Daikin Industries, Ltd., Kashima Plant
The Daikin Industries Kashima Plant, which produces fluorochemical products for a industry, has recently focused on effective maintenance of control valves. The failure of a control valve has a greater impact on production than the failure of other instrumentation equipment used in plant operations, and control valves require large repair costs even in the course of regular maintenance. By switching from periodic maintenance to condition-based maintenance of these valves, the Kashima plant has significantly reduced maintenance costs and has established a system for quick handling of minor malfunctions and warning signs of future problems.
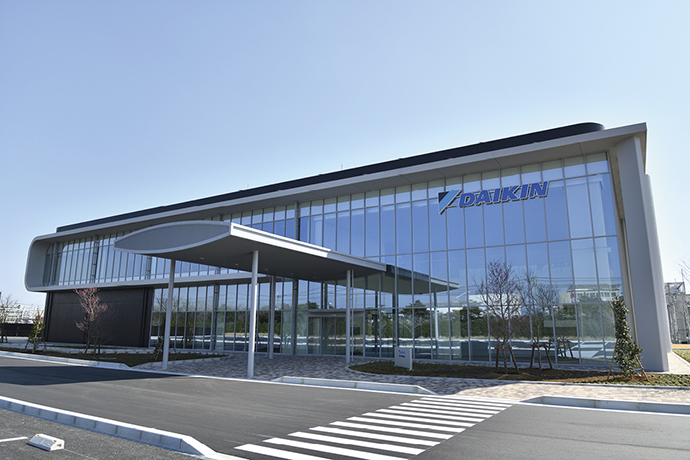
Factories and Plants Chemicals Cost Reduction Quality Control Reliable Operation Maintenance Support Cloud, IoT, and AI Industrial Automation Control and Monitoring Systems and Software Control Valves and Actuators Life Cycle Support
Products/Services Provided
Seeking the optimal maintenance cycle for valves
Daikin Industries, Ltd., conducts business in more than 160 countries around the world, providing packaged air conditioners, room air conditioners, and building air conditioners. Known as a global manufacturer of both refrigeration and air conditioning equipment and of coolants, the company is also expanding its chemical business by developing, manufacturing, and supplying fluorochemical products. The Kashima Plant is responsible for the chemical business.
In June of 2021, Daikin Industries completed construction of its Integrated Production Center at the Kashima Plant. Aiming to improve quality and productivity, all of the people, organizations, and information related to plant operation, equipment, and production management that had been dispersed around the plant were integrated into the same facility.
“In 2005 our company started efforts for production innovation in the chemical business, and we have been proceeding with the steps of stabilization, standardization, and integration. Our plant has begun implementing integration, the final stage of innovation,” explains Yuuji Onodera, section manager of the Engineering Department.
As part of this initiative, the plant has set a goal to triple productivity per employee involved in manufacturing by 2025 compared to 2010. To meet this goal various measures are being implemented in each area of the manufacturing site. One such measure is the optimization of the control valve maintenance cycle.
“For control valves, we used to use the time-based maintenance (TBM)*1 method. Basically, valves were overhauled in regular maintenance,*2 at which time they were disassembled for inspection and maintenance. However, upon looking inside these valves, we found that many of them had no problems at all. I have to say that this kind of uniform timebased inspection and maintenance was a big waste in terms of cost,” says Mr. Onodera.
Diagnosing a large number of shutoff valves
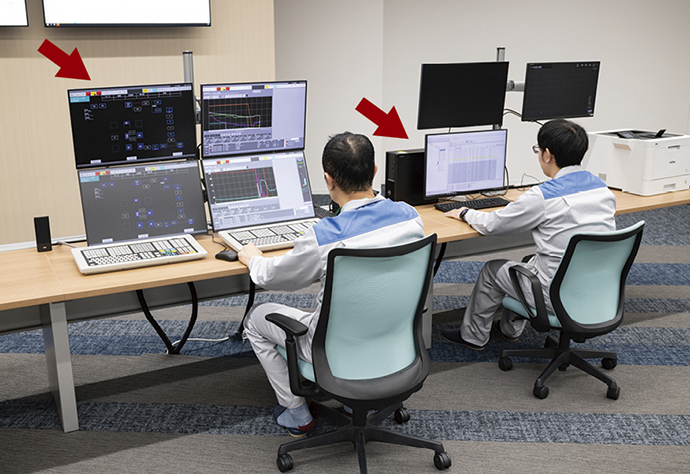
Monitoring screens for Azbil’s DCS*5 system introduced as a DCS (left) and for the control valve maintenance support system (right).
