valve analysis and diagnosis services
Showa Denko K.K., Kawasaki Plant
Showa Denko’s Kawasaki Plant in Ogimachi boasts a long history of development and manufacture of organic and inorganic chemical products. In order to promote smart industrial safety using technology such as the Internet of Things (IoT), the company pays special attention to valves, which are indispensable for production. To optimize maintenance work and reduce costs, Showa Denko utilizes Azbil’s smart valve positioners, valve diagnostic systems, and valve analysis and diagnosis services provided by specialist engineers.
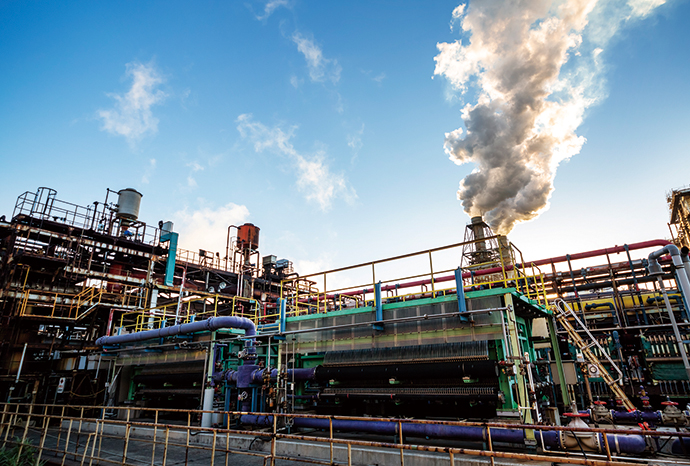
Factories and Plants Oil Refining and Petrochemical Chemicals Cost Reduction Reliable Operation Operation Improvement Maintenance Support Cloud, IoT, and AI Control Valves and Actuators Life Cycle Support
Products/Services Provided
A focus on valve maintenance, which accounts for most maintenance costs, for smarter operation
Showa Denko is involved in a variety of business areas, including petrochemicals, chemicals, inorganics, aluminum, and electronics. The Kawasaki Plant, the oldest of its operating plants, is located in three sections of the city, Ogimachi, Okawa, and Chidori, and is positioned as the company’s mother plant. It manufactures chemicals, including industrial products like ammonia and caustic soda, and industrial gases like nitrogen, hydrogen, and argon. In addition, in recent years, the company has been promoting chemical recycling of used plastics, which is attracting attention as an activity for a resource-recycling society.
“From a management perspective, there is a strong demand to promote smart plants in order to solve the personnel shortage and to pass on technology smoothly to the next generation of workers, while assuring the steady operation of the plant. So, we focus on the 4,000 to 5,000 valves that are operating at our plant,” says Tsuyoshi Hino, a group leader in the Engineering Department.
“As we expand our business overseas and compete globally,” adds Kaichiro Arita, an assistant manager in the department, “reducing maintenance costs is a major issue now more than ever, in order to increase corporate and product competitiveness. Valve maintenance in periodic inspections accounts for about 20% of our total maintenance cost for instrumentation equipment, and requires 1,000 man-hours a year. We thought that, if we could make our valve maintenance smarter, we could dramatically reduce costs and improve productivity.”
Valve diagnosis by specialist engineers, and a discovered anomaly not visible to human eyes
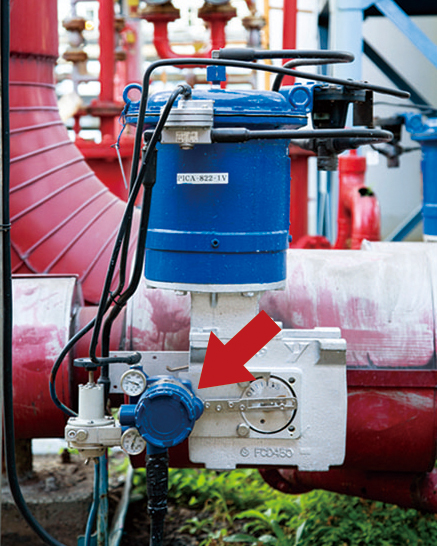
A smart valve positioner attached to an Azbil valve used to regulate hydrogen pressure in soda electrolysis equipment.
