savic-net™FX Building Management System
Makino Milling Machine Co., Ltd. Fuji-Katsuyama Plant
Makino Milling Machine Co., Ltd., is a machine tool manufacturer with over 80 years of history. Their machining center manufacturing plant needed strict temperature control. When upgrading its central monitoring system, the company implemented unified management of equipment at the Fuji-Katsuyama plant. The outdoor air intake control was improved and variable speed drives were introduced in air handling units. Through Azbil’s proposals for improvements and energy savings based on accumulated operational data, operator load was reduced and the amount of energy saved was 170% of projections. The accuracy of indoor temperature control was also improved from ±1.5 °C to ±1 °C, leading to stable temperature and energy savings.
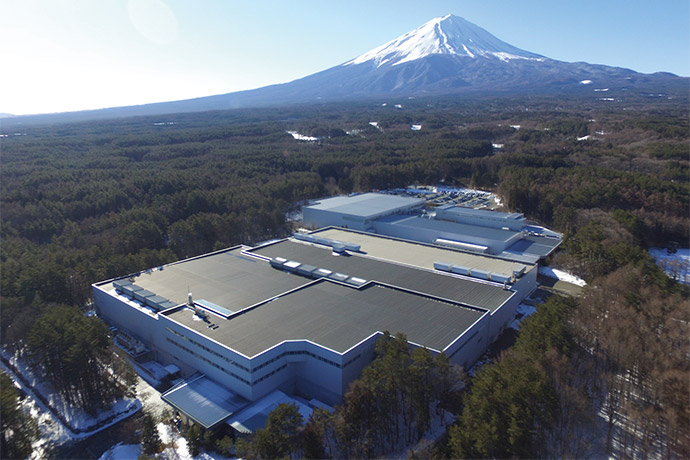
Building Solutions Other (Markets and Industries) Energy Efficiency Energy Management Cost Reduction Operation Improvement Building Management Systems Building Energy Management
Products/Services Provided
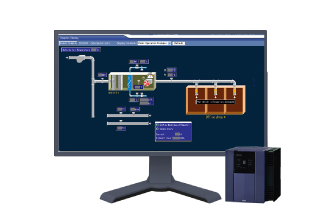
A philosophy of “Quality First”
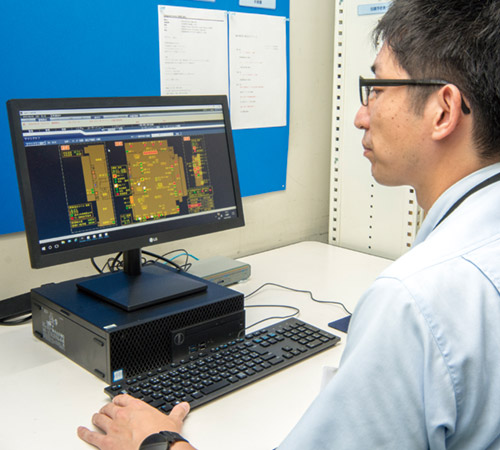
Central management of the HVAC equipment at the Fuji-Katsuyama plant is done by savic-net FX. On this screen, the status of the equipment at the Fujiyoshida and Narusawa plants can be checked, and the equipment can be remotely operated.
Founded in 1937, Makino Milling Machine Co., Ltd., is one of the leading machine tool manufacturers in Japan, and is known for developing Japan’s first numerical control (NC) milling machine in 1958. The company pursues its philosophy of “Quality First” not only in terms of all its products and services, but also as the ideal for its organizations and employees.
The company’s domestic plants are located in Kanagawa Prefecture in the city of Atsugi and in Yamanashi Prefecture in the areas of Fujikawaguchiko, Fujiyoshida, and Narusawa. In these plants the machine tools called machining centers, which can continuously perform various metalworking tasks, are manufactured. Makino’s machining centers make the large metal parts of automobiles, aircraft, etc., that require high accuracy, and they are highly regarded by companies worldwide. Currently, the company is expanding its global business in Europe, the United States, and Asia, and is also focusing on ESG*1 and SDG-related initiatives for achieving a sustainable society.