The Kashima Plant decided to switch from TBM to condition-based maintenance (CBM),*3 which is conducted based on the state of the valves, and the plant adopted Azbil Corporation’s Control Valve Maintenance support system as a tool for effectively implementing CBM. This system analyzes and diagnoses various data on valves collected by smart valve positioners in order to identify malfunctions and warning signs of problems at an early stage.
“The sales release of the 700 series smart valve positioners, which incorporate a pressure sensor, was also a deciding factor in introducing the system. We thought that the diagnostic accuracy we had hoped for would finally be achieved with these positioners, since the system has various diagnostic parameters,” says Kenichi Kamogawa of Kashima Engineering Group.
The plant gradually increased the number of 700 series positioners to implement the Control Valve Maintenance support system. The system was introduced in April of 2017, when a certain number of the positioners were installed on operating valves, and analysis and diagnosis of the valves’ condition began. About 120 control valves in the monomer and chemical production facilities are now connected to the system.
“At first, only the control of the of the valves, and the plant adopted Azbil Corporation’s Control Valve Maintenance support system as a tool for effectively implementing CBM. This system analyzes and diagnoses various data on valves, and the plant adopted Azbil Corporation’s Control Valve Maintenance support system as a tool for effectively implementing CBM. This system analyzes and diagnoses various data on valves were subject to diagnosis by the system. However, we have as many as 1600 shutoff valves, in addition to 900 control valves. Therefore, we asked Azbil to include the shutoff valves in the analysis and diagnosis. “Visualizing” the operation of shutoff valves for CBM gave us a hint for improvement and led to more effective maintenance,” explains Masumi Yoshida of Kashima Engineering Group.
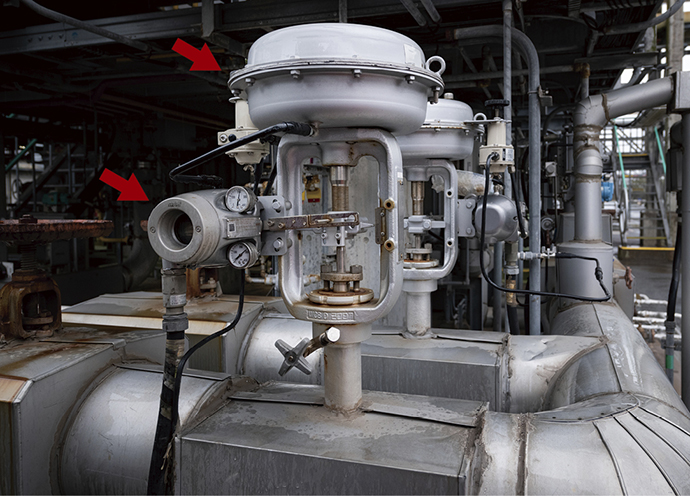
Azbil’s top-guided single-seated control valve equipped with a 700 series smart valve positioner (left). This valve controls the flow rate of steam sent into a furnace to heat melted raw material.
Valve diagnosis to decide the timing of maintenance dramatically reduced costs
As a result of introducing the control valve maintenance support system, the Kashima Plant is making progress in implementing CBM for its valves. Along with the system, the plant also adopted the Dx*4 Valve Basic Service, which provides valve analysis and diagnosis results in a yearly report. Since the condition of the valves is shown quantitatively, the plant is now able to make a data-based judgment on whether to carry out an overhaul or other maintenance.
“For the valves that the system recommended to overhaul, we further analyzed the data in-house and improved the accuracy. We were able to eliminate maintenance on about 60% of the valves subject to inspection in 2021 and about 80% of them in 2022. As a result, inspection and maintenance costs were cut by approximately 34 million yen over two years,” says Mr. Kamogawa.
The system contributes not only to identifying the valves that really need maintenance, but also to detecting warning signs of failure in operating valves.
