PT. Aspex Kumbong
PT. Aspex Kumbong is a paper manufacturing company in Indonesia. In preparation for a likely rise in electricity rates, its Bogor Factory has been promoting energy conservation. After the factory received an energy conservation diagnosis, it started to use Japan’s advanced energy-saving technology. Compressor control and air piping at the Bogor Factory were reviewed and renovated, resulting in higher energy savings than expected.
Factories and Plants Paper and Pulp Energy Efficiency Industrial Automation Control and Monitoring Systems and Software
Products/Services Provided
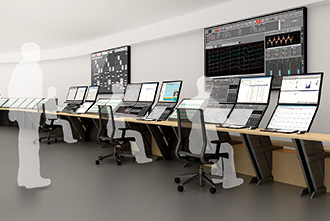
Compressor optimization control ENEOPTcomp
Dealing with a steep rise in the electricity bill becomes an urgent management issue
PT. Aspex Kumbong is a paper manufacturing company established in 1983, and is a member of the Korea-based Korindo Group. The company is located in Cileungsi in the suburbs of Jakarta, West Java, Indonesia. Its Bogor Factory manufactures paper for newspaper, books, notebooks, and telephone books as well as printer paper, and has a production capacity of 420,000 tons per year. The factory also has a production line for producing deinked pulp (DIP) from paper waste.
Formerly, Indonesia followed a policy of using government budget to keep electricity rates low for industrial users and household consumers. However, for reasons such as a recent rise in fuel costs, the government changed its policy. Rates for large consumers of electricity like Aspex Kumbong and other major companies have increased since the spring of 2014, resulting in an increase of as much as 65 % in some cases.
According to Mr. Bongki Choi, General Manager of the company’s Electric & Power Plant Department, “Conservation of energy has been a pressing management issue for our company. A few years ago, we implemented our own energy-saving measures, such as the addition of inverters for the various rotating machines (water feed pumps, etc.) required for operating the paper machines*1 in Bogor Factory. However, when the cost of electricity rose in 2014, we felt the need for further energy efficiency.”
While the company was seeking a means to further reduce power consumption, PT. Azbil Berca Indonesia, Azbil Corporation’s subsidiary in Indonesia, proposed the use of an energy-conservation diagnosis program.
After Azbil conducted thorough site research, its energy-conservation technology was installed
A one-week long field investigation and energy conservation diagnosis were conducted at Bogor Factory at the end of September, 2013. Azbil Berca Indonesia conducted interviews at the factory to obtain information on actual equipment operating and control conditions and energy consumption.
Based on analyses of the operating data and other information collected at the site by Azbil Berca Indonesia, it was estimated that optimizing the control of compressors would achieve a significant reduction of 6.4 % in electricity consumption. Aspex Kumbong decided to install the ENEOPT™comp compressor optimization control proposed by Azbil, and the necessary work took place at Bogor Factory from April to July in 2014.
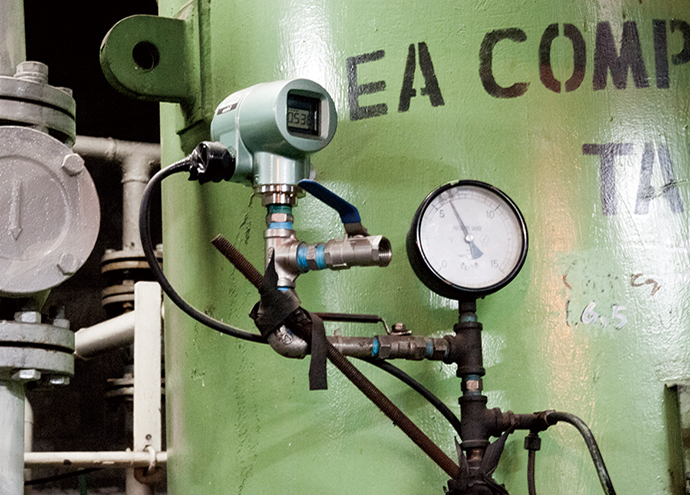
Compressed air from compressors is temporarily stored in the air surge tank. A Bravolight™ pressure sensor measures the pressure inside the tank, allowing control of the number of compressors in operation according to the demand for air from the manufacturing lines.
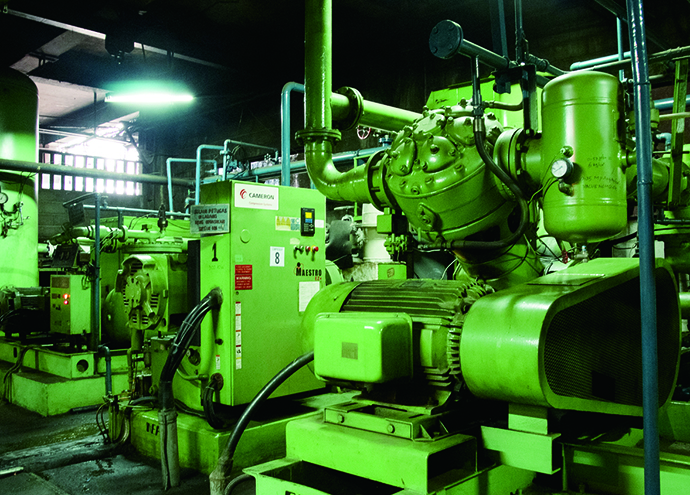
Reciprocal compressor, one of the 14 compressors in the factory.