Located at the foot of Mt. Fuji, the Fuji- Katsuyama plant started in 1987 and now has six buildings. Since the construction of the first one, Makino has used measurement and control equipment from Azbil Corporation (Yamatake-Honeywell Co., Ltd., at that time), and Azbil has overseen its maintenance for years.
When Azbil’s savic-net™FX building management system was introduced for central monitoring in Building 5 in 2007, systems in Buildings 1 and 2 were also replaced. Also, construction in 2018 allowed HVAC equipment status, temperature and humidity to be managed by the central monitoring system. Thus, unified management of the HVAC equipment in the plant was achieved.
“Previously, staff had to go where equipment was installed to change the temperature but the new central management led to improved accuracy of temperature control and reduced operation manhours,” said Atsushi Watanabe, Katsuyama Maintenance Team Leader.
“Accuracy is essential for the production of large machine tools,” explains Equipment Management Group Manager Shigenori Hada. “For example, iron expands 12 micrometers per meter for every 1 ℃ rise. Since temperature affects the material’s dimensions, heat inside the plant can affect product quality.”
Since production in the plant generates a considerable amount of heat, the company aimed to ensure a better indoor environment and product quality by constantly monitoring the indoor temperature and keeping it constant.
Power savings of 170%
In 2018, once the plant had become centrally managed, Azbil used operational data from the plant’s HVAC equipment to make energy- efficiency proposals, including the installation of variable speed drives (VSDs) for fans in the air handling units (AHUs) and measures to improve the control of outdoor air intake.
The weather around Mt. Fuji is cool all year so the plant has actively used outdoor air for cooling. But that would freeze the AHU coils when the outdoor temperature was too cold. So, to prevent AHU failure, the safety circuits were often activated, causing the AHUs to stop.
“But if the AHUs stop, temperature in the plant will rise. We had to deal with such issues manually for years until Azbil helped,” says Yusuke Udagawa of the Katsuyama Maintenance Team.
The stored operational data was analyzed to determine the threshold just before the AHUs stop to prevent freezing, and the damper opening for outdoor air intake was finely tuned. Also, the temperature inside the plant could be kept constant if the airflow was not always at the maximum rate, so VSDs were introduced for the AHU fans, achieving a significant reduction in power consumption.
As a result, yearly power consumption was cut by 1,403,471 kWh compared to the previous year, which is an achievement rate of 170% compared with Azbil’s targets.
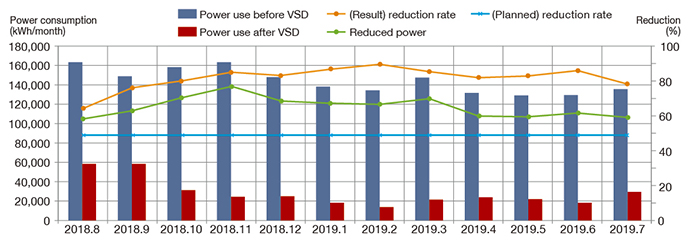
Comparison of plant power consumption before and after VSD introduction (1 year after delivery)
A partner for energy efficiency
The factors that brought about dramatic energy savings are long-term accumulation of operating data, monitoring and analysis of that data, and improvements in the form of appropriate adjustments based on the analysis. Azbil personnel analyze the data collected at Makino every day to determine equipment and control trends. In regular meetings with the Makino staff members managing the equipment, Azbil plans improvements and provides reports and proposals.
“I am very satisfied with Azbil’s after-sales support,” says Mr. Udagawa. “If I have a concern, Azbil provides us with countermeasures on their next visit. Also, the accuracy of temperature control in Buildings 1 and 2 was improved from ±1.5 ℃ to ±1 ℃.”
The system at the Fuji-Katsuyama plant is connected via a network to Makino’s other bases at Atsugi, Fujiyoshida, and Narusawa.