In discussions on making the plant smarter, Azbil proposed that the Kawasaki Plant use Azbil’s control valve maintenance support system and smart valve positioners as the basis for valve analysis and diagnosis, and the plant agreed.
One advantage for the plant was the fact that Azbil’s microprocessor-equipped smart valve positioners could be mounted on existing valves, including those made by other manufacturers. Valve operation data from the positioners is collected by the control valve maintenance support system utilizing IoT technology. The degree of valve deterioration and potential anomalies can then be checked easily with graphed data.
“Operation data on valves from any manufacturer can be collected, which enables us to visualize the operating status of all the valves in the plant. We decided that this was a very effective way to achieve a smarter plant,” explains Mr. Hino.
Valve operation data collected by the control valve maintenance support system is sent to Azbil’s remote center, where Azbil conducts a primary screening diagnosis, which originally was done every other month. If the result of diagnosis is “overhaul recommended,” the Kawasaki Plant asks Azbil for a detailed analysis and diagnosis as necessary. Backed by many years of experience in valve diagnosis, Azbil can provide valve analysis and diagnosis by specialist engineers for detailed items such as input-travel comparison and maximum operating speed. This service was the deciding factor in accepting Azbil’s proposal.
“Other companies also offered valve diagnosis, but Azbil’s proposal was different in that specialist engineers analyze the data using a wealth of knowledge and know-how. We would like to accumulate analysis techniques ourselves, so this service is the most important advantage for us,” says Mr. Arita.
At first, the Kawasaki Plant decided to try using Azbil’s products on a small scale. In August 2016, they selected 16 important valves in the soda electrolysis equipment at the Ogimachi site and started operation.
After introducing the smart valve positioners and control valve maintenance support system, they conducted a response test in which valve travel was changed gradually in 1% increments to check the operating status of the valves during a trial run after a periodic repair. Another manufacturer’s valve that controlled the hydrogen pressure was found to be hunting, as shown by a fine wavy travel signal. Although alarms on hydrogen pressure had been generated for some time, the cause could not be identified, but the result of diagnosis showed that it was probably caused by the valve. The Kawasaki Plant then asked the manufacturer for maintenance, and the manufacturer carried out an overhaul that included disassembly of the valve for cleaning and reassembly. After the overhaul, the plant checked the valve with the control valve maintenance support system and found that the hunting had stopped.
“If the valve had not been serviced, the problem could have affected the operation of the plant. We were able to find an abnormality that could not be identified by human eyes and that even the valve manufacturer’s specialist did not notice, because the control valve maintenance support system’s data indicated a possible problem,” explains Junichi Yoshitake of the Engineering Department.
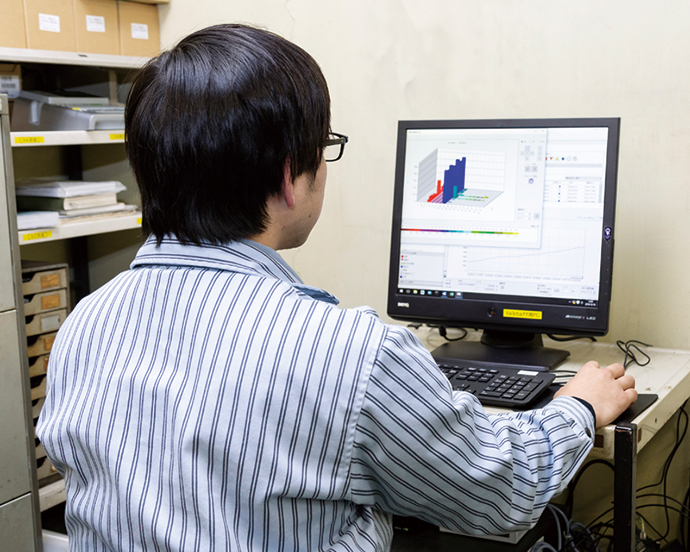
A monitor for the control valve maintenance support system installed in a local control room (LCR) near the plant. It is used to monitor the operating status of the plant. The operator can check the data on valve operation in easy-to-understand graphs.