An actual reduction in electricity use exceeding the energy diagnosis estimate
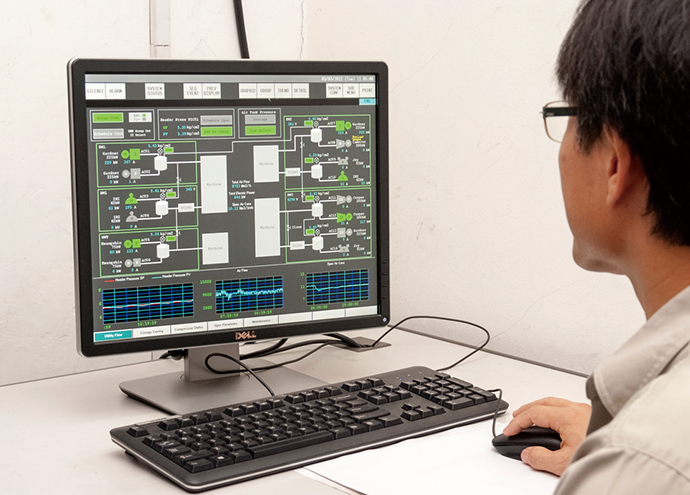
Harmonas-DEO in the central monitoring room.
At the time, Bogor Factory was operating three paper machines and 14 compressors, grouped into sets of two for the purpose of backup. The renovation project achieved integrated control of the compressors for all paper manufacturing lines, instead of separate control for each paper machine, by connecting the air piping of the manufacturing lines. Moreover, the newly installed system controls the number of operating compressors depending on the demand for air, as determined by measuring the pressure inside an air surge tank. Incorporation of the system to control the number of operating compressors initially resulted in the continuous operation of seven compressors, but improvements were made so that four or five operating units were able to supply the compressed air needed by the manufacturing lines. In order to provide optimum control of the number of units operating, it was critical to understand the characteristics of each type of compressor in detail. Different types of compressors—such as turbo, reciprocal, and screw—were used in the factory. “Azbil can take advantage of advanced know-how accumulated over many years, so they were able to provide operation control suitable for each equipment model. As a result, we successfully achieved a large 8.5 % reduction in electricity consumption, exceeding the figure of 6.4 % estimated during the diagnosis,” says Mr. Choi.
Previously, each compressor installation site in the factory was attended by three or four workers around the clock. For more effective and efficient compressor monitoring, Azbil’s Harmonas-DEO™ monitoring and control system was installed. The system enabled integrated monitoring of compressor and equipment operating conditions from a central monitoring room, eliminating the need to station workers at each compressor installation site, thus significantly reducing the workload and improving productivity.
The Bogor Factory plans to make further investments to achieve greater energy efficiency on production lines that do not include compressors. “We are very happy with Japan’s sophisticated energy-saving technology and the detailed and extensive service provided by Azbil Berca Indonesia throughout the project. I look forward to hearing future energy-conservation proposals backed by Azbil’s extensive knowhow,” says Mr. Choi.
ENEOPT and Bravolight are trademarks of Azbil Corporation.
Harmonas-DEO is trademarks of Azbil Corporation.
glossary
*1 Paper machine
A machine for manufacturing paper. It is composed of a forming section (to create a sheet), a press section (to squeeze out excess water), a drying section, and a calender section (where paper is rolled).
Learn about the customer
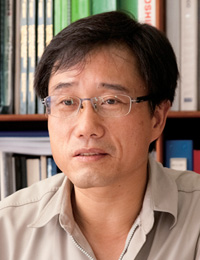
General Manager
Electric & Power Plant Department
PT. Aspex Kumbong
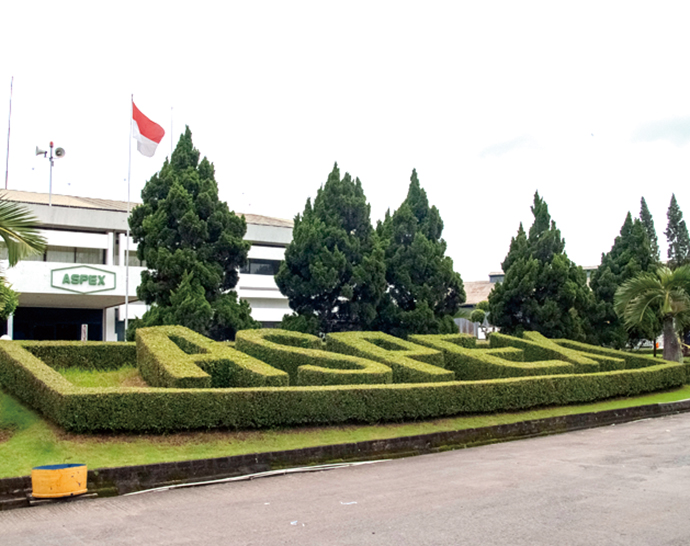
PT. Aspex Kumbong Bogor Factory
- Location: Jl. Raya Narogong KM. 26, Cileungsi, Bogor 16820, Jawa Barat, Indonesia
- Established: 1983
- Business line: Manufacture of paper for newspaper, books, notebooks, telephone books, etc.
This case study was published in the 2016 Vol.2 issue of the azbil Group's corporate magazine, azbil.