“From the Fuji-Katsuyama plant, we can check and operate monitored points for the Fujiyoshida and Narusawa plants. So if an alarm is generated, we can make an initial response from here,” says Mr. Watanabe.
In appreciation of these achievements, the company is considering expanding the unified management of equipment and energy-efficiency measures to other bases.
“It was a big success that energy savings were achieved while the temperature in the plant where precise work is required was strictly controlled,” says Mr. Hada. “Since a significant effect was obtained, we are planning to expand the measures to other bases as a matter of course. We are looking forward to further proposals from Azbil as our partner in plant operation improvement.”
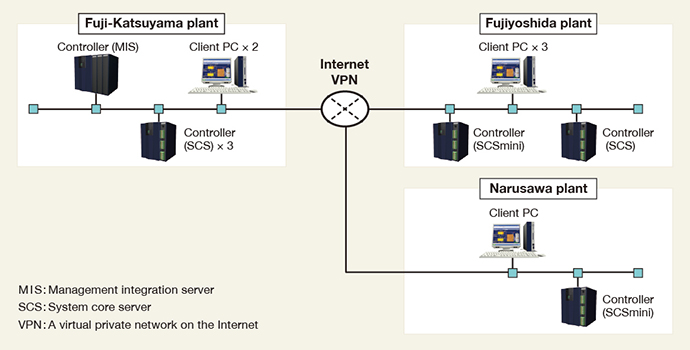
System configuration
glossary
*1 ESG
An abbreviation for the words environmental, social, and governance; the idea that these three viewpoints are necessary for the sustainable growth of society and of companies.
Learn about the customer
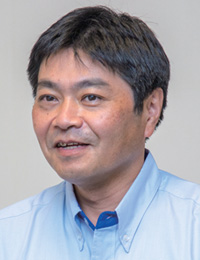
Production Engineering Dept.
Equipment Management Group
Group Manager
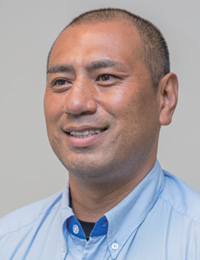
Production Engineering Dept.
Equipment Management Group
Katsuyama Maintenance Team
Leader
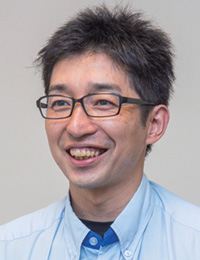
Production Engineering Dept.
Equipment Management Group
Katsuyama Maintenance Team
Makino Milling Machine Co., Ltd. Fuji-Katsuyama Plant
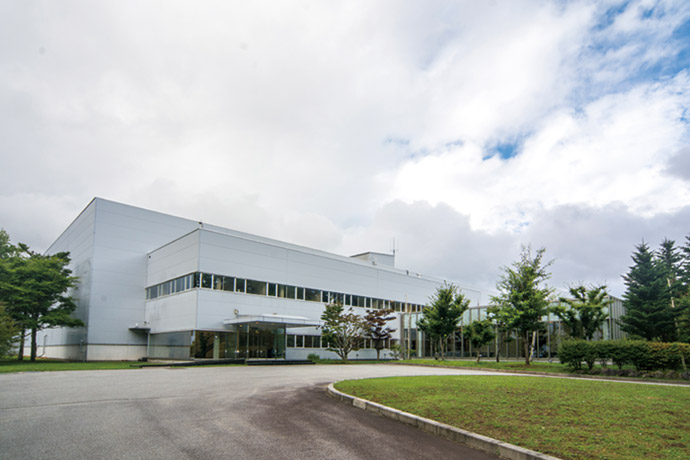
Makino Milling Machine Co., Ltd. Fuji-Katsuyama Plant
- Location: 3560-1 Katsuyama, Fujikawaguchiko-machi, Minamitsuru-gun, Yamanashi Prefecture
- Opened: November 1987
- Business: Manufacturing, sales, and export of machine tools (machining centers, NC electric discharge machines, NC milling machines, milling machines, CAD/CAM, etc.)
This article was published in April 2022.