Achieving a longer overhaul cycle by proper valve operating condition diagnosis
The valves that were diagnosed in this trial had previously been overhauled about once every two years. The Kawasaki Plant took all possible measures to maintain valves properly, and it seemed that some valves could have a longer overhaul cycle without problems. However, due to a lack of evidence, the plant did not extend the cycle.
“But now it is possible to check the status of each valve with data and obtain a basis for judgment,” says Mr. Yoshitake. “We were actually able to extend the overhaul cycle for two valves that had no problem at all.”
In June 2019, the Kawasaki Plant added 16 more valves to the number of diagnosed valves in the soda electrolysis equipment, with plans to carry out the primary screening diagnosis every six months.
“We learned that Azbil’s valve diagnosis is worth using and produces great results. Utilizing quantitative data on valve conditions obtained frequently and continuously, we can do predictive maintenance, which means taking appropriate measures before failure occurs. This contributes to stable operation of the plant and reduces costs,” says Mr. Arita.
“The larger the scale of installation, the greater the results, such as reduction in manhours,” adds Mr. Hino. “So we are increasing the number of diagnosed valves in the soda electrolysis equipment and are considering introduction of the system to other manufacturing equipment at the Kawasaki Plant. In addition, we share information with other plants. Seeing what we have accomplished, some other plants have installed the control valve maintenance support system.”
“We would like to create a work environment where all employees can do rewarding and high-value-added work by utilizing new technology. We have high expectations for Azbil’s support in the future, including assistance in making our plants smarter.”
Learn about the customer
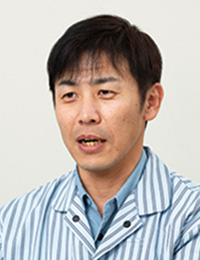
Group Leader
Electric and Instrumentation Group
Engineering Department
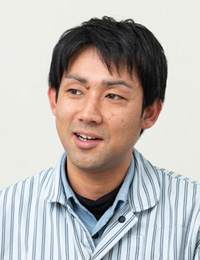
Assistant Manager
Electric and Instrumentation Group
Engineering Department
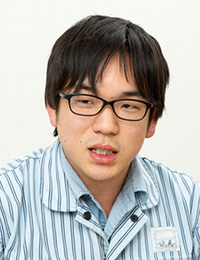
Electric and Instrumentation Group
Engineering Department
Showa Denko K.K., Kawasaki Plant
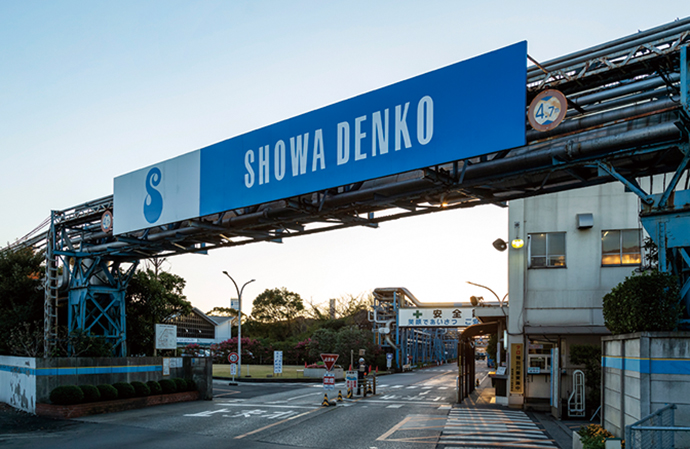
Showa Denko K.K., Kawasaki Plant
- Address: 5-1, Ogimachi, Kawasaki-ku, Kawasaki, Kanagawa Prefecture
- Beginning of Operation: 1930
- Business: Industrial products such as ammonia, caustic soda, and sodium hypochlorite; industrial gases such as nitrogen, hydrogen and argon; high-purity gas for electronic materials; food additives; cosmetic raw materials, etc.
This article was published in April 2021.