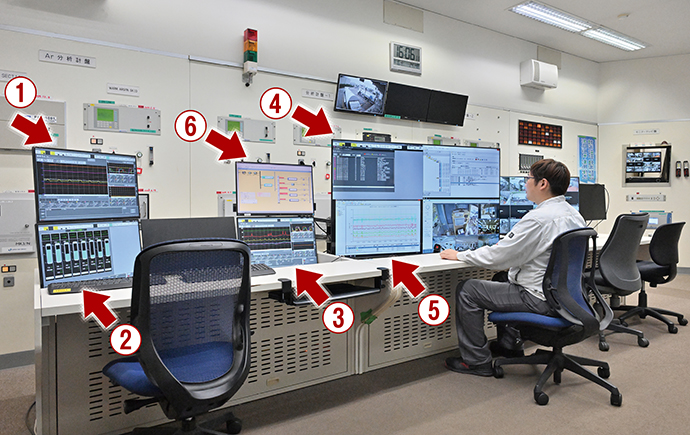
Monitor screens for the DCS Harmonas-DEO (①, ②, ③, ④), SORTiA-MPC (⑤), and Knowledge Power (⑥) installed in the central monitoring room.
*Knowledge Power, SORTiA, and MagneW are trademarks of Azbil Corporation in Japan.
glossary
*1. Distributed control system (DCS)
A dedicated system for monitoring and controlling the manufacturing processes and production equipment of plants and factories. To achieve an even distribution of load, the DCS manages the functions of each device over a network, resulting in safety and excellent maintainability.
Learn about the customer
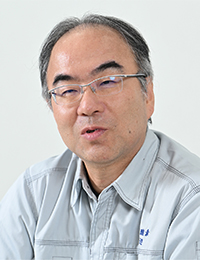
Senior Vice President
Plant Manager
Nitta Plant
Shinyo Sanso Co., Ltd.
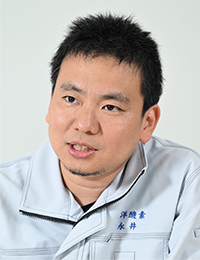
Manager
Production
Nitta Plant
Shinyo Sanso Co., Ltd.
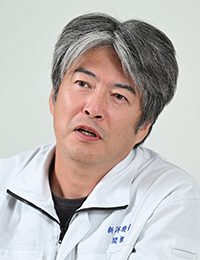
Assistant Manager
Production
Nitta Plant
Shinyo Sanso Co., Ltd.
Shinyo Sanso Co., Ltd. Nitta Plant
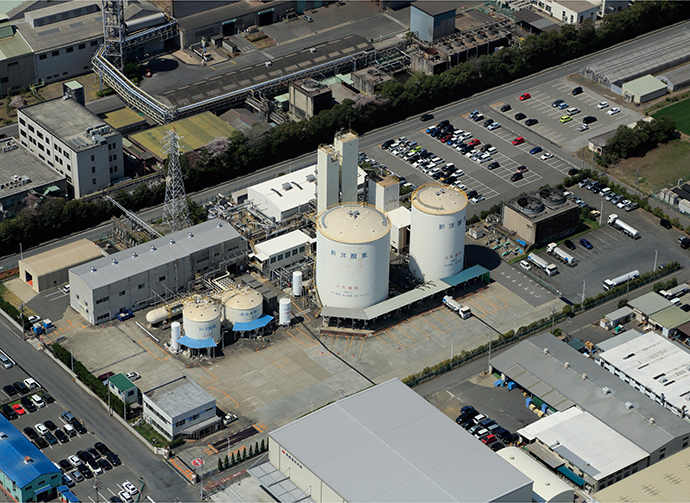
- Location: 337 Nitta Sorimachi-cho, Ota, Gunma
- Establishment: March 1, 1971
- Business activities: Manufacture and sales of various gases such as oxygen, nitrogen, and argon
This article was translated from the Japanese version.
This article was published in February 2025.