“We once received an investigation request from our manufacturing section saying that there was a fluctuation in the flow rate. Although no particular abnormalities were found by visual inspection, we were able to identify a minute operational abnormality of 0.1% using the control valve maintenance support system,” says Mr. Yoshida.
“We then cleaned the sliding part of the valve and checked the result with the system. The deviation was smaller and the amount of fluctuation in the flow rate was smaller. We were able to perceive minute fluctuations that could not be identified before, and that prevented problems that could have occurred if we continued to use the valve without taking any action. If we can check with the system for signs of abnormality that our personnel could not find before, we can minimize losses by taking corrective action on the equipment before a serious failure occurs,” adds Mr. Kamogawa.
In the future, the plant plans to gradually incorporate more control and shutoff valves operating in the monomer and chemical production facilities into the control valve maintenance support system, and to use the system in new production facilities, further accelerating CBM for valves. Also under consideration is the collection of data from devices such as flowmeters and sensors to further support reliable plant operation and optimal equipment maintenance.
“We have also introduced Azbil’s online anomaly detection system for stable plant operation and are working hard to prepare for fullscale utilization of it. We have high expectations that Azbil, with its comprehensive knowledge and practical know-how on measurement and control, will continue to provide unique data utilization solutions,” says Mr. Onodera.
glossary
*1 TBM (Time Based Maintenance)
A maintenance method in which maintenance is performed periodically regardless of the condition of the equipment.
*2 Regular maintenance
Large-scale inspection and repair that is performed at regular intervals at various manufacturing factories and plants.
*3 CBM (Condition Based Maintenance)
A maintenance method in which maintenance is performed when signs of deterioration are identified in monitored equipment.
*4 Dx
An abbreviation for “diagnosis” in the field of medicine. Azbil uses this abbreviation to imply that the service will enable the customer to always use valves safely by understanding whether or not their condition is sound.
*5 DCS (Distributed Control System)
A dedicated system for monitoring and controlling the manufacturing processes and production equipment of plants and factories. To achieve an even distribution of load, the DCS manages the functions of each device over a network, resulting in safety and excellent maintainability.
Learn about the customer
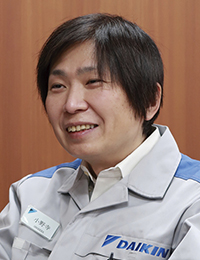
Section Manager
Engineering Department
Chemical Division
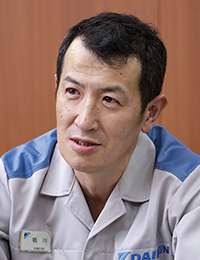
Kashima Engineering Group
Engineering Department
Chemical Division
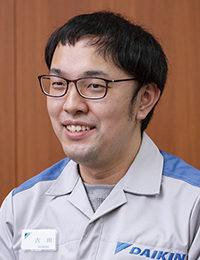
Kashima Engineering Group
Engineering Department
Chemical Division
Daikin Industries, Ltd., Kashima Plant
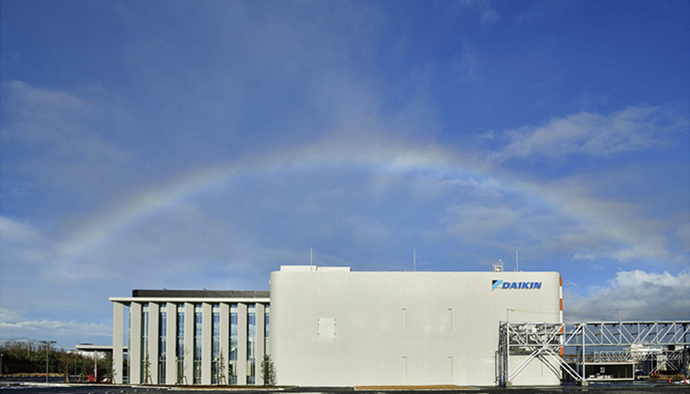
Daikin Industries, Ltd., Kashima Plant
- Location: 21 Sunayama, Kamisu, Ibaraki Prefecture
- Start of operation: April 1983
- Products: Fluoropolymers and fluorochemical products
This article was published in July 